Скрепления для рельсошпальной решетки | Строительство и ремонт железных дорог
Скрепления АРС
В связи с тенденцией к сокращению затрат на обслуживание пути и снижению материалоемкости производства материалов ВСП, в последние годы все больше объектов строиться с применением скрепления АРС.
Анкерное промежуточное рельсовое скрепление АРС относится к числу бесподкладочных упругих скреплений и предназначено для использования на бесстыковом пути грузонапряженных линий магистральных железных дорог, в том числе высокоскоростных магистралях, а также метрополитенах.
![]() | 1 — Клемма 2 — Монорегулятор 3 — Подклеммник 4 — Анкер 5 — Изолирующий уголок 6 — Резиновая прокладка |
На путях ОАО «РЖД» скрепление АРС применяется как при капитальном ремонте главных путей так и при строительстве новых линий, в том числе скоростных.
![]() | ![]() |
Скрепления типа КБ
Типовым промежуточным скреплением для железобетонных шпал является раздельное клеммно-болтовое скрепление КБ, в котором рельс к подкладке прижимается жесткими клеммами.
Полностью себя оправдало применение скреплений КБ на бесстыковом пути в отношении применения прогрессивной технологии замены рельсов, разрядки температурных напряжений, обеспечения оптимальных условий температурной работы рельсовых плетей.
![]() | 1 — Закладная шайба 2 — Шпала 4 — Изолирующая втулка 5 — Плоская шайба 6 — Закладной болт 7 — Клемма 8 — Двухвитковая шайба 9 — Гайка 10 — Клеммный болт 11 — Прокладка под рельс 12 — Подкладка КБ |
В настоящее время скрепление КБ является самым распространенным на путях Октябрьской железной дороги.
Скрепления типа Д
Несмотря на широкое применение в строительстве железных дорог железобетонных шпал, не утратили свою актуальность и деревянные шпалы.
Деревянные шпалы применяются:
— при укладке в кривых малого радиуса для обеспечения устройства колеи шириной больше 1520 мм;
— на путях, где применение железобетонных шпал невозможно из-за воздействия агрессивных сред.
Самое распространенное скрепление с деревянными шпалами –. костыльное скрепление.
![]() | 1 — подкладка 2 — гайка стыкового болта 3 — шайба пружинная 4 — рельс 5 — накладка 6 — болт стыковой 7 — костыль путевой 8 — прокладка нашпальная. |
![]() | ![]() |
mk20.ru
Комплект скрепления КБ-65 высокого качества от компании ВСП74 в Челябинске
Типовым промежуточным скреплением для железобетонных шпал является раздельное клеммно-болтовое скрепление КБ, в котором рельс к подкладке прижимается жесткими клеммами, надеваемыми на клеммные болты, фигурные головки которых заводятся в пазы реборд подкладок. Под гайки клеммных болтов ставят упругие шайбы. Под рельс, на металлическую подкладку укладывают резиновую прокладку, для улучшения упругих свойств скрепления. Металлические подкладки укладывают на наклонную (для обеспечения подуклонки рельсов), заглубленную в тело шпалы на 15— 25 мм подрельсовую площадку. На бетон под подкладку укладывают для электро- и виброизоляции резиновую прокладку толщиной 6—8 мм. Благодаря этому осуществляется передача поперечных горизонтальных сил от подкладки через нашпальную прокладку на бетон, улучшаются условия работы закладных болтов и повышается стабильность ширины колеи.
Подкладка крепится к шпале закладными болтами. При этом головки болтов опираются на замоноличенную в бетон металлическую шайбу, которая при затяжке монтажных гаек равномерно распределяет нагрузку на бетон. Электроизоляция подкладок от шпал осуществляется нашпальной прокладкой и втулкой из текстолита, надеваемой на стержень закладного болта и заглубляемой в отверстие металлической подкладки.
Высота реборд подкладок КБ позволяет укладывать под рельс прокладки толщиной 12—14 мм для ре- гулировки рельсов по высоте, что особенно важно в зимний период. В других случаях это преимущество скреплений КБ используют для укладки под подошву рельса прокладок повышенной упругости.
Полностью себя оправдало применение скреплений КБ на бесстыковом пути в отношении применения прогрессивной технологии замены рельсов, разрядки температурных напряжений, обеспечения оптимальных условий температурной работы рельсовых плетей.
Недостатками конструкции скреплений КБ являются:
• многодетальность (21 деталь в каждом узле скреплений)
• материалоемкость (общая масса металлических и полимерных деталей на 1 км пути составляет соответственно 41,6 и 2,1 т)
• и наличие около 16 тыс. болтов на 1 км пути, содержание которых (очистка от грязи, смазка, подтягивание гаек) требует больших затрат.
www.vsp74.ru
Комплект скрепления КБ-65 высокого качества от компании ВСП74 в Челябинске
Типовым промежуточным скреплением для железобетонных шпал является раздельное клеммно-болтовое скрепление КБ, в котором рельс к подкладке прижимается жесткими клеммами, надеваемыми на клеммные болты, фигурные головки которых заводятся в пазы реборд подкладок. Под гайки клеммных болтов ставят упругие шайбы. Под рельс, на металлическую подкладку укладывают резиновую прокладку, для улучшения упругих свойств скрепления. Металлические подкладки укладывают на наклонную (для обеспечения подуклонки рельсов), заглубленную в тело шпалы на 15— 25 мм подрельсовую площадку. На бетон под подкладку укладывают для электро- и виброизоляции резиновую прокладку толщиной 6—8 мм. Благодаря этому осуществляется передача поперечных горизонтальных сил от подкладки через нашпальную прокладку на бетон, улучшаются условия работы закладных болтов и повышается стабильность ширины колеи.
Подкладка крепится к шпале закладными болтами. При этом головки болтов опираются на замоноличенную в бетон металлическую шайбу, которая при затяжке монтажных гаек равномерно распределяет нагрузку на бетон. Электроизоляция подкладок от шпал осуществляется нашпальной прокладкой и втулкой из текстолита, надеваемой на стержень закладного болта и заглубляемой в отверстие металлической подкладки.
Высота реборд подкладок КБ позволяет укладывать под рельс прокладки толщиной 12—14 мм для ре- гулировки рельсов по высоте, что особенно важно в зимний период. В других случаях это преимущество скреплений КБ используют для укладки под подошву рельса прокладок повышенной упругости.
Полностью себя оправдало применение скреплений КБ на бесстыковом пути в отношении применения прогрессивной технологии замены рельсов, разрядки температурных напряжений, обеспечения оптимальных условий температурной работы рельсовых плетей.
Недостатками конструкции скреплений КБ являются:
• многодетальность (21 деталь в каждом узле скреплений)
• материалоемкость (общая масса металлических и полимерных деталей на 1 км пути составляет соответственно 41,6 и 2,1 т)
• и наличие около 16 тыс. болтов на 1 км пути, содержание которых (очистка от грязи, смазка, подтягивание гаек) требует больших затрат.
www.vsp74.ru
Раздельное промежуточное рельсовое скрепление для железобетонных и деревянных шпал
Самым распространенным скреплением для железобетонных шпал с рельсами типов Р75, Р65 и Р50 является подкладочное раздельное скрепление (черт. 77 — 94, табл. 20, 21). На деревянных шпалах находит применение раздельное скрепление, в котором подкладка крепится к шпале с помощью шурупов (черт. 95 — 99, табл. 22).
Таблица 20. Детали, входящие в комплект узла раздельного промежуточного скрепления КБ65 на железобетонных шпалах с рельсами типа Р65 или Р75
Деталь | № позиции на черт. 77 | № черт в альбоме | Число деталей в узле | Масса одной детали, кг |
Подкладка КБ65 | 2 | 78 | 1 | 7,0 |
Болт М22×175 | 7 | 79 | 2 | 0,635 |
Болт М22×75 | 4 | 80 | 2 | 0,345 |
Гайка М22 | 3 | 81 | 4 | 0,126 |
Шайба двухвитковая 25 | 5 | 82 | 4 | 0,12 |
Прокладка под подошву рельсов Р65: — ЦП- 358 рифление в виде отверстий, — ЦП-318 без рифления, — ЦП-143 рифление в виде пазов) | 10 | 83 | 1 | 0,23 |
Скоба для изолирующей втулки КБ (ЦП-138) | 8 | 85 | 2 | 0,09 |
Шайба черная 22 (вариант) | 84 | 2 | 0,055 | |
Втулка изолирующая КБ (ЦП-142 или ОП-142) | 9 | 87 | 2 | 0,04 |
Втулка солирующая KB-1-22 (вариант) | 86 | 2 | 0,027 | |
Прокладка под подкладку КБ (ЦП-153) | 1 | 88 | 1 | 0,60 |
Прокладка под подкладку КБ (вариант) (ЦП-328) | 89 | 1 | 0,64 | |
Клемма ПК | 6 | 90 | 2 | 0,62 |
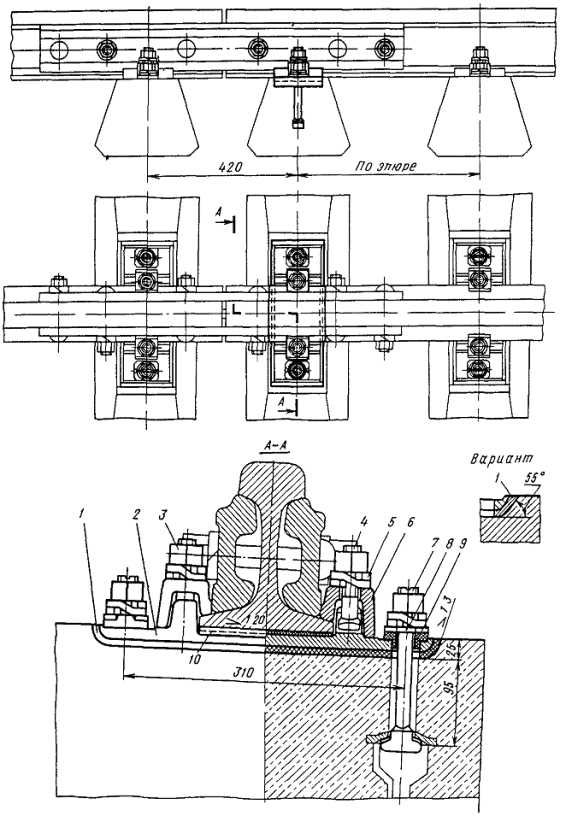
Черт. 77. Рельсовое скрепление КБ65 на железобетонных шпалах с рельсами типов Р65 и Р75
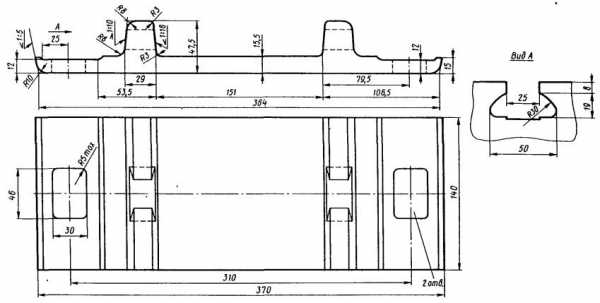
Черт. 78. Подкладка раздельного скрепления КБ65 по ГОСТ 16279-78
Черт. 79. Болт закладной М22×175 по ГОСТ 16017-79
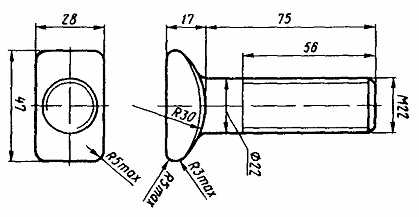
Черт. 80. Болт клеммный М22×75 по ГОСТ 16016-79
Черт. 81. Гайка М22 по ГОСТ 16018-79
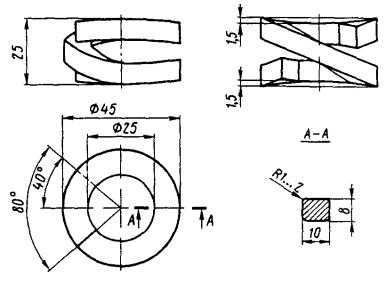
Черт. 82. Шайба двухвитковая 25 по ГОСТ 21797-76
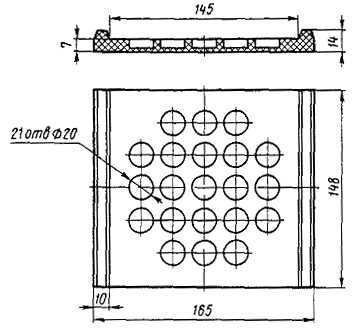
Черт. 83. Прокладка под подошву рельсов Р65
ЦП- 358 рифление в виде отверстий, ЦП-318 без рифления, ЦП-143 рифление в виде пазов
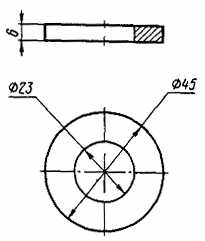
Черт. 84. Шайба черная 22
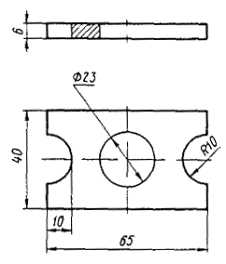
Черт. 85. Скоба для изолирующей втулки КБ (ЦП-138)
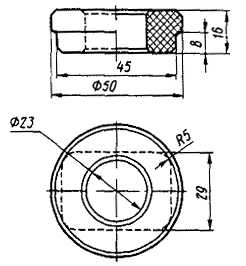
Черт. 86. Втулка изолирующая KB-1-22
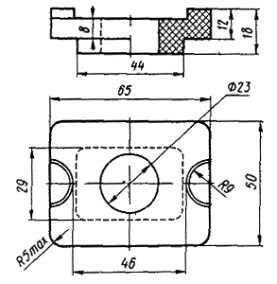
Черт. 87. Втулка изолирующая КБ (ЦП-142, ОП-142)
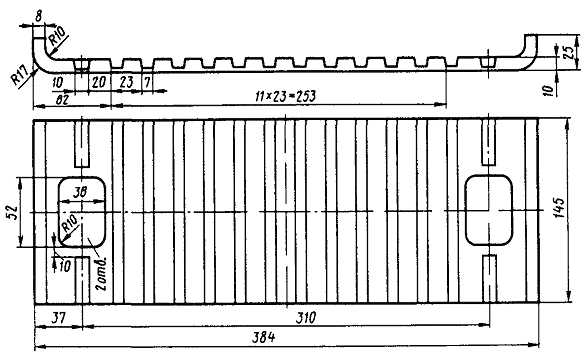
Черт. 88. Прокладка повышенной упругости под подкладку КБ (ЦП-153)
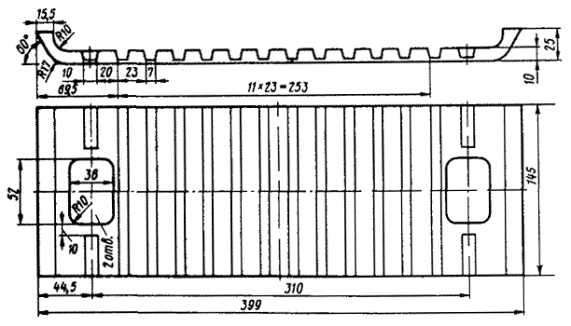
Черт. 89. Прокладка повышенной упругости под подкладку КБ (вариант) (ЦП-328)
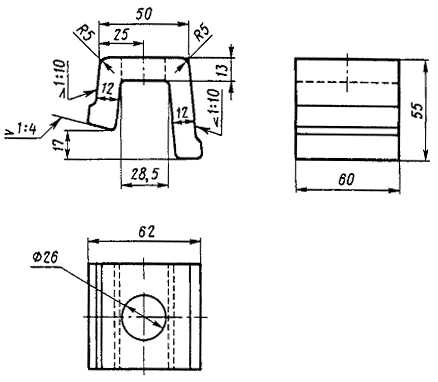
Черт. 90. Клемма раздельного скрепления (ПК) по ГОСТ 22343-90
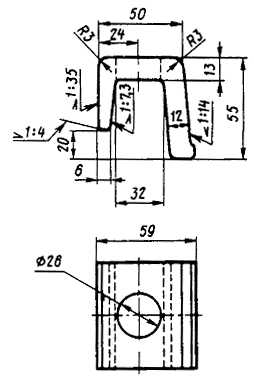
Черт. 91. Клемма раздельного рельсового скрепления (СК) по ГОСТ 22343-77
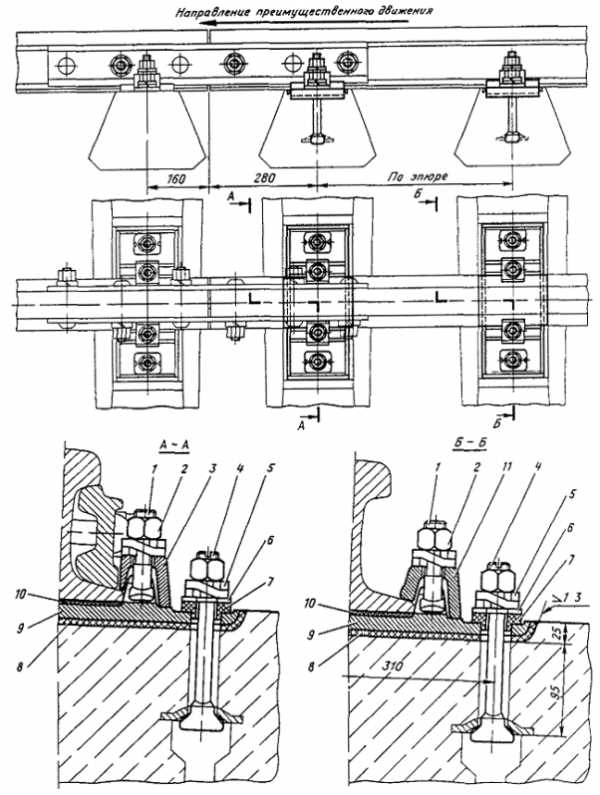
Черт. 92. Рельсовое скрепление КБ50 на железобетонных шпалах с рельсами типа Р50
Таблица 21. Детали, входящие в комплект узла раздельного промежуточного скрепления КБ50 на железобетонных шпалах с рельсами типа Р50
Деталь | № позиции на черт. 92 | № черт в альбоме | Число деталей в узле | Масса одной детали, кг |
Подкладка КБ50 | 9 | 93 | 1 | 6,95 |
Прокладка под подошву рельсов Р50 | 10 | 94 | 1 | 0,165 |
Болт М22×175 | 4 | 79 | 2 | 0,635 |
Болт М22×75 | 1 | 80 | 2 | 0,345 |
Гайка М22 | 2 | 81 | 4 | 0,126 |
Клемма ПК | 11 | 90 | 2 | 0,62 |
Клемма СК | 3 | 91 | 2 | 0,58 |
Шайба двухвитковая 25 | 5 | 82 | 4 | 0,12 |
Скоба для изолирующей втулки КБ (ЦП-138) | 6 | 85 | 2 | 0,09 |
Шайба черная 22 (вариант) | 84 | 2 | 0,055 | |
Втулка изолирующая КБ (ЦП-142 или ОП-142) | 7 | 87 | 2 | 0,04 |
Втулка изолирующая KB-1-22 (вариант) | 86 | 2 | 0,027 | |
Прокладка под подкладку КБ (ЦП-153) | 8 | 88 | 1 | 0,60 |
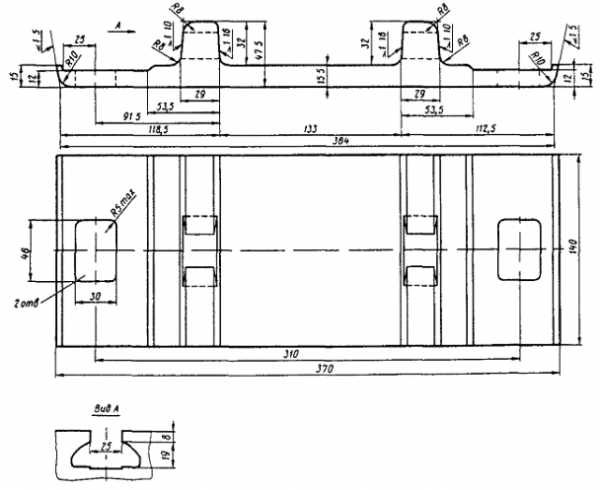
Черт. 93. Подкладка КБ50 по ГОСТ 16278-78
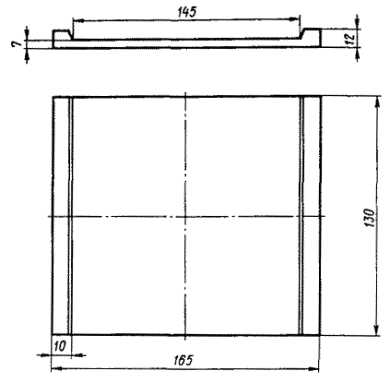
Черт. 94. Прокладка под подошву рельсов Р50
Таблица 22. Детали, входящие в комплект узла раздельного промежуточного скрепления КД65 (К4-65) на деревянных шпалах с рельсами типов Р65 и Р75
Деталь | № позиции на черт. 95 | № черт. в альбоме | Число деталей в узле | Масса одной детали, кг |
Подкладка К4-65 | 1 | 96 | 1 | 9,6 |
Прокладка под подкладку КД65 | 8 | 97 | 1 | 0,62 |
Шуруп путевой | 3 | 98 | 4 | 0,56 |
Прокладка под подошву рельсов Р65 | 7 | 99 | 1 | 0,25 |
Болт М22×75 | 6 | 80 | 2 | 0,345 |
Гайка М22 | 5 | 81 | 4 | 0,126 |
Клемма ПК | 4 | 90 | 2 | 0,62 |
Шайба двухвитковая 25 | 2 | 82 | 4 | 0,12 |
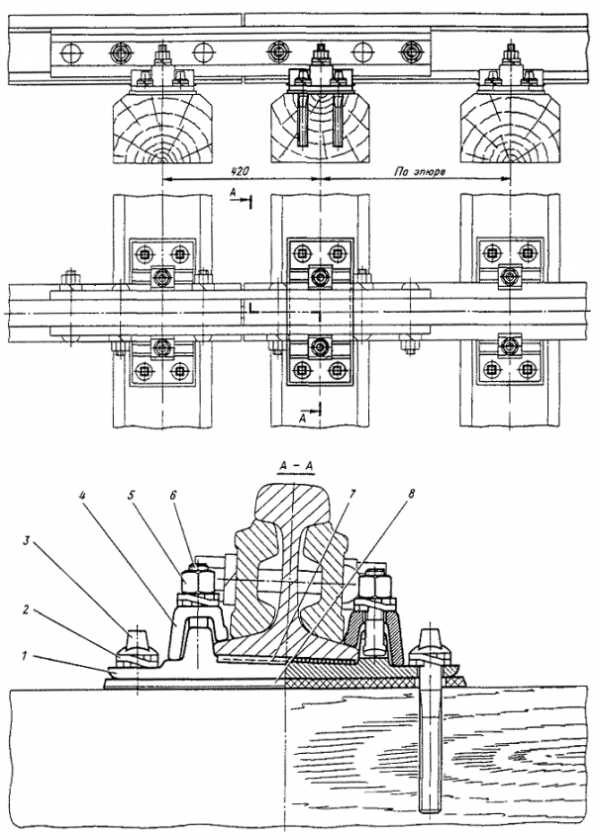
Черт. 95. Рельсовое скрепление КД65 (К4-65) на деревянных шпалах с рельсами типов Р65 и Р75
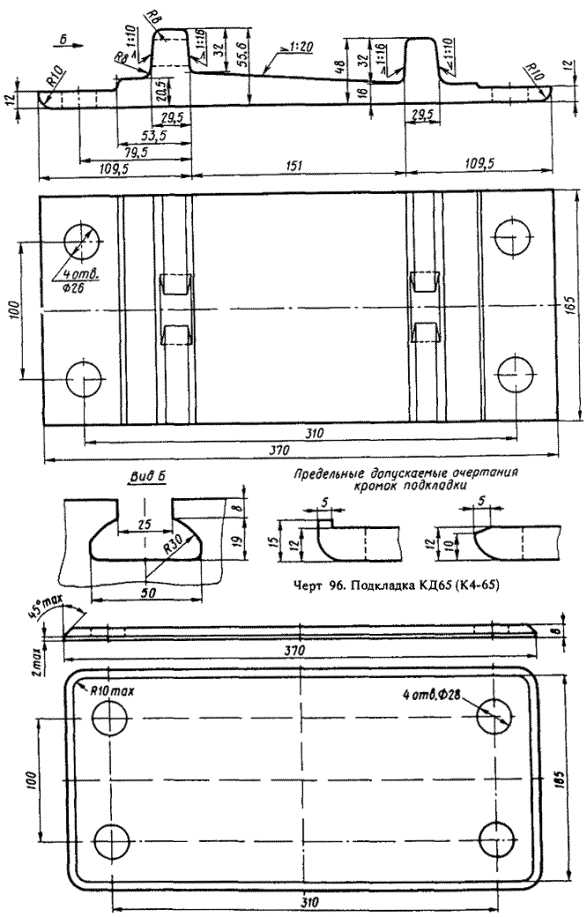
Черт. 97. Прокладка под подкладку КД65
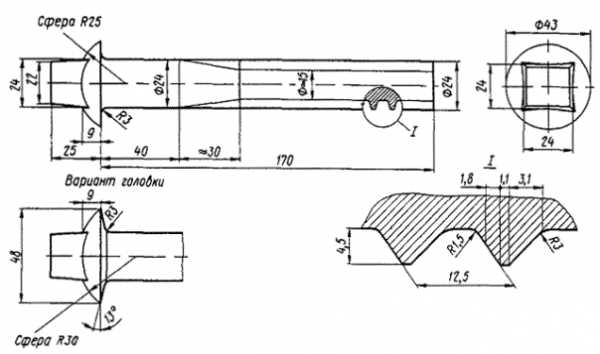
Черт. 98. Шуруп путевой 24×170 по ГОСТ 809-71
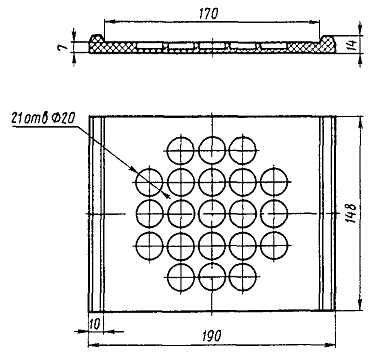
Черт. 99. Прокладка под подошву рельсов Р65 в скреплении КД65
Основные требования к подкладкам раздельного скрепления по ГОСТ 16277-84 (введен с 1 января 1986 г. взамен ГОСТ 16277-78)
1. Подкладки должны изготовляться из полос, прокатанных из стали спокойных, полуспокойных и кипящих марок, группы Б, первой категории (кроме стали марки БСтО по ГОСТ 380-88) с содержанием углерода от 0,18 % до 0,30 %, мышьяка до 0,20%.
Допускается изготовлять подкладки из полос с содержанием углерода стали не менее 0,16 % (при этом суммарное количество углерода и 1/4 марганца должно составлять не менее 0,28 %).
2. Поверхности прилегания подкладки к подошве рельса и шпале должны быть плоскими.
3. Допускаемые отклонения, мм, от правильной геометрической формы подкладок приведены ниже:
Продольная и поперечная выпуклость поверхности прилегания подкладок к подошве рельса | ≤0,5 |
То же, на расстоянии от торца до 20 мм | ≤1,5 |
Продольная и поперечная выпуклость и вогнутость прилегания подкладок к шпале | ≤1,5 |
Вогнутость поверхности прилегания подкладок к подошве рельса | Не допускается |
Отклонение от перпендикулярности торцов подкладок: в вертикальной плоскости в горизонтальной плоскости | ≤3,0 ≤5,0 |
4. Заусенцы, отпечатки на поверхности прилегания подкладок к подошве рельса и к шпале, а также на внутренних гранях реборд должны быть удалены посредством фрезерования, опиловки или вырубки, если они выходят за пределы опорных поверхностей.
Допускаются на наружной стороне реборд следы механической обработки глубиной не более 2 мм, получаемые при удалении заусенцев по периметру пазов для клеммных болтов.
Заварка или заделка дефектов не допускается.
5. На поверхности торцов подкладок, крепежных отверстий и пазов для клеммных болтов не должно быть расслоений.
Не допускаются заусенцы:
— по периметру пазов для клеммных болтов высотой более 1,5 мм;
— по периметру крепежных отверстий, выходящие за опорную верхнюю поверхность более 0,5 мм;
— на остальных поверхностях подкладок более 1,0 мм.
6. Отгиб концов реборд паза внутрь подкладок не должен быть более 1,5 мм и не должен выходить за пределы вертикальных линий, ограничивающих расстояние между внутренними гранями реборд у их основания.
7. При прошивке крепежных отверстий местное выпучивание металла на кромках подкладок ниже уса не должно быть более 1,0 мм и не должно выводить подкладку за установленные предельные отклонения по ширине более чем на 1 мм, при этом допускается деформация уса.
8. Подкладки испытывают на изгиб на угол 45° (внутренний угол 135°). Это испытание подкладка должна выдерживать без излома, трещин и надрывов.
9. По качеству подкладки разделяются на первый и второй сорт. Подкладки второго сорта используют на промышленных путях. Один торец подкладок второго сорта окрашивается красной краской.
10. На каждой подкладочной полосе, на наружной стороне одной из полок подкладок, должен быть выкатан выпуклыми буквами или цифрами товарный знак или условное обозначение предприятия-изготовителя с таким расчетом, чтобы этот знак имелся полностью или частично на каждой готовой подкладке.
11. На две подкладки каждой принятой партии навешивают металлический ярлык, в котором должно быть указано:
— товарный знак или условное обозначение предприятия-изготовителя;
— год и месяц изготовления подкладок;
— тип подкладок и сорт;
— номер партии;
— число подкладок в штуках;
— клеймо технического контроля предприятия-изготовителя;
— приемочное клеймо инспектора МПС.
Основные требования к клеммам раздельного скрепления по ГОСТ 22343-90 (введен с 1 июля 1991 г. взамен ГОСТ 22343-77)
1. Клеммы изготовляют из полос, прокатанных из стали марки Ст4 любой степени раскисления по ГОСТ 380-88.
2. Поверхности прилегания клеммы к подошве рельса и подкладке должны быть ровными. Допускается равномерная продольная выпуклость поверхности прилегания клеммы к подошве рельса и подкладке размером не более 1 мм.
Вогнутость поверхности прилегания клеммы к подошве рельса и подкладке не допускается.
3. На поверхности торцов клеммы и отверстий не должно быть расслоений.
4. Поверхности торцов клеммы должны быть перпендикулярны к продольной оси. Допускается косина реза в горизонтальной и вертикальной плоскости клеммы не более 3,0 мм.
5. Допускаются на опорных поверхностях клеммы вмятины от ножа не более 3,0 мм и утяжка металла не более 3,0 мм с плавным переходом к основной поверхности на расстоянии не более 15 мм от торца.
6. Допускаются заусенцы на торцах клеммы, около отверстия для клеммных болтов и на наружных нерабочих поверхностях клеммы высотой не более 1,0 мм.
7. В местах разъема валков допускается ус не более 1,5 мм. С наружной стороны большой ножки клеммы допускается ус не более 1,0 мм.
8. На каждую партию клемм навешивают два металлических ярлыка, в которых должны быть указаны:
— товарный знак или условное обозначение предприятия-изготовителя;
— номер партии;
— масса партии;
— клеймо технического контроля предприятия-изготовителя и инспектора МПС.
Основные требования к болтам и гайкам для скреплений по ГОСТ 16016-79, ГОСТ 16017-79 и ГОСТ 16018-79 (введены с 1 января 1981 г. взамен ГОСТ 16016-70, ГОСТ 16017-70 и ГОСТ 16018-70)
1. Стандартами предусмотрено изготовление клеммых, закладных болтов и гаек к ним нормальной и грубой точности.
2. Клеммные и закладные болты должны изготовляться класса прочности 3.6 или 4.8 по ГОСТ 1759.4-87.
3. Резьба по ГОСТ 24705-81. Поле допуска 8g по ГОСТ 16093-81.
4. Смещение оси головки болтов относительно стержня не должно превышать 0,9 мм.
5. Болты должны быть укомплектованы гайками по ГОСТ 16018-79.
6. Гайки должны изготовляться класса прочности 5 или 6 по ГОСТ 1759.5-87.
7. Резьба по ГОСТ 24705-81. Поле допуска 7Н по ГОСТ 16093-81.
8. Смещение оси отверстия гайки относительно оси симметрии не должно превышать 0,9 мм.
9. Фаски на конце резьбы гаек — по ГОСТ 10549-80.
10. Гайки отгружаются в комплекте с болтами для рельсовых скреплений.
Допускается транспортировать гайки как отдельные изделия. В этом случае упаковка гаек и маркировка тары выполняются по ГОСТ 18160-72.
Основные требования к шайбам пружинным двухвитковым по ГОСТ 21797-76
(введен с 1 июля 1977 г.)
1. На чертежах указаны размеры шайб, прошедших термическую обработку и трехкратное обжатие.
2. Пружинные двухвитковые шайбы должны быть изготовлены из стали марки 65Г по ГОСТ 14959-79 сечением 8×10 мм.
3. Допускается изготовлять шайбы из стали марки 60С2А по ГОСТ 14959-79 или из стали других марок с механическими свойствами не ниже стали 65Г, а также с цинковым покрытием с хроматированием.
4. На поверхности шайб не должно быть плен, трещин, раковин, расслоений и закатов. Наличие окалины на поверхности шайб и скрученность (пропеллерность витков) браковочными признаками не являются.
5. На поверхности шайб допускаются следы от подающего, навивочного и спрессовывающего инструмента в виде вмятин и задиров глубиной не более 0,5 и шириной до 5 мм.
6. На поверхности обрезанных концов допускаются сколы металла глубиной не более 1,5 мм и заусенцы высотой не более 1,5 мм.
7. Наружный диаметр шайбы в сжатом состоянии не должен превышать 49,5 мм.
8. Термообработанные двухвитковые пружинные шайбы должны иметь твердость от 40 до 50 единиц по Роквеллу.
9. Шайбы могут иметь маркировку, состоящую из условного обозначения предприятия-изготовителя и года изготовления (две последние цифры).
10. Упаковка шайб и маркировка тары производятся по ГОСТ 18160-72. Допускается упаковывать шайбы в тару массой нетто до 2,5 т.
11. По согласованию с потребителем допускается шайбы не упаковывать и перевозить без упаковки любым транспортом, кроме железнодорожных платформ.
Основные требования к изолирующим втулкам из реактопластов для рельсовых скреплений по ТУ 32 ЦП 748-86 (введены с 1 июля 1986 г. взамен ТУ 6-05-1809-77)
1. Технические условия распространяются на втулки изолирующие рельсовых скреплений, предназначенные для электрической изоляции болтов в рельсовых скреплениях железнодорожного пути.
2. Втулки изготавливаются из прессматериалов-реактопластов. В качестве основных материалов используется ткань пропитанная, премикс, прессматериалы ГСП-32, ДСВ-2-Р-2М, АГ-4В и др.
3. Втулки по своим качественным показателям должны соответствовать требованиям, приведенным ниже:
Форма и размеры | В соответствии с чертежом на изделие |
Разрушающее усилие при сжатии, кН, не менее | 100 |
Электрическое сопротивление в сухом состоянии, Ом, не менее | 106 |
Водопоглощение за 24 ч, %, не менее | 1,2 |
Маслопоглощение в осевом масле за 24 ч, %, не более | 0,8 |
4. Маркировка втулок производится путем гравировки соответствующих гнезд в прессформе.
5. Втулки упаковываются в многослойные бумажные или битумированные мешки.
Допускаются по согласованию с потребителем другие виды упаковки. Любой вид упаковки должен исключать возможность повреждения втулок в процессе транспортирования. Масса одного упаковочного места не должна превышать 20 кг.
6. При маркировке транспортной тары указывают:
— наименование завода-изготовителя и его товарный знак;
— условное обозначение втулки;
— номера технических условий;
— количество деталей;
— дата изготовления;
— штамп ОТК.
7. Втулки транспортируют любым видом крытого транспорта в соответствии с правилами, действующими на данном виде транспорта.
8. Втулки должны храниться в складских помещениях или под навесами.
Основные требования к подрельсовым и нашпальным прокладкам-амортизаторам из отходов шинного производства по ТУ 38 104 325-90
(введены с 1 января 1991 г. взамен ТУ 38 104 325-85)
1. Технические условия распространяются на прокладки-амортизаторы подрельсовые и нашпальные, изготовленные из отходов шинного производства и представляющие собой резинокордные пластины.
2. Резиновые смеси, предназначенные для изготовления прокладок-амортизаторов, должны удовлетворять по физико-механическим показателям требованиям, приведенным ниже:
Условная прочность при растяжении, кгс/м2, не менее | 100 |
Относительное удлинение при разрыве, %, не менее | 300 |
Сопротивление раздиру, кгс/см, не менее | 40 |
Эластичность по откосу, %, не менее | 30 |
Истираемость, м3/ТДж, не более | 140 |
Температурный предел хрупкости, °С, не выше | минус 50 |
3. Прокладки-амортизаторы по физико-механическим показателям должны удовлетворять требованиям, приведенным ниже:
Твердость по Шору А, единиц ………………………………… 75
Набухание в осевом масле «Л», %, не более …………….. 10
Водопоглощение, %, не более …………………………………. 0,2
Набухание в воде, %, не более ………………………………… 0,8
4. Маркировка производится оттиском гравировки прессформы в соответствии с требованиями чертежа.
5. Прокладки-амортизаторы поставляются без упаковки, связанными в пачки массой не более 15 кг. Пачки перевязываются шпагатом или резинотканевыми полосками из отходов производства.
6. Транспортная маркировка должна быть нанесена на ярлыки, которые крепятся к торцевой или боковой поверхности кип прокладок-амортизаторов.
7. Хранят прокладки-амортизаторы в сухих и чистых закрытых помещениях. При этом прокладки должны быть защищены от попадания агрессивных жидкостей и прямых солнечных лучей и находиться на расстоянии не менее 1 м от нагревательных приборов.
Основные требования к резиновым нашпальным прокладкам для железобетонных шпал по ТУ 38 105 1215-86
(введены с 1 января 1987 г. взамен ТУ 38 105 1215-78)
1. Технические условия распространяются на прокладки резиновые и смеси резиновые товарные для их изготовления, предназначенные для электрической изоляции и амортизации пути на железобетонных шпалах.
2. Резина, применяемая для прокладок, должна удовлетворять по физико-механическим показателям требованиям, приведенным далее:
Условная прочность при растяжении, кгс/см2, не менее | 75 |
Относительное удлинение при разрыве, %, не менее | 200 |
Относительная остаточная деформация, %, не более | 20 |
Твердость по Шору А, единиц, не менее | 57 |
Истираемость, м3/ТДж, не более | 300 |
Температурный предел хрупкости, °С, не выше | минус 32 |
Удельное объемное сопротивление электрическому току, Ом×см, не менее | 109 |
3. Готовые прокладки по физико-механическим показателям должны удовлетворять требованиям, приведенным ниже:
Твердость по Шору А, единиц, не менее | 57 |
Удельное объемное сопротивление электрическому току, Ом×см, не менее | 109 |
4. Маркировка формовых прокладок производится на каждой прокладке путем гравировки гнезд прессформ в соответствии с чертежами.
5. Прокладки собираются в пачки не более 20 штук. Пачки перевязываются шпагатом или другим перевязочным материалом, обеспечивающим сохранность пачки при транспортировании. Допускаются другие виды упаковки.
6. Каждое упаковочное место должно иметь ярлык с указанием:
— товарного знака или наименования предприятия-изготовителя;
— условного обозначения прокладки;
— номера партии;
— количества прокладок;
— марки резины;
— штампа ОТК;
— даты изготовления.
7. Прокладки должны храниться на расстоянии не менее 1 м от отопительных приборов и защищены от действия прямых солнечных лучей при температуре от 0 до 35 °С. Разрешается хранить прокладки при температуре до минус 25 °С при условии отсутствия деформации и ударных нагрузок.
Основные требования к путевым шурупам по ГОСТ 809-71
(введен с 1 января 1972 г. взамен ГОСТ 809-41)
1. Шурупы изготовляют из стали марки Ст3 по ГОСТ 380-88. По соглашению между потребителем и предприятием-изготовителем шурупы могут изготавливаться из других марок стали с механическими свойствами не ниже, чем у марки Ст3.
2. Для районов с холодным климатом шурупы должны изготовляться в исполнении ХЛ по ГОСТ 15150-69 из спокойных марок стали.
3. Для особых условий эксплуатации шурупы могут изготавливаться с антикоррозионным покрытием.
4. На поверхности шурупов не допускаются:
— риски и раковины глубиной более 0,5 мм;
— притупление ребер квадратной части головки, выводящее размеры диагонали квадрата за предельное значение;
— изогнутость стержня более 0,5 мм;
— смещение оси головки относительно оси стержня более 1 мм;
— швы от разъема матриц высотой более 0,5 мм и ступеньки более 0,3 мм от смещения матриц;
— увеличение наружного диаметра резьбы более размера 26 мм на участке сбега резьбы;
— рванины и выкрашивания ниток резьбы, если они по глубине выходят за предельные отклонения наружного диаметра резьбы и если общая протяженность рванин и выкрашиваний по длине превышает половину витка.
5. На торце квадратной части головок шурупов маркируют товарный знак или условное обозначение предприятия-изготовителя и год изготовления (две последние цифры).
www.rails.ru
Рельсовое скрепление — Энциклопедия нашего транспорта
Рельсовое скрепление — конструкция, соединяющая рельсы между собой или прикрепляющая их к подрельсовому основанию.
Рельсовые скрепления подразделяются на стыковые, служащие для соединения рельсов между собой вдоль пути, и промежуточные — для прикрепления рельсов к опорам (шпалам, рамам, плитам и т. д.).
Стыковые скрепления выполняются в виде плоских накладок, соединяющих рельсы при помощи болтов. В начале XX века от ранее применявшихся четырёхдырных плоских накладок перешли к шестидырным фартучным накладкам, у которых подошва рельса перекрывается горизонтальной полкой, переходящей в вертикальный «фартук». В месте прикрепления рельсов к стыковым шпалам для размещения подкладок и костылей (против второго и пятого болтовых отверстий) в полке и фартуке сделаны вырезы. При увеличении нагрузок и скоростей в этом ослабленном сечении возникали косые изломы. С 1947 года на отечественных железных дорогах осуществлялся переход на двухголовые накладки с четырьмя болтовыми отверстиями (рис. 1) для рельсов Р75 и Р65 и шестью для рельсов Р50. Масса четырёхдырных накладок для рельсов Р50 — 18,77 кг, для рельсов Р65 и Р75 — 23,48 кг, а шестидырных для рельсов Р50 — 18,77 кг, для рельсов Р65 и Р75 — 29,5 кг. В уравнительных пролётах бесстыкового пути применяются накладки с шестью отверстиями. Отверстия в накладках сделаны поочерёдно овальной и круглой формы. Верхние и нижние головки накладок имеют скос, выполненный под тем же углом, как нижняя грань головки и верхняя грань подошвы рельса. Поэтому при затягивании стыковых болтов обеспечивается устойчивость рельсового стыка. Стыковые болты диаметром 27 мм для рельсов Р65 и Р75 и 24 мм для рельсов Р50 имеют круглую голову и овальный подголовок. Такой подголовок входит в овальное отверстие накладки, благодаря чему болт при завинчивании гайки не проворачивается. Разрезные шайбы, надеваемые на болт под гайку, обеспечивают упругое восприятие сил до 12 кН. Для изолирующих стыков на линиях, оборудованных автоматической блокировкой, применялись первоначально деревянные накладки, позже лигнофолиевые, а с 1950-х годов — металлические. Между металлической накладкой и рельсом помещается полиэтиленовая прокладка, на болты надеваются полиэтиленовые втулки. Торцы рельсов также разделены изолирующей прокладкой. В конструкции изолирующего стыка могут применяться и объемлющие накладки, охватывающие рельсы со стороны нижней плоскости подошвы. С 1969 года широко применяют клееболтовые электроизолирующие стыки, в которых двухголовые накладки уменьшены по высоте с обеих сторон на 3 мм. Образующийся между накладкой и рельсом люфт заполнятеся стеклотканью, пропитанной эпоксидным клеем с добавлением отвердителя. При использовании накладок с шестью болтовыми отверстиями и затяжкой болтов до 150—170 кН такой стык упруго воспринимает продольные силы до 1500 кН, а при применении объемлющих накладок — до 3000 кН.
Промежуточные скрепления могут быть раздельными (тип Д2 и Д4 для деревянных и тип КБ для железобетонных шпал), нераздельными (костыльные с подкладками, имеющими три костыльных отверстия, для деревянных шпал и тип ЖБ для железобетонных шпал) и смешанными (тип ДО — костыльные с подкладками, имеющими пять костыльных отверстий, для деревянных шпал).
Наиболее распространённой конструкцией промежуточного рельсового скрепления на пути с деревянными шпалами является костыльное скрепление (тип ДО). В этой конструкции (рис.2) применяются клинчатые двухребордчатые подкладки с пятью костыльными отверстиями: три для постановки костылей у подошвы рельса (из них два — с внутренней стороны) и два — для обшивочных костылей, для удобства расшивки которых на подкладке предусмотрены бортики. Для предохранения от прорезания древесины шпал подкладки имеют закруглённые по концам нижние грани и укладываются на прокладки из полимерных материалов (гамбелита или резины). Костыли имеют длину 165 мм, поперечное сечение 16×16 мм, овальную головку; пучинные костыли выпускаются длиной 205, 230, 255, 280 мм. Для более стабильного прижатия рельсов к подкладкам и шпалам могут применяться термически обработанные изогнутые костыли, обладающие пружинящими свойствами. В раздельных промежуточных скреплениях (тип Д2 и Д4) подкладка прикрепляется к шпале шурупами, а рельс к шпале клеммами и клеммными болтами (рис. 3). Скрепления этих типов имеют много деталей, большую металлоёмкость, но позволяют укладывать бесстыковой путь на деревянных шпалах и производить выправку пути установкой дополнительных подрельсовых прокладок между подошвой рельса и подкладкой.
Промежуточные рельсовые скрепления для пути на железобетонных шпалах применяются двух основных типов: подкладочные типа КБ с жёсткой клеммой (рис. 4) и бесподкладочные типа ЖБ с пружинной клеммой (рис. 5). В скреплении КБ подкладка, имеющая две реборды, крепится к шпале двумя закладными болтами, которые вставляются в шпальные отверстия и после поворота на 90° упираются плечиками
в закладную шайбу. Под гайкой и шайбой закладного болта устанавливают текстолитовую втулку, обеспечивающую электрическую изоляцию болта от подкладки. Под подкладку укладывается изоляционная резиновая рифлёная прокладка, позволяющая также снизить жёсткость конструкции. Обычно резиновая прокладка имеет толщину 7 мм, в шпале с углублением для подрельсовой площадки — 14 мм. В отверстия реборд в виде ласточкиного хвоста вставляют клеммные болты, закрепляющие клеммы. Опираясь одной лапкой в подкладку, а другой — в подошву рельса, клеммы фиксируют рельс на подкладке. Для уменьшения жёсткости и большей стабильности прижатия подошвы рельса к шпале под гайку клеммного болта укладывают двухвитковую шайбу, а под подошву рельса — прокладки. Положение рельса можно регулировать по высоте до 14 мм укладкой дополнительных прокладок из полиэтилена. Установка пружинной прутковой клеммы типа «Краб» позволяет дополнительно снизить жёсткость конструкции. Скрепление ЖБ имеет два закладных болта, которые прижимают пружинные клеммы к шпале и подошве рельса. У пластинчатой клеммы нижняя ветвь доходит до кромки подошвы, а верхняя прижимает подошву рельса к шпале. Изоляция закладного болта аналогична изоляции скрепления КБ. Рельс от шпалы изолируется постановкой резиновой прокладки, служащей одновременно амортизатором. Пружинящие свойства клеммы обеспечивают стабильное прижатие подошвы рельса к прокладке и шпале. Скрепление ЖБ не позволяет регулировать рельсы по высоте и имеет недостаточное сопротивление горизонтальным боковым силам в крутых кривых. Основные недостатки скреплений КБ — высокую жёсткость и многодетальность — позволяют устранить скрепления типа БП (рис. 6), в которых закладной болт выполняет функции и клеммного болта, а клеммы — пружинные, пластинчатые или прутковые. При этом сохраняется возможность регулировки положения рельса по высоте. Скрепление БП является универсальным, поскольку при заглублении подрельсовой площадки на 25 мм оно может использоваться и без подкладки, но с упругими прокладками и клеммами. Бесподкладочное скрепление типа ЖБР (рис. 7) отличается повышенной надёжностью по сравнению со скреплением типа ЖБ. Так же, как скрепление БП, имеет заглублённую подрельсовую площадку и пружинную клемму, в которой подошва рельса перекрывается её верхней и нижней ветвями.
Источник:
- «Энциклопедия железнодорожного транспорта», научное издательство «Большая Российская энциклопедия», 1995 год.
wiki.nashtransport.ru
4.3.1. Промежуточные скрепления для деревянных шпал
Промежуточные скрепления для деревянных шпал делятся на:
бесподкладочные – без металлических подкладок под рельсами;
подкладочные:
нераздельные,
смешанные,
полураздельные,
раздельные.
При нераздельных скрепленияхрельс через подкладку соединяется непосредственно с опорой. Нераздельные скрепления могут быть костыльными и шурупными. Костыльные скрепления являются самыми простыми, удобными при сборке и разборке и применяются в основном на звеньевом пути. Основной недостаток – плохая связь рельса с подкладкой и подкладки со шпалой.
При смешанных скрепленияхрельс через подкладку соединяется с опорой, и, кроме того, подкладка самостоятельно прикрепляется к опоре.
Полураздельные скрепления– с одной стороны рельса скрепление осуществлено, как нераздельное, а с другой – как раздельное.
Раздельные скрепления– рельс скреплен только с подкладкой, а подкладка независимо от рельса соединена с опорой.
В настоящее время в постоянной эксплуатации находятся в основном два типа скреплений – смешанное скрепление ДО (рис. 4.2) и раздельное скрепление КД (рис. 4.3, а). Применяется также скрепление Д4 (рис. 4.3, б).
Рис. 4.2. Смешанное скрепление ДО:
1 – рельс; 2 – костыль; 3 – подкладка; 4 — шпала
Подкладку к шпале принято пришивать двумя обшивочными костылями, а рельс к шпале на прямых участках пути – костылями, расположенными диагонально. На кривых при необходимости рельсы к шпалам пришивают дополнительно костылями. основными недостатками скрепления ДО являются: смятие древесины под подкладкой и разработка костыльных отверстий, возможность напресовки снега и засорителей под подошвой рельса, что является причиной уширения колеи и схода подвижного состава.
В раздельном скреплении КД металлическая подкладка крепится к шпале четырьмя шурупами, а рельс прижимается к подкладке двумя жесткими П-образными клеммами и клеммными болтами. Это скрепление в отличие от скрепления ДО обеспечивает постоянное прижате рельса к подкладке и позволяет производить регулировку рельса по высоте до 14 мм. При этом обеспечивается стабильность ширины колеи и облегчается смена рельсов. Основной недостаток скрепления КД – его многодетельность и большая материалоемкость.
Скрепления типа Д4сравнительно мало, они отличаются многодетальностью и металлоемкостью. Они сильнее, чем костыли, зажимают рельсы и таким образом препятствуют угону пути. Такие скрепления могут использоваться при укладке бесстыкового пути. Между рельсом и подкладкой укладываются прокладки разной толщины, что позволяет регулировать положение рельсов по высоте.
Рис. 4.3. Раздельное скрепление для деревянных шпал:
а – типа КД; типа – Д4; 1 – двухвинтовая шайба; 2 – шуруп;
3 – подкладка; 4 – клеммный болт; 5 – клемма; 6 – подрельсовая площадка; 7 – прокладка под подкладку
4.3.2. Промежуточные скрепления для железобетонных шпал
Скрепления для железобетонных шпалмогут быть:
подкладочными и бесподкладочными;
жесткими и упругими;
раздельными и нераздельными.
В главном пути РЖД эксплуатируются следующие промежуточные рельсовые скрепления:
КБ-65 (88,8%),
ЖБР-65 (7,9%),
АРС(2,86%),
ЖБР-65Ш (0,3%),
КН-65 (0,12%),
ЖБР-65П.
Наиболее распространенным промежуточным скреплением для железобетонных шпал является раздельное скрепление КБ с жесткими клеммами. Типовое раздельное клеммно-болтовое скрепление работает в главном пути более 50 лет. В таком скреплении рельс прижимается к подкладке двумя жесткими клеммами, а подкладка крепится к шпале двумя закладными болтами. Основными недостатками скрепления КБ является его многодетальность (21 деталь), материалоемкость (41,6 т металла и 2,1 т полимеров на 1 км пути) и большое количество болтов (16 тыс. болтов на 1 км). Степень натяжения болтов быстро ослабевает, что требует регулярной и частой проверки, смазки и подтяжки.
В пути с железобетонными шпалами проходят проверку нераздельные скрепления БП, которые могут быть подкладочными или бесподкладочными.
Бесподкладочные упругие нераздельные скрепления ЖБР с прутковой клеммой обладают большей, чем у КБ, стабильностью натяжения болтов. недостаток таких скреплений – высокая трудоемкость при сборке рельсошпальной решетки и недостаточная стабильность ширины колеи в кривых. Разновидностями таких скреплений являются скрепления ЖБР-65П и ЖБР-65Ш.
В модернизированном подкладочном скреплении ЖБР-65П вместо плоских клемм применены пружинные прутковые и металлическая подкладка. Бесподкладочное шурупно-дюбельное скрепление ЖБР-65Ш имеет два шурупа, которые ввинчиваются в дюбели, заделанные в шпалу, и прижимают клеммы к подошве рельса.
Нераздельное клеммно-болтовое скрепление БП имеет два закладных болта, которыми при помощи упругих клемм рельс прижимается к подкладке, а подкладка – к шпале. Преимуществом данного скрепления перед скреплением КБ является возможность регулировки положения рельса по высоте до 20 мм. Скрепление БП может быть подкладочным или бесподкладочным.
В Московском государственном университете путей сообщения (МИИТ) разработано безболтовое анкерное рельсовое скрепление АРС, которое может работать на магистральных линиях при любых скоростях движения и грузонапряженности. Его положительные качества — высокая надежность и обеспечение стабильности ширины колеи и небольшая материалоемкость (экономия металла не менее 15 т на 1 км), простота сборки. Скрепление является нераздельным, основной элемент скрепления – замоноличенный в бетонную шпалу анкер рамноарочного типа. Скрепление модификаций АРС-4 (рис. 4.4) позволяет регулировать положение рельса по высоте до 20-24 мм.
Основным недостатком скреплений ЖБР и АРС является недостаточная обеспеченность стабильной ширины колеи в кривых участках пути, особенно в крутых кривых. Причиной этого является плохое качество полимерных элементов скреплений.
Рис. 4.4. Нераздельное упругое анкерное скрепление АРС-4:
1 – упругая клемма; 2, 3 – монорегулятор-фиксатор; 4 – подклеммник; 5 – анкер; 6 – изолирующий уголок; 7 – резиновая прокладка.
Сроки службы скреплений в настоящее время не позволяют повысить надежность работы пути. Назначенный ресурс скреплений должен составлять не менее 1 млрд. т брутто. Для повышения надежности скреплений допускается периодическая замена подрельсовых прокладок при смене рельсов.
studfiles.net
Рельсовое скрепление типа КБ — ООО «Строй Универсал»
Детали, входящие в комплект узла раздельного промежуточного скрепления КБ-65 |
|||
Деталь |
№ позиции на чертеже |
Число деталей в узле |
Масса одной детали, кг |
Подкладка КБ65 |
2 |
1 |
6,85 |
Болт закладной М22х175 |
7 |
2 |
0,635 |
Болт клеммный М22х75 |
4 |
2 |
0,345 |
Гайка М22 |
3 |
4 |
0,126 |
Шайба двухвитковая диаметр 25 |
5 |
4 |
0,12 |
Прокладка под подошву рельсов Р65 (типа ЦП-143) |
10 |
1 |
0,23 |
Скоба для изолирующей втулки КБ (шайба плоская) |
8 |
2 |
0,09 |
Втулка изолирующая КБ (ЦП-142) |
9 |
2 |
0,04 |
Прокладка под подкладку КБ-65 (ЦБ-328) |
1 |
1 |
0,60 |
Клемма ПК-65 |
6 |
2 |
0,62 |
Вернуться в раздел Наша продукция
stroiuniversal.ru