Как делают металл для VW, Renault, Hyundai, Kia… — репортаж с завода — журнал За рулем
Из череповецкой стали штампуют почти всё, что выпускают на российских автозаводах. «За рулем» отправился в Череповец, чтобы разобраться, как производят прокат для автопрома и какая толщина у металла, из которого изготовлен кузов вашего автомобиля.
Материалы по теме
Череповецкий металлургический комбинат рождает смешанные чувства.
Смотрю на грандиозные доменные печи и проезжающие составы с расплавленным металлом — и в голове звучит мелодия «Время, вперёд!» из девятичасовых новостей. А реки раскаленной руды заставляют вспомнить кузни гномов из эпического произведения Толкиена.
Здесь творится магия рождения металла, из которого делают автомобильный лист. Из «северстали» штампуют почти всё, что производится в России, - кабины и кузовá автомобилей ГАЗ, КАМАЗ, Haval, Renault, Nissan, Peugeot, Citroen, Volkswagen, Hyundai и Kia.
Не важно, у вас ГАЗель или Solaris.Толщина металла и оцинковка у них одинаковые!
Стройка вопреки
Череповецкий комбинат появился скорее «вопреки», нежели «благодаря». Но и благодарить есть кого — ученого-металлурга Ивана Павловича Бардина. Именно он предложил не строить комбинат рядом с месторождением руды или угля, который был основным топливом.
Материалы по теме
По мнению Бардина, Череповецкий завод следовало строить на равном удалении как от обоих месторождений, так и от двух столиц, на перекрестке водных артерий и железнодорожных путей.
Было много возражений, но стройка началась — по распоряжению Сталина, с которым, ясное дело, никто спорить не решался. Проект стартовал ударными темпами: НКВД пригнал около десяти тысяч заключенных. Но помешала война. Стройка возобновилась только в 1947 году, и через восемь лет комбинат дал первую партию чугуна. Причем очень высокого качества. Спустя три года отлили первую сталь. А уже в 1962 году комбинат стал рентабельным — Бардин оказался прав.
Сейчас Череповецкий металлургический выдает по 12 миллионов тонн стали ежегодно. Большая часть этого объема приходится на конструкционную сталь для судостроения и строительной отрасли. Автомобильный лист составляет лишь 10% объема. Однако именно это производство самое технологичное, требовательное и затратное.
Брак не прокатит
Всё начинается с доменных печей, коих в Череповце четыре (скоро закончится строительство пятой). Особая гордость — печь «Северянка» высотой больше 100 метров. Гигантская домна была задута (именно так называется запуск доменной печи) в 1986 году и долгое время оставалась самой большой в мире, попав в Книгу рекордов Гиннесса.
Материалы по теме
Позже в Японии, Корее и Китае появились домны больше, но в Европе «Северянка» по-прежнему королева. Аппетит под стать размеру — каждый день она сжирает по шесть железнодорожных составов кокса и почти 70 тысяч кубометров газа, отдавая взамен по 13–15 тысяч тонн чугуна — исключительно передельного (так называют чугун для последующей переплавки в сталь).
Расплавленный чугун отправляется в сталеплавильный цех, который тоже поражает воображение. Над головой проезжают гигантские чаны; из них расплавленный металл переливают в формы и смешивают с металлоломом и присадками. Состав этого «винегрета» определяет физические и химические свойства стали, необходимые заказчику. При нас готовили сталь для ГАЗа. Точный состав, который требует каждый производитель, держат в секрете. Но всем производителям отправляют высокопрочную сталь, предел прочности которой 1500–2000 мПа. На выходе получают большие раскаленные отливки, так называемый сляб.
Расплавленный чугун отправляют в переплавку, замешивая с металлоломом и присадками. На выходе получают раскаленные отливки из стали.
Отливки проходят пластическую обработку, затем их охлаждают и закручивают в рулоны.
После того как газовые резаки настругают одинаковые плиты сляба, в дело вступает стан горячей прокатки «2000». Число означает вовсе не год открытия, а ширину валков, через которые черновой сляб проходит, утончаясь до толщины автомобильного листа. Раскаленные плиты больше километра едут по конвейеру, периодически попадая в тесные объятия валков. Каждый такой проход сопровождается брызгами искр и тяжелым дыханием испаряющейся воды, необходимой для охлаждения.
Материалы по теме
На выходе прокат закручивается в километровые рулоны. Их-то и отправляют на финальную обработку — в новенький цех оцинковки. Здесь чисто и светло, ничего общего с брутальным производством черного металла. Череповецкая сталь не зря устраивает всех зарубежных производителей, пришедших к нам на рынок.
Рулоны нарезают в листы, они проходят оцинковку, после чего их снова сваривают между собой и закручивают в рулоны уже окончательно и бесповоротно — для отправки заказчику. Причем швы увидеть просто нереально — на выходе получается цельный километровый лист. Размер рулонов определяется заказчиком — вес варьируется от 5 до 30 тонн. Но перед этим весь лист проходит контроль, причем очень жесткий. Даже малейший брак недопустим. Всматриваясь в дефектные листы, я иногда не мог найти хоть какой-то изъян. Кстати, совсем недавно на заводе освоили производство и стали DР600, предназначенной для изготовления колесных дисков.
Готовую сталь перед отправкой заказчику снова закручивают в рулоны.
Культура производства
Атмосфера и масштабы предприятия вселяют гордость: не все промышленные гиганты Союза отправились в небытие. Завод работает и кормит не только владельцев, но и город: благодаря Северстали Череповец живет и развивается.
И о людях думают. Вот простая мелочь: во всех цехах, у каждой лестницы — плакаты с просьбой держаться за поручни. Казалось бы, никто их не читает, но травматизм снизился на 80%! Именно из этого складывается культура производства, а без нее качества не достичь.
- Как сэкономить на кузовном ремонте, читайте тут.
Из череповецкой стали штампуют почти всё, что выпускают на российских автозаводах. «За рулем» отправился в Череповец, чтобы разобраться, как производят прокат для автопрома и какая толщина у металла, из которого изготовлен кузов вашего автомобиля.
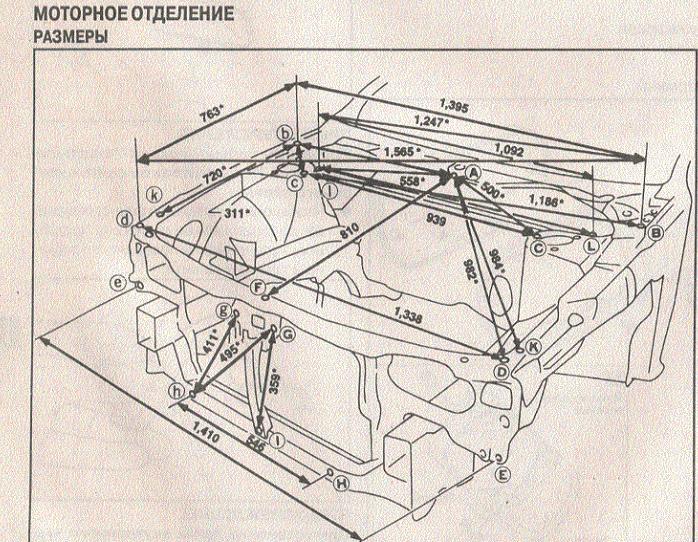
Металл для ремонта кузова автомобиля
Металл из которого производят автомобили имеет свойство ржаветь. Эта проблема вполне решаема. Нужно лишь вырезать сгнившую деталь или её часть и поставить “заплатку”.
Какой металл подойдет для ремонта?
Для ремонта корпуса важно использовать те стали, которые были рассчитаны и заложены на заводе. Кузов автомобиля является несущим элементом, и проектируется таким образом, чтобы:
- Выдерживать все нагрузки при эксплуатации автомобиля;
- При аварии деформироваться таким способом, чтобы не подвергать пассажиров и водителя угрозе. К примеру, чтобы капот не сдвигался в кабину, а сминался, постепенно снижая силу удара при лобовом столкновении.
Лучше покупать готовые кузовные элементы, или вырезать детали из аналогичных списанных автомобилей. “За” использование кузовного железа говорит тот факт, что металл уже имеет защитное покрытие. И часто оно отличается высоким качеством, ведь нанесено на заводе. Но готовые элементы дороги, а автомобильный кузов модели, аналогичной вашей, редко доступен для раскраивания под сварку. Что же делать?
Листовой металл для ремонта машины
Экономичным материалом для ремонта кузова служит листовой прокат, который можно найти на металлобазе или в строительном магазине. Для ремонта применяют следующие марки стали: 08ПС, 08КП, 10ПС, 08Ю, 01ЮПД, 08ГСЮФ, 08ГСЮТ, 08ЮП, 08ЮПР, 08ФКП, 09Г2С. Среди перечисленных марок наиболее часто встречается листовая сталь 09Г2С.
В различных моделях автомобилей определить конкретную марку стали не так просто. Но существуют общие советы:
- Используемый прокат должен быть холоднокатаным. Такой прокат более однороден по структуре, имеет более высокие параметры прочности, пластичности и упругости, на нем отсутствует окалина.
- Металл должен быть мягким, для придания ему нужной формы.
Толщину используемых для ремонта элементов необходимо выбирать близкую к заводским, чтобы в результате ремонта конструкция работала таким же образом, как запланировано при конструировании. Для неответственных элементов кузова и днища (таких, как листовые панели, двери, капот и т.д.) можно брать листовой металл 09Г2С, толщиной 0,8 – 1 мм. Если необходимо восстановить ответственные несущие элементы кузова (усилители днища, передние стойки кузова, и т.д.), толщину и марку металла лучше всего выбрать аналогичную использованной на заводе. Чаще всего, подойдет лист из стали 09Г2С, с толщиной 1 – 1,5 миллиметра.
Не рекомендуется усиливать конструкцию кузова бездумно. Например, приваривать профильную трубу на место порогов, так как она увеличивает жесткость кузова в месте присоединения. Это может привести к повышенной нагрузке на сварные швы и могут возникнуть деформации (трещины) в швах или околошовных зонах. Такое изменение повлияет и на работу конструкции кузова в целом: изменится поведение кузова при аварии, что абсолютно нежелательно.
Вырезать заплатку лучше ножницами по металлу, для получения ровного края реза. Края свариваемых элементов необходимо зачищать углошлифовальной машинкой, для получения качественного шва.
При восстановлении неответственных элементов для получения сложной формы детали допускается воспользоваться газовой горелкой. Нагревая элемент, мы повышаем его гибкость. Но при восстановлении ответственных элементов этот инструмент лучше не использовать, ведь нагрев меняет параметры стали.
Сравниваю толщину металла современных авто и тех, что выпускали в СССР. Немного удивился | АВТОБЛОГЕР
Приветствую вас, товарищи автолюбители!
Недавно мне в голову пришла идея сравнить толщину металла современных автомобилей, а также тех, что выпускали в СССР. Мысль такая возникла после того, как я увидел в сети видео, где металл современной иномарки прогибается под усилием пары пальцев простого, среднестатистического человека.
В то же время я прекрасно помнил моменты, когда металл автомобилей из СССР не особо то и хотел гнуться даже от удара ногой, хотя, честно говоря, с этими автомобилями наши люди делали такую процедуру довольно часто.
Я стал изучать эту информацию, искал только подтверждённую реальными замерами и отчётами, дабы не вводить себя и вас, товарищи, в заблуждение.
По-итогу мне удалось выискать вот такие данные:
1) Толщина металла с завода на автомобиле ВАЗ-2101 была от 0,7 мм до 1 мм. Тонкими были задние крылья, крышка багажника и капот. Более толстыми были брызговики, дно и пороги. Но это утолщение не особо то и помогло этим частям данного авто, ржавели и гнили до дыр очень сильно и быстро.
2) Толщина металла на LADA Granta, Vesta, да и в целом всех современных автомобилей, которые производит «АвтоВАЗ», была чуть меньшей, чем на «Копейке» — от 0,6 мм до 0,8 мм.
Это меня немного удивило, ведь я видел тесты этих авто на пассивную безопасность: если «Копейка» и её рестайлинговая версия в виде ВАЗ-2107 при ударе о бетонный барьер сминались буквально в хлам, представляя из себя, как говорят в народе, «консервную банку», то Веста держала удар очень хорошо, там и водитель с пассажиром даже не пострадали, так, встряхнулись чуть-чуть.
Вот что значит современных технологии, когда с использованием меньшего количества ресурсов получается более прочный кузов.
Друзья, если у вас есть желание, то можете прочитать другие мои статьи:
Почему я всегда советую отгибать уплотнители на дверях автомобиля при его покупке
Простой способ, как легко выкрутить ржавый саморез из подкрылка автомобиля
Друзья, если вам понравилась статья — подпишитесь на этот канал и поставьте лайк этому материалу, а при желании можете поделиться ей в социальных сетях, я очень старался при её написании и это будет лучшая поддержка от вас.
Впереди ещё много полезного и интересного про автомобили!
Если у вас есть что дополнить, или остались вопросы — пишите в комментарии. Удачи на дорогах и вне них.
Доказано, что современные автомобили с тонким металлом на самом деле лучше старых
Почему современные автомобили стали делать из тонкого металла.
Вы помните первую модель Лада ВАЗ-2101 , которая была сделана на базе 124-го Фиата ? Или старые 21-е Волги? Или возьмем более поздние модели ГАЗ-24. В том числе вспомните старые американские автомобили 70-х, 80-х годов. Все эти автомобили объединяет одно: у всех них кузов был сделан из толстого металла. Современные же автомобили заметно «похудели», приобретя кузова с тонкой (порой почти как фольга) толщиной металла. Куда же движется мировая автопромышленность?
Неужели к бумажным транспортным средствам? И как толщина кузова современных автомобилей может быть безопасной? Как тогда современные автомобили успешно проходят краш-тесты , получая высшие оценки? Оказывается, действительно все современные авто намного безопаснее своих тяжелых предшественников, большинство из которых были сделаны реально из толстого металла . Но как такое возможно?
Вот вам пример типичной аварии старого и современного автомобиля.
Обратите внимание на характер повреждений современного автомобиля и старого. Невооруженным взглядом видно, что даже при таком сильном ударе в боковую часть старой машине хоть бы хны, тогда как современный автомобиль получил довольно-таки серьезные повреждения.
Смотрите также
Оказывается, именно характер повреждений в подобных авариях и смущает автолюбителей, что и становится распространением мифа о небезопасности современных авто. Ведь действительно на первый взгляд кажется, что хорошо выдержавший удар старый американский автомобиль надежней современного. Но не все так просто. Так что – современные автомобили действительно хуже старых, и тонкие кузова новых автомобилей – это явный признак краха капитализма? На самом деле нет.
Знаете ли вы, что прогресс не стоит на месте не только в мире электроники и гаджетов. Он также постоянно продолжается и в автопромышленности. В том числе в области безопасности, которая за последние 20-30 лет существенно возросла. Да-да, современные авто намного безопаснее старых.
И дело здесь не только в большом количестве подушек безопасности и различных электронных системах помощи водителю. В первую очередь безопасность стала лучше за счет улучшений в конструкции кузова автомобилей . И этот прогресс продолжается. Все автомобильные компании вкладывают большие инвестиции в исследование и разработку новых технологий в конструкции кузовов.
Например, вот видео, где вы можете посмотреть краш-тест с участием двух автомобилей: современного и старого.
Имейте в виду, что у старого автомобиля толщина металла кузова в разы больше, чем у современной машины. Но по результату краш-теста старый автомобиль получил ужасные оценки безопасности, тогда как современное авто показало приемлемые результаты.
Или вот еще один ролик, где специалист пресс-центра компании АвтоВаз в передаче «В самом деле» развеивает миф о небезопасности современных автомобилей Лада, убеждая нас в том, что, несмотря на то, что современные Лады имеют кузова с тонким металлом, они намного безопасней своих старых предшественников, которые имели толстый метал в конструкции кузова.
По словам представителя АвтоВаза, тонкий металл в современной промышленности используется не только для того, чтобы снизить вес автомобиля с целью сокращения расхода топлива, но и для того, чтобы улучшить безопасность пешеходов. Чем тоньше металл, тем больше деформация кузова, что меньше, естественно, травмирует пешехода, если его собьет автомобиль.
Смотрите также
А как насчет водителя и пассажиров? Разве сильная деформация кузовных элементов, сделанных из тонкого металла, в современных автомобилях не угрожает тем, кто находится внутри салона? Оказывается, нет.
Тут нужно вспомнить физику, из которой следует, что чем больше происходит деформация кузова, тем больше энергии, вызванной столкновением, рассеивается. В итоге лишь небольшая часть этой опасной энергии поступает в салон, где сидят водитель и пассажиры. В случае же со старыми машинами , которые намного меньше подвергались деформации кузова, практически вся энергия удара при ДТП попадала в салон, принося тем, кто там сидел, тяжелые травмы.
Именно поэтому, несмотря на толстый металл кузовов старых машин, их безопасность, по современным меркам, оценивается, как правило, в ноль баллов или в ноль звезд.
Все современные автомобили, в том числе и отечественные Лады, имеют особую конструкцию кузова. Так, под тонкими кузовными деталями кузова, как правило, спрятан прочный каркас из различных крепких сплавов. Именно этот каркас и защищает водителя и пассажира при аварии. Кстати, в любой современной машине конструкторы еще во время проектирования транспортного средства создают зоны с так называемой запланированной деформацией. Это такие кузовные элементы, которые должны максимально деформироваться при ударе, чтобы максимально погасить энергию, возникшую во время ДТП.
Смотрите также
Да, облегчение кузова автомобиля за счет применения более тонкого металла имеет, конечно, и минусы. Куда без них. Ведь в мире нет ничего идеального. В том числе в мире автомобилей. За тонкий металл кузова автовладельцы расплачиваются, как правило, рублем. Во-первых, чем меньше толщина металла кузова, тем тоньше лакокрасочное покрытие автомобиля, что приводит к быстрому образованию сколов и другим повреждением кузова. Во-вторых, из-за того, что многие современные авто стали как фольга, приходится расплачиваться своим кошельком даже при небольшом ударе.
Так, даже при мелкой аварии современный автомобиль может быть существенно поврежден из-за сильной деформации того или иного кузовного компонента. Естественно, это расстраивает многих автовладельцев. Особенно тех, кто раньше владел старыми автомобилями, которые даже при сильном ударе внешне могли выглядеть после ДТП практически не поврежденными.
Именно это и заставляет многих автовладельцев ругать современные авто за их хлипкость, ненадежность и т. п., с добром вспоминая старые неубиваемые автомобили. Но, как видите, современные стандарты безопасности диктуют свои правила при проектировании и производстве автомобилей. Так как любое транспортное средство – это повышенный источник опасности для человека, то вопросы безопасности, конечно же, превыше всего и важнее искореженной кузовной детали.
Да, может быть, в чем-то современные автомобили стали хуже (качество, надежность, ремонтопригодность, стоимость обслуживания и т. д.), но что касаемо безопасности , то тут однозначно современные авто заметно выигрывают у старых машин.
Толщина кузовов ретро – машин не делает их безопасными при ДТП: mexanizm — LiveJournal
Раньше на машины металла не жалели, а сейчас что, пластмасса одна, — сетуют порой дедушки, поглядывая на новинки автомобильного мира, действительно больше напоминающие гаджет на колёсах, чем утилитарное средство передвижения.
Однажды, когда я шел на осмотр одного раритета, который хотел купить себе /спойлер – так и не купил ту машину/, разговаривал с владельцем о состоянии кузова. Кузов был пусть и не в идеальном, но весьма приличном состоянии. Владелец, парень лет 25 –ти как-то между делом сказал – там металл толстый, она и удар грузовика выдержит, как бронированный. Владелец не сильно разбирался в автомобилях, и термин «пассивная безопасность» ему знаком не был, так что, пока шли, немного ввёл его в курс дела.
(с)IIHSТолщина металла на ретро автомобилях это конечно хороший фактор, благодаря которому не все старые машины превратились в ржавую труху, и часть их дошла до наших дней. Но увы, на пассивной безопасности это не особо сказывается в наши дни. Те машины были спроектированы с учётом регламентов, скоростей и трафика тех времен, и с современными они конкурировать могут лишь в одном параметре – уникальном, особенном для каждого автомобиля дизайне. А вот на энергопоглощение силы удара при ДТП силовые элементы их кузовов не рассчитаны.
Это сейчас большинство легковушек выглядят однотипными, а тогда у каждой машины, хоть самой бюджетной, хоть премиум-сегмента был свой неповторимый внешний вид. Но, несмотря на то, что современные машины сделаны из тонкой стали, алюминия, стекла и пластика, в случае столкновения с раритетом, последний пострадает гораздо сильнее, и сидящим в его салоне не позавидуешь.
Американский Страховой институт безопасности дорог (IIHS) пошел на то, на что никто из нас никогда бы не отважился. Его специалисты провели краш-тест в виде лобового столкновения прекраснейшего Chevrolet Bel Air 1959 года с современным Chevrolet Malibu 2009 года выпуска. Вес автомобилей приблизительно одинаков, олдтаймер весит на 90 кг больше современного «Шевроле», правда, снизить вес удалость только за счёт демонтажа двигателя. Результаты для старичка оказались не утешительны.
(с)IIHS
Отсутствие у Bel Air даже банальных ремней безопасности (в 50-х их установка не считалась обязательной) а также деформация большой поверхности кузова не оставили манекену, сидящему на водительском месте никаких шансов, в то время как на «пластмассовом» Malibu манекен просто уткнулся в подушку безопасности.
(с)IIHSДеформации подверглась по в основном передняя часть автомобиля, в то время как у седана — «дедушки» на кузове относительно целой оказалась только задняя часть.
(с)IIHSКак видим, в дизайне современный автомобиль, похожий на пластиковый бокс для зубных щёток, не может потягаться со старичком, но вот по безопасности… 50 лет прошло не даром, каким бы толстым не был металл на олдтаймерах, на безопасности это никак не сказывается.
Volkswagen Jetta против Toyota Corolla
Объективно сравнивая двух конкурентов в B-классе Jetta и To*** Cor***, констатируем явное преимущество седана от Volkswagen.
Первая модель Toyota Cor**** появилась в 1966 году и за это время автомобиль ни разу не менял своего названия. В 2013 году вышла 11-я по счету генерация Toyota Cor****. Сборка автомобиля производится в Турции.
Поколение автомобиля, продающееся сегодня, оснащается 3-мя атмосферными бензиновыми двигателями и типами КПП:
- 1,33 VVT-i (99л.с.) возможно с 6МКП;
- 1.6 VVT-i (122л.с.) возможно с 6МКП; Вариатор;
- 1,8 VVT-i (140л.с.) возможно с Вариатор.
Величина клиренса
Производитель заявляет, что дорожный просвет автомобиля составляет 150 мм. В рамках эксперимента, проведенного инженерами Volkswagen в г. Калуга, расстояние от земли до переднего бампера составило 150 мм и расстояние от земли до порога 140 мм. Клиренс же Jetta по факту составляет 160 мм!
Низкий показатель в 140 мм обоснован наличием массивного сварного шва на пороге автомобиля в районе стойки «А». Это именно то место, которое чаще всего страдает при проезде неровностей.
Конструкция кузова
Из-за современного «самолетного» дизайна автомобиль получил дутые кузовные детали, которые не несут в себе никакой функциональности. Например: открывая массивную крышку капота, вы сможете увидеть большое количество свободного места в моторном отсеке. По факту, конечно, это не на что не влияет. Посмотрите внимательнее на обилие дополнительных кранштейнов и переходников, которые крепят детали подкапотного пространства. Как итог, мы получаем усложнение конструкции там, где это не нужно. Также это относится и к деталям кузовных панелей.
Если обратить внимание на автомобиль в целом, то можно заметить, что все кузовные детали массивные, этим обуславливается их высокая стоимость.
Cor**** обладает длинными дверьми, что существенно облегчает посадку в автомобиль. Однако мало на какой парковке клиенту удастся воспользоваться всеми предоставляемыми масштабами открытия дверей. Чем больше длина двери, тем уже угол ее открытия в стесненном пространстве (парковка).
Обратите внимание на наличие б/бака с левой стороны автомобиля, это особенность всех японских автомобилей. Обусловлена эта особенность дороговизной переноса данного элемента на другую сторону.
Толщина металла кузова автомобиля составляет от 0.3 мм. до 0.4 мм. и, как следствие, автомобиль имеет низкую жесткость внешних кузовных элементов.
Особенности:
- Низкая жесткость кузова на кручение, тонкий металл;
- Низкое качество отделочных материалов.
Комфорт
В таком большом автомобиле должно быть много места как спереди, так и сзади! И это действительно так — места предостаточно и там, и там. Однако есть моменты, на которые хотелось бы обратить внимание. Безусловно, широкая дверь облегчает посадку в автомобиль, если ее получится открыть на 100%.
Удачно производителям удалось реализовать стойку «С»: при посадке в автомобиль человек практически любого роста сможет разместиться с комфортом.
Подвеска и багажник
Перемещаясь к задней части автомобиля, стоит отметить тип задней подвески. Это торсионная балка вне зависимости от типа двигателя и комплектации.
Объем багажного отделения составляет 452 л, при этом организация багажного пространства на хорошем уровне и имеет геометрически правильные формы.
Стоит обратить особое внимание на трансформацию заднего сиденья — при сложенных спинках образуется большой порог и отсутствует лючек для провоза длинномеров.
Отделка салона
В момент, когда попадаешь в салон автомобиля, сразу же обращаешь внимание на излишнюю мягкость подушки сиденья и вертикально расположенную заднюю спинку второго ряда. Все это не позволяет проводить долгое время в автомобиле с комфортом.
Отделочные материалы, салона автомобиля и его кузова, не высокого качества. Например: это выражено в покрытой пленкой рамки двери, обивка сидений быстро теряет товарный вид, уплотнительные резинки не фиксируются и выпадают.
Попадая в салон автомобиля, сразу же ощущается диссонанс интерьера и экстерьера! Материалы, из которых выполнена панель, откровенно дешевы. Эргономика далека от совершенства и имеет множество спорных решений: подогревы сидений, спрятанные за декоративную шторку, архаичная зигзагообразная направляющая селектора переключения вариаторной коробки — все это настолько не интуитивно. Также из поколения в поколение автомобиль получает кнопки стеклоподъемников без подсветки и автоматического режима, что крайне не современно и не удобно. Обратите внимание: открытие лючка б/бака находится именно в том месте, куда попадает грязь с обуви при посадке в автомобиль.
Садясь в автомобиль, сразу же хочется настроить подлокотник под себя, так как его «мало», но такой возможности Cor**** нам не дарит.
Вывод
Итог таков: Cor***, выглядящая серьезно снаружи, не оправдывает ожидания внутри.
Минусы:
- Слабая эргономическая составляющая;
- Качество сборки автомобиля;
- Слабое опциональное оснащение.
Автоцентр Сити — Каширка Volkswagen
Москва, Внешняя сторона МКАД, 23 км
ежедневно: 08:00-21:00
Толщина кузова Киа Рио — Толщина металла кузова моделей ваз — Мой Kia Rio | Авто центр SPB
Да че вы пристали, не нравится?! Шок… Пауза… Проглотил.
Позвали инженера. При данной толщине ЛКП, если я через пол года приеду по вздувшейся краске например, что вы мне скажите?
Инженер И: Что это повторный окрас и не гарантийный случай… по глазам вижу, что понимает, что это треш Я: Дальше подписание доков и явно омраченное толщина металла у киа рио Эта мысль мне не даёт покоя до сих пор. У нее имеется собственное производство стали, а также Хендай закупает металл у других концернов.
По недостоверным данным стало известно, что одной из таких компаний стала Северсталь, но не должно быть никаких опасений по этому поводу, потому что на производстве строгий контроль за качеством материала.
Мой Kia Rio
Есть ли оцинковка и какая С таким кузовом автолюбители могут не переживать, что уже через несколько лет на их машине появится неприятное желтое пятно, свидетельствующее о появлении коррозии. Оцинкован ли кузов на Киа Рио и как это происходит?
Если со временем оголенный металл остается чистым и не появляется следов начала коррозионного процесса, значит оцинковка кузова присутствует.
Как правило, на автомобилях Kia Рио 3 и более ранних моделях оцинковка кузова выполнялась.
Инженеры корейского производителя утверждают, что все автомобили проходят обязательную обработку всех кузовных элементов, за исключением крыши. Данные слова подтверждают многие владельцы данной модели автомобиля.
В отзывах водителей указывается, что машины Рио третьего и более ранних поколений, при появлении сколов лакокрасочного покрытия, не проявляют признаков окисления толщина металла у киа рио коррозии.
Однако, в теме на одном из известных автофорумов, находящейся по ссылке https: Это, вероятно, можно считать браком, поскольку даже в комментариях к этой теме участвует не один десяток владельцев подобных автомобилей с более удачными корпусами. Более современные модели машин, такие как Рио и Киа Rio х Лайн не всегда толщина металла у киа рио достаточную обработку.
Так, многие владельцы новых моделей Рио жалуются, что на появившихся сколах в течение нескольких месяцев появляются следы коррозии, что свидетельствует о том, что корпуса не цинкуют или делают это некачественно.
Возникновение очагов коррозии существенно портит экстерьер Kia Rio и ухудшает надежность конструкции кузовной части транспортного средства. Виды оцинковки кузова Kia Rio Начиная с года, все автомобили Rio проходят процесс оцинковки. Данная обработка кузовных элементов носит частичный характер.
Оцинковка производится со следующими параметрами:
|
Таблица стандартной толщины датчика листового металла
- Дом
- Учебный центр
- Статьи
- Калибр для листового металла
BY: CableOrganizer.com
Калибр листового металла (иногда пишется «калибр») указывает стандартную толщину листового металла для определенного материала. По мере увеличения калибра толщина материала уменьшается.
Измерители толщины листового металла для стали основаны на весе 41,82 фунта на квадратный фут на дюйм толщины. Это известно как стандартный калибр производителей для листовой стали.Для других материалов, таких как алюминий и латунь, толщина будет другой. Таким образом, стальной лист калибра 10 и толщиной 0,1345 дюйма будет весить 41,82 * 0,1345 = 5,625 фунта на квадратный фут.
Примеры: CRS 16 г составляет 2,5 фунта на квадратный фут. Для CRS 18 ga вес составляет 2,0 фунта на квадратный фут, а для CRS 20 ga вес составляет 1,5 фунта на квадратный фут.
Калибр | Сталь | Углеродистая сталь eh | Оцинкованная сталь | Нержавеющая сталь | Алюминий | Сталь (мм) | |||||||||||||||
07 | 0.179 | — | — | — | — | 4,547 | |||||||||||||||
08 | 0,165 | 0,1644 | 0,1681 | 0,1719 | 0,1285 | 4,19114 | 0,1285 | 4,19114 | 0,1532 | 0,1563 | 0,1144 | 3,810 | |||||||||
10 | 0,135 | 0,1345 | 0,1382 | 0,1406 | 0.1019 | 3,429 | |||||||||||||||
11 | 0,120 | 0,1196 | 0,1233 | 0,1250 | 0,0907 | 3,048 | |||||||||||||||
12 | 0,105 | 0,105 | 0,105 | 0,105 | |||||||||||||||||
13 | 0,09 | — | — | 0,094 | 0,072 | 2,286 | |||||||||||||||
14 | 0,075 | 0.0747 | 0,0785 | 0,0781 | 0,0641 | 1,905 | |||||||||||||||
15 | 0,067 | — | — | 0,07 | 0,057 | 1,702 | 0,057 | 1,702 | 5 | 1,702 | 5 | 0,0625 | 0,0508 | 1,524 | |||||||
17 | 0,054 | — | — | 0,056 | 0,045 | 1,372 | |||||||||||||||
18 | 0.047 | 0,0478 | 0,0516 | 0,0500 | 0,0403 | 1,1938 | |||||||||||||||
19 | 0,042 | — | — | 0,044 | 0,036 | 1,014 | 0,044 | 0,036 | 1.014 | 0,044 | 0,036 | 1,014 | 0,014 | 0,014 | 0,014 | 0,014 | 0,0396 | 0,0375 | 0,0320 | 0,9144 | |
21 | 0,033 | — | — | 0,034 | 0.028 | 0,838 | |||||||||||||||
22 | 0,03 | — | — | 0,031 | 0,025 | 0,762 | |||||||||||||||
23 | 0,027 | — | — | 0,6 | |||||||||||||||||
24 | 0,024 | — | — | 0,025 | 0,02 | 0,61 | |||||||||||||||
25 | 0,021 | — | — | 0.022 | 0,018 | 0,533 | |||||||||||||||
26 | 0,018 | — | — | 0,019 | 0,017 | 0,457 | |||||||||||||||
27 | 0,016 | — | 0,014— | 0,406 | |||||||||||||||||
28 | 0,015 | — | — | 0,016 | — | 0,381 | |||||||||||||||
29 | 0,014 | — | — | 0.014 | — | 0,356 | |||||||||||||||
30 | 0,012 | — | — | 0,013 | — | 0,305 | |||||||||||||||
31 | — | — | —11 0,09 | — |
- Толщина выражается в дюймах, за исключением столбца мм (1 дюйм = 25,4 мм).
- Эта таблица предназначена только для справки, и настоятельно рекомендуется уточнить у местного поставщика, какие фактические значения толщины используются в вашем конкретном месте.
© 2021 CableOrganizer.com, LLC. Воспроизведение этой статьи частично или полностью без письменного разрешения CableOrganizer.com запрещено.
Основы листового металла — Old Cars Weekly
Мэтт Джозеф
Выдержка из «Библии по восстановлению коллекционных автомобилей».
Работа с листовым металлом делится на две области: ручное искусство и технические навыки.Стратегии и операции по удалению сложных деформаций (также известных как «вмятины») на деталях корпуса из листового металла настолько разнообразны, что выбор между ними сам по себе является искусством.
Обычно нет единого правильного подхода к такой сложной задаче, и различные подходы могут дать практически одинаковые результаты. Конечно, есть также множество нестандартных или неправильных подходов к этой работе, которые могут скрыть первоначальные повреждения и в то же время вызвать дальнейшие скрытые повреждения.
Три книги, показанные здесь, являются самыми основными и важными текстами для металлического человека.Тот, что слева, вырос из каталога инструментов и был первым систематическим руководством по обработке листового металла кузова автомобилей. Двое справа — это действительно одна и та же книга в разных выпусках. Они предлагают всестороннее понимание работы с листовым металлом кузова автомобилей.
Поскольку в работе с листовым металлом возможны элементы рассудительности, эффективности, опыта и даже вдохновения, это граничит с искусством. Однако другие аспекты работы с листовым металлом, такие как ковка, сварка и знание воздействия тепла на этот материал, являются в высшей степени техническими и требуют четкого понимания причин и следствий, прежде чем вы сможете понять и успешно их выполнить.Это действительно технические области, которые можно продемонстрировать научно. Результатом всего этого является то, что хорошая работа с листовым металлом требует изучения основных технических факторов, опыта в реальной работе, а также воображения и изобретательности в решении некоторых из наиболее сложных проблем, возникающих при ремонте листового металла.
Существует несколько учебников, в которых рассматриваются автомобильные листы и ремонтные работы, в частности, и одна или несколько глав посвящены ремонту листового металла в целом. Некоторые из этих книг довольно полезны для начинающих, но многие из них предназначены для использования вместе с обучением в классе.Последнее действительно не очень хорошо работает без него.
Хотя некоторые операции по механическому ремонту можно выполнять с «открытой книгой» на крыле, это никогда не годится для восстановления и повторной отделки кузова. Кроме того, классные гиды будут склонны говорить вам ровно столько, чтобы сделать вас опасным, и часто упускают из виду многое из того, что является основным. Это лучшее из них. Худшие из них, как правило, описывают процедуры, операции и материалы полностью и совершенно понятно, если вы понимаете эти вещи до того, как прочитаете описания того, как их выполнять.
Есть две книги, которые, как мне кажется, действительно дают полезное понимание того, как решать различные аспекты ремонта стального листового металла. К сожалению, один из них является для большинства слишком поверхностным, а другой — слишком подробным. Однако, если вы новичок в этой работе, вам следует взглянуть на них обоих.
The Key to Metal Bumping Фрэнка Т. Сарджента впервые был выпущен в конце 1930-х годов и в основном представлял собой руководство пользователя по инструментам для тела, производимым Fairmont Forge Company.За первоначальным выпуском последовали различные исправления и издания, и к третьему изданию (1953 г.) эта книга стала довольно хорошим трактатом о «методе Фэрмонта» при ремонте листового металла. Третье издание также включало всевозможные полезные советы по сварке и другим навыкам. Основная посылка книги заключается в том, что вы должны использовать определенный метод правки листового металла. Вы не можете просто взять молоток и начать выбивать вещи, которые кажутся «входящими», или наоборот.
Метод, предложенный в The Key … включает в себя различие между постоянно деформированным металлом и металлом, который неуместен из-за постоянно деформированного металла.Рецепт ремонта заключается в том, чтобы проанализировать порядок, в котором возникли повреждения при ударе, вызвавшем их, и устранить их в обратном порядке. The Key … — это небольшая книга, в которой многое не сказано, но это хорошее базовое руководство в области шлифования и отделки листового металла.
Во время выпуска и исправлений, The Key … был почти революционным, предлагая метод анализа и план атаки для противодействия ремонту листового металла. Я бы предположил, что предложенный план полезен, но не является единственным способом решения этих проблем.В любом случае «Ключ…» — хорошее место для начала изучения работы с листовым металлом. Его также можно легко приобрести в книжных магазинах, торгующих старыми автомобилями, и у поставщиков инструментов и принадлежностей для кузовов автомобилей.
Ремонт листового металла автомобилей , Роберт Л. Сарджент (Чилтон), и его новейшая редакция, Руководство по механике Чилтона, Том 3: Ремонт листового металла автомобилей , является наиболее полной общей книгой, которую я знаю по этому вопросу. В то время как The Key … делает эту работу удивительно легкой и простой, Сарджент сбивает читателя с толку полной сложностью каждого аспекта анализа и соответствующих операций.Конечно, это не чтение перед сном, если вы хотите спать по ночам, но если вы найдете время, чтобы прочитать его и понять, вы получите хорошее представление о теории и практике этой работы. Я настоятельно рекомендую его тем, кто хочет научиться выполнять это ремесло.
Прочитав эти книги или оставшуюся часть этой главы, вы поймете, что ремонт листового металла включает в себя больше, чем просто выбивание или выталкивание вмятины. Помимо этого, существуют подходы, которые позволят эффективно выполнить ремонт, который будет выглядеть хорошо, будет долговечным, без наполнителя или с очень небольшим количеством наполнителя и восстановит базовую целостность поврежденной панели.Это, конечно, цель. Однако независимо от того, сколько статей, книг, брошюр, видеокассет, компакт-дисков, DVD-дисков и семинаров вы пройдете по этой теме, опыт по-прежнему важен для совершенствования вашей техники обработки листового металла.
НИКОГДА не пытайтесь выполнять такую работу, основываясь исключительно на книжных знаниях. Лучше всего найти старые панели кузова: двери, крылья, капоты и т. Д., Повредить и отремонтировать их самостоятельно, чтобы почувствовать это. Вооружившись базовыми знаниями этого ремесла, вы узнаете за пять или шесть часов экспериментов с реальными деталями из листового металла больше, чем вы могли бы подумать.Я подчеркиваю этот момент, потому что я видел кузовные панели и целые автомобили, разрушенные людьми, которые думали, что кузовные работы настолько просты, насколько это делают квалифицированные специалисты или глянцевые брошюры по продаже инструментов. Это не так. Панели из лома дешевы, но ремонт повреждений, которые вы можете нанести заветной машине, обойдется дорого.
Следующая последовательность фотографий описывает основной эксперимент по деформационному упрочнению листового металла. Он показывает, как происходит наклеп и каковы его эффекты. Фактор наклепа имеет решающее значение для кузовных работ и восстановления автомобилей, поскольку он ограничивает то, как далеко вы можете перемещать металл без отжига.В эксперименте используется полоса из листового металла 22-го калибра. Он будет деформирован и выпрямлен с помощью пары плоскогубцев для листового металла, а затем молотка с низким корпусом на наковальне.
В дополнение к отработке своей техники на отрывных панелях во время раннего обучения, вы часто можете попробовать новые или альтернативные стратегии на них. Иногда легко скопировать в утиль примерно фактические повреждения того, над чем вы работаете. Затем вы можете поэкспериментировать, чтобы определить, какая стратегия ремонта будет наиболее эффективной.Панели из лома также представляют собой прекрасный перечень формованных металлических профилей для ремонта. Удивительно, как часто вы можете найти область или часть панели лома, которую можно изменить для определенного места или цели, которая у вас есть. Это может сэкономить часы работы с молотками из сыромятной кожи и мешками для дроби.
Есть много изящных уловок в кузове, которые могут сэкономить время и способствовать повышению качества, но есть и очень плохие «грязные уловки». В каждом случае важно знать, почему что-то должно работать, а не просто верить чьим-то словам.За прошедшие годы производители создали множество инструментов и материалов, которые вообще не работают или работают только в ограниченном объеме или в ограниченных ситуациях. Возьмем, например, инструменты для отбортовки панелей. Существует очень мало приложений, в которых эти инструменты можно использовать надлежащим образом и с пользой. В основном они используются для экономии времени и снижения уровня навыков, которые в противном случае потребовались бы для правильной установки панелей для стыковой сварки. При неправильном использовании эти инструменты перестают быть изящными уловками и превращаются в орудия разрушения.В этих случаях либо опыт, либо здравый смысл, либо и то, и другое должны увести вас от подобных злоупотреблений.
Металл помещается в плоскогубцы и сгибается вручную как можно ближе к губкам плоскогубцев.
Кроме того, существуют действительно грязные подходы, которые никогда не следует (в отличие от «почти никогда») использовать. На ум сразу приходит просверливание отверстий и использование крюков для тела или приварных шпилек к металлическому листу, чтобы вытащить его, когда его могли выбить сзади. Я понимаю, что вы увидите, как так называемые «профессионалы» делают это, и, фактически, я вижу несколько примеров этих и других варварских «методов», выставляемых на автомобильных выставках каждый год.Они могут работать достаточно хорошо, чтобы удовлетворять потребности низкоуровневой коммерческой работы. Это не делает их подходящими для реставрационных работ. Интуиция и здравый смысл подскажут, какие подходы вредны, а какие в интересах сохранения старых автомобилей.
Жесткий изгиб продолжается.
Одна из приятных особенностей работы с листовым металлом заключается в том, что простые инструменты и простые подходы часто лучше всего подходят для ремонта и восстановления. Кажущиеся сложными проблемы часто можно разделить на ряд более простых проблем и задач и решить их просто.Хотя доступны причудливые зажимные, тянущие, толкающие и ударные инструменты, несколько хороших молотков и тележек, а также умение правильно ими пользоваться, почти всегда обеспечат лучшую основу для восстановительных ремонтных работ на листовом металле.
Я не хочу возражать против сложного оборудования и технологий, а просто констатирую, что знания и опыт всегда являются отправной точкой в этой работе, и что многое из того, что в современном ремонтном секторе считается сложным, имеет очень большое значение. небольшое приложение для восстановления старых автомобилей.
Гибка продолжается до тех пор, пока листовой металл не будет согнут назад вокруг губок плоскогубцев настолько сильно, насколько это возможно вручную.
Листовой металл: состав, изготовление и основные характеристики
Листовой металл, используемый для изготовления автомобильных панелей и некоторых опорных конструкций панелей, представляет собой высокоразвитую и сложную серию сплавов, основанных на семействе сталей. В листовой стали используются несколько легирующих компонентов для достижения желаемых характеристик. Наиболее важным из них является углерод, который добавляют в сталь в концентрациях от 1/4 до 3/4 от 1 процента (обычно около 1/4 процента для автомобильного листового металла).Поскольку многие операции включают в себя преобразование основного сляба необработанной стали в то, что мы называем «листовым металлом», выбор характеристик, которые призвано обеспечить легирование, должен начинаться с этих преобразований. Кроме того, автомобильный листовой металл необходимо формовать в форме сложной формы, обрезать, а иногда и фланцевать. Во многих случаях он также должен быть свариваемым для прикрепления. Эти потребности диктуют особый состав стали, используемой в автомобилях.
Физические характеристики сталей определяют многочисленные технические термины.К ним относятся эластичность, твердость, пластичность, пластичность, предел текучести, вязкость и так далее. Каждый из этих терминов и несколько других имеют особое значение при описании стали.
Теперь металл зажимается губками плоскогубцев и слегка сжимается.
Наиболее интересными для нас описательными терминами являются пластичность и эластичность. Первый, пластичность, описывает способность стали формироваться под давлением (штампы) без разрыва, растрескивания или иного разрушения.Второй термин, эластичность, включает способность стали деформироваться и впоследствии возвращаться к своей первоначальной форме без каких-либо изменений в этой форме. В обоих случаях ключевым явлением является наличие или отсутствие так называемого «наклепа». Это явление представляет большой интерес для тех, кто работает с листовым металлом. Это связано с тем, что при деформации листовой стали (штамповкой, случайным ударом или молотком ремонтника) ее кристаллическая структура изменяется, в результате чего она становится более твердой и, следовательно, более устойчивой к дальнейшим изменениям.Классическим примером этого является демонстрация скрепки для бумаг, которая вначале представляет собой кусок прямой проволоки, а затем сгибается в свою обычную форму.
Тем не менее, если вы попытаетесь выпрямить один из изгибов скрепки, взяв ее прямые части на 1/2 дюйма назад от изгиба и приложив силу в обратном направлении, в котором она была приложена для изгиба, проволока будет не выпрямлять полностью. Вместо этого металл по обе стороны от исходного изгиба в конечном итоге деформируется до того, как изгиб будет полностью удален.Фотографии, сопровождающие эту главу, показывают это в отношении полосы из стали 22-го калибра шириной 1/2 дюйма.
Теперь металлическая полоса зажимается плоскогубцами как можно ближе к изгибу, и делается попытка отогнуть ее прямо вручную.
В этом примере произошло то, что исходный изгиб, который я вставил в полосу из мягкой стали, закалил ее до такой степени, что, когда я прикладываю к ней противодавление для удаления изгиба, я создаю еще две деформации обе стороны от оригинала.Металлу, прилегающему к исходному сгибу, легче деформироваться, чем металлу в исходном сгибе, потому что этот металл подвергся деформационному упрочнению за счет своей первоначальной деформации.
Явление наклепа имеет решающее значение при проектировании и производстве автомобильных панелей из листового металла. Это одновременно проблема и актив для любого, кому приходится ремонтировать листовой металл. Преимущество состоит в том, что области, где штампы деформировали листовой металл из его исходного плоского состояния, обеспечивают большую часть необходимой прочности панели при проектировании корпуса.Проблема в том, что, когда панель необходимо выпрямить из-за ударного повреждения, она затвердеет в нескольких местах и таким образом, что это может затруднить ее выпрямление, не вызывая дополнительных деформаций.
Он был закален в первоначальном процессе штамповки при его производстве. Он был дополнительно упрочнен дорожной вибрацией, которая особенно часто встречается в таких конфигурациях, как крылья понтона. Наконец, ударные повреждения еще больше укрепили его. Теперь может быть трудно или невозможно вернуть панели в форму, не имея дело с деформационным упрочнением металла, который удерживает ее в ее деформированной форме.
Участок первого изгиба отказался изгибаться прямо, и металл по обе стороны от него сначала уступил давлению обратного изгиба. Это связано с тем, что металл в исходном изгибе был закален до деформации и обеспечивал большее сопротивление изгибу, чем несогнутый металл по обе стороны от него. Без какого-либо дополнительного вмешательства это так же просто, как жена автора может достать стальную полосу руками и парой плоскогубцев для листового металла. Это наглядная демонстрация явления наклепа.Это также очень похоже на то, что происходит, когда вы пытаетесь выбить складку из крыла, ударяя молотком прямо по складке.
Иногда упрочнение можно обойти, приняв стратегию ремонта, которая заставляет вещи возвращаться на место, несмотря на это. В случае печально известной канцелярской скрепки можно согнуть ее почти обратно в прямую проволоку, если упрочненные ножки сгиба поддерживаются достаточно близко к центру сгиба во время операции реформирования. Его также можно прижать к тискам или наковальне.В других случаях эффекты наклепа настолько серьезны, что вовлеченный металл легко разрушается, прежде чем его можно будет забить молотком или заставить вернуться в исходную форму.
В этих случаях нагрев пораженного участка до «температуры трансформации» обычно является лучшим решением. Этот процесс называется «отжигом». Листовой металл кузова автомобиля потеряет эффект наклепа, если его нагреть до температуры около 1600 градусов по Фаренгейту и охладить на воздухе. Применение такого тепла позволяет кристаллической структуре металла перестраиваться таким образом, чтобы нейтрализовать эффекты деформационного упрочнения.Проблема в том, что это решение может привести к созданию панели или участков панели, которые будут иметь небольшую твердость, которая была на них изначально отпечатана. Поскольку первоначальная штамповка, вероятно, была разработана для того, чтобы вызвать деформационное упрочнение критических областей панели как элемент ее структурной прочности, отжиг может создать структурные слабости. Нагрев с последующей закалкой в воде (быстрое охлаждение) является наиболее распространенным решением выборочной повторной закалки металла способами, которые сохраняют некоторую исходную твердость штампованной панели.
Процесс штамповки — это замечательная вещь на автомобильной штамповочной фабрике. Когда вы это видите, вы можете оценить огромные силы, действующие при производстве автомобильных панелей. При штамповке огромные штампы (штампы длиной 108 дюймов довольно стандартны для больших панелей), которые весят много тонн, сжимаются вместе под огромным давлением с листовым металлом между ними. Матрицы часто смазывают, если они имеют «глубокую вытяжку». Первое действие при их закрытии заключается в том, что «связующие кольца» зажимают металл по его краям, прежде чем штампы деформируют его.Если бы этого не было сделано, металл втягивался бы в матрицу и сморщился бы под давлением закрывающих поверхностей матрицы. В новейших технологиях штамповки используются еще более массивные и сложные трехосные передаточные прессы, которые буквально превращают форму в металл.
После процесса штамповки выполняются операции обрезки и (иногда) отбортовки. Практически в каждом случае участки с высокой деформацией, такие как складки, проходящие по всей длине панели, помещаются туда для придания металлу прочности за счет преднамеренных участков деформационного упрочнения, которые будут выдерживать напряжение или нагрузку в процессе эксплуатации.
Скульптурные и ребристые стороны автомобилей обычно в такой же степени приспособлены к потребностям структурного дизайна, как и к прихотям стиля. Конечно, есть участки с большой деформацией, которые необходимы для работы, как, например, формованные концы панелей на автомобиле, которые оборачиваются так, чтобы автомобиль мог закончиться!
Операция штамповки позволяет получить три типа площади панели и бесконечное количество их комбинаций. Три основных типа: высокая, низкая и обратная.При ремонте поврежденных автомобильных панелей очень важно различать их.
Чтобы действительно выпрямить эту полосу и преодолеть деформационное упрочнение в ее изгибе, потребуется механическое усилие, как показано здесь. Это приведет к растяжению металла, если не делать это очень осторожно. Помните об этих характеристиках листового металла, когда вы собираетесь выпрямить гребень, V-образный канал или пряжку на панели из мягкой стали.
Панели с высокой короной — это панели с большой кривизной во всех направлениях.Они имеют округлый вид и отпадают с севера и юга, востока и запада. Это, конечно, панели, которые были существенно деформированы в процессе штамповки. С ними обычно намного легче работать, чем с панелями с низким венцом, потому что у них меньше склонности к изгибу под действием тепла или когда они забиты молотком после того, как были деформированы или слегка растянуты в результате удара или предыдущего ремонта. Когда панели с высокой короной обработаны должным образом, они имеют тенденцию отражать свет таким образом, чтобы это прощало, даже если их точная исходная кривизна не сохраняется при ремонте.
Напротив, панели с низкой короной довольно плоские и имеют очень небольшую кривизну на север, юг, восток и запад. Они могут иметь изгиб в одном направлении, как верх двери или крыла, где формат обычно представляет собой простой изгиб в одном направлении. Двери с плитами на Lincoln Continentals в начале 1960-х годов — еще один пример панелей с низкой крышей. Панели с низким гребнем имеют небольшую внутреннюю прочность по сравнению с панелями с высоким гребнем, потому что они претерпели очень небольшую деформацию и деформацию в процессе штамповки.Прочность часто добавляется к панелям с низким венцом за счет добавления опор или иногда путем формирования их в предварительно напряженной (монококовой) конструкции, которая иногда заимствуется из конструкции самолетов для усовершенствованной конструкции автомобилей.
С панелями с низким венцом может быть очень трудно работать, потому что, если они большие, любое растяжение приведет к их короблению, когда они вернутся к их правильной форме, если только растянутые дополнительные поперечные размеры панелей не могут быть вытеснены до их краев или спрятан где-то в местах с высокой кроной.В противном случае их необходимо аккуратно усадить при растяжении. Это может быть очень сложная процедура ремонта.
Особенно распространенный вариант этой проблемы возникает при реставрационных работах, когда в автомобилях с очень плоскими дверями эти двери заполняются водой и ржавчиной на несколько дюймов вдоль днища. Любой процесс сварки, который используется для разрезания нового металла, вызовет некоторую степень теплового искажения дверной обшивки. Это надо кропотливо устранять.
В четырехдверных автомобилях задние двери обычно должны иметь контуры, совпадающие с контурами передних дверей, таким образом, продолжая линии кузова.Дверные пары с каждой стороны автомобиля должны будут отражать свет таким образом, чтобы это указывало на равномерное и непрерывное совпадение панелей. Если это невозможно сделать, я бы посоветовал всегда ставить машину посреди большого поля или парковки без покрытия, вдали от чего-либо отличительного, что может отражать свет от его сторон и указывать на проблему! Удачи.
Панели с обратной короной — это просто панели с высокой короной в вогнутой конфигурации. Между крыльями и стволами, среди прочего, иногда встречаются области обратной короны.Как и панели с высокой коронкой, с ними обычно легче работать, чем с панелями с низкой короной, но они часто представляют собой уникальные проблемы с доступом.
Очевидно, что большинство панелей кузова старых автомобилей представляют собой комбинацию областей высокой и низкой короны с иногда добавляемой обратной короной. Когда доступен выбор относительно того, где сварить заплаточный шов или где нужно переместить небольшое количество растянутого металла, высокий и области обратной короны — хорошие ставки, если они не ослаблены отжигом или изменениями кривизны в процессе.
Последней характеристикой листового металла кузова автомобиля, которую следует учитывать, является его основной калибр или толщина. Существует полдюжины стандартов толщины проволоки и листовой стали, но автомобильные материалы обычно описываются стандартом «Стандартный калибр производителя для листовой стали». В этой системе номер калибра — это количество кусков стали определенной толщины, которые можно уместить на дюйм. Таким образом, калибр 2 будет толщиной 1/2 дюйма; 4 калибра будет толщиной 1/4 дюйма и так далее.
Автомобильный листовой металл когда-то имел толщину 18 калибра, что составляло 48 тысячных дюйма (на самом деле 0,0478 дюйма). 20-й калибр стал обычным явлением в последнее время, а это означало, что металл толщиной 0,0359 дюйма — все еще много для работы с неровностями и металлической отделкой. Однако в последнее время широкое распространение получил калибр 22 (0,0299 дюйма), а теперь на сцене появились 23 и 24 калибра (0,0269 и 0,0239 дюйма соответственно) под эвфемистическим названием «высокопрочная сталь. . » Я полагаю, что эти ужасные (для настоящих металлистов) и жалкие штучки способствуют облегчению автомобилей, но влекут за собой массу проблем.Во-первых, сплавы, используемые для его изготовления, трудно формировать при ремонте, поскольку они относительно твердые (с высоким содержанием углерода) и имеют очень низкую эластичность. Проверьте люки на некоторых современных минивэнах и хэтчбеках на любой парковке и обратите внимание на вмятины и складки, оставленные руками людей, когда они были излишне энергичны, захлопнув их.
Высокопрочные стали также настолько тонкие, что в областях, где соль и влага являются проблемой, они проявляют тревожную перфорацию ржавчины вскоре после изготовления.Применяемая к ним тщательно продуманная, широко разрекламированная и широко разрекламированная антикоррозионная обработка на самом деле обусловлена тонкостью материала, из которого изготовлены автомобили. Однако есть некоторая надежда, потому что некоторые производители начали немного увеличивать толщину панелей на своих новейших автомобилях.
Толщина металла, с которым вы работаете, может в значительной степени определить лучший способ ремонта. Если, например, когда-нибудь в будущем люди решат восстановить некоторые из экобоксов, которые украшали наши улицы и дороги в последние годы, как новые автомобили, им лучше найти хороший запас кузовных панелей NOS, прежде чем они возьмутся за такие проекты.Многие современные панели слишком тонкие, и их слишком сложно отбивать прямо, когда они серьезно деформированы. О традиционных методах отделки металла не может быть и речи, потому что файлы имеют тенденцию скользить по своему высокоуглеродистому металлу или, если они режут, они сильно ослабляют панели или прорезают их. Даже шлифование их диском может стать проблемой, если вы не будете очень осторожны.
Хорошая новость заключается в том, что толстый и относительно мягкий металл в большинстве кузовов сборных автомобилей очень чувствителен к правке, сварке и обработке металла.Когда к ним применяются некоторые из более новых технологий, такие как сварка MIG (собственно GMAW), ремонт становится настолько простым, что можно слушать радио во время работы.
Основные операции с молотком и тележкой, операции по усадке и сварке, применяемые к старым автомобилям, — это достижимые навыки, а не несбыточные мечты, которые иногда кажутся вам, когда вы пытаетесь применить их к большинству современных автомобильных кузовов.
Приобретенные характеристики старого и поврежденного листового металла
Типы повреждений, которые могут возникнуть с листовым металлом коллекторной машины, практически неограничены.Самыми распространенными, безусловно, являются коррозионные повреждения и ударные повреждения. Помимо этого, каждая машина, над которой вы работаете, вероятно, будет демонстрировать некоторые смелые инновации в области возможных дефектов листового металла. Растрескивание под напряжением обычно происходит в некоторых частях некоторых автомобилей. Кузова с деревянным каркасом часто демонстрируют структурные сдвиги, которые деформируют листовой металл, в то время как вздутая древесина каркаса может выпучивать листовой металл, что трудно устранить. В автомобилях со сварными и точечными креплениями сочетание вибрации и коррозии может привести к тому, что вещи вырвутся из строя и начнут двигаться, что приведет к серьезным беспорядкам.
Тем не менее, при всех этих возможностях, ущерб, которого я больше всего боюсь, наносят люди, вооруженные минимальными знаниями, плохим отношением, тяжелыми молотками и неправильным представлением, что они занимаются ремонтом кузовов. Когда эти типы и их приспешники добавляют ацетиленовые резаки, плазменные резаки и заклепочные пистолеты к своему базовому арсеналу молотков с зазубринами и скользящих молотов с закаленными винтами, они становятся явной угрозой для благосостояния листового металла во всем мире.
Иногда трудно представить себе степень слабоумия и вызванное этим разрушение, которое некоторые из этих художников Бондо нанесли панелям бедных автомобилей, которым посчастливилось попасть с молотка.Вместо того, чтобы тщательно анализировать характер повреждений панели, с которыми они сталкиваются, и устранять их неразрушающими способами, эти второстепенные мыслители применяют самые тяжелые молотки или самые большие монтировки, которые они могут использовать, по поврежденным участкам металла, буквально отбивая их вправо. места. В этом варварском процессе они вызывают растяжение, дальнейшую деформацию и наклеп, которые впоследствии трудно исправить.
При столкновении с ржавчиной или рваным металлом резка секций и стыковая сварка обычно выходят за рамки их ограниченного уровня квалификации, поэтому на помощь приходят инструменты для отбортовки, прутки для пайки и инструменты для заклепок.Неизбежно последует еще больший ущерб.
Эти ребята покупают пластиковый наполнитель за 55-галлонную бочку, и единственным очевидным ограничением их использования, кажется, является то, что они никогда не позволяют весу наполнителя превышать вес оригинального автомобиля. Помимо того факта, что продолжительность жизни такого рода работы составляет от 6 месяцев до 2 лет, она всегда создает серьезные проблемы, когда ее приходится переделывать кому-то, кто хочет делать ее правильно. Хорошо, вас предупредили. Также, как всегда, избегайте стереотипов.
С двумя наиболее распространенными формами повреждения листового металла, коррозией и ударом, следует бороться очень специфическими способами. Коррозионные повреждения должны быть обнаружены путем расследования, в котором помимо визуального осмотра используются физический сбор и зондирование. Это может показаться жестоким, но под, казалось бы, прочной краской могут скрываться всевозможные виды коррозии. Конечно, там, где краска вздулась и / или вздулась, есть веские основания подозревать основную коррозию. Царапающее шило — ваш лучший помощник в этом.Там, где кажется, что контуры кузова изменены, или если панели имеют толщину 1/8 дюйма или более, вы часто найдете ржавчину, стекловолоконные бинты, расклепанную кровельную жестяную банку и любые другие неприятности под поверхностью.
Фланцевые и паяные панели также часто встречаются под пузырящейся краской. Иногда, и это почти приятный сюрприз, для заделки вмятин и других повреждений от ударов используется наполнитель, потому что попытка ремонта включала затрудненный доступ к задней части панели или человеку, производившему ремонт, не хватало навыков и / или решимости ударить по ней. панель для корректировки контуров.Увы, чаще всего в этих случаях для грубого удаления вмятин использовались скользящий молоток и закаленный винт, крюки корпуса или приварные шпильки, и под Bondo скрывается серьезное коррозионное повреждение, усугубляемое попытками ремонта такого рода. .
Суть всего этого заключается в том, что единственный правильный способ исправить коррозионное повреждение, которое пробивает листовой металл, — это приварить новый металл, а единственный правильный способ справиться с ударной деформацией — это отбить его таким образом, чтобы наименьшее растяжение и коробление металла.
Иногда необходимо небольшое количество наполнителя. В таком случае корпусный свинец (на самом деле сплав олова и свинца, который сейчас широко доступен в соотношении 30/70) действительно является единственным способом проведения реставрационных работ.
В дополнение к деформационному упрочнению, которое происходит в панелях кузова, когда они штампуются, а затем подвергаются дорожной вибрации и усилиям изгиба, есть несколько других изменений в листовом металле кузова, которые происходят, когда есть ударные повреждения и попытки их ремонта.Самая важная из них — растяжка. Когда панель сильно деформируется в результате аварии, она иногда растягивается. Это означает, что давление, оказываемое на него, привело к его удлинению или расширению, или к тому и другому вместе. При этом тоже где-то похудела. К сожалению, процесс выпрямления деформированной и растянутой панели включает удары молотком по ее гребням и каналам либо непосредственно над блоком тележки, либо рядом с ним. Это часто приводит к дальнейшему растяжению металла, потому что металл становится тоньше, когда его забивают молотком.Плохой ремонт часто приводит к закалке и растяжению металла. Это может создать сложную комбинацию дефектов, которую необходимо устранить с помощью надлежащего ремонта.
Противоположность растяжению — это «осаждение», которое иногда возникает при ударном повреждении, но чаще является результатом неправильной стратегии ремонта. Это явление связано с тем, что площадь или участки металла в панели становятся толще и по бокам меньше, чем они были изначально. Если ударить плохую пряжку прямо над блоком тележки, это может вызвать расстройство, потому что металлу может некуда деваться сбоку.В результате высаженная часть панели становится толще и меньше в поперечном направлении, чем была. Этот дефект необходимо исправить, чтобы металл приобрел правильные первоначальные очертания. С расстройством можно справиться в ситуации ремонта, и, фактически, иногда его специально вызывают, чтобы преодолеть эффекты растяжения. В этом случае это называется «усадка».
Подходы к ремонту при ударах
Повреждения от ударов и коррозии иногда настолько серьезны, что необходимо найти сменные панели или изготовить и разрезать новый металл на поврежденные участки.Пример изготовления небольшой панели и сварки секций показан и описан на фотографиях и подписях к тексту следующей главы. Большая часть кузова, с которым может столкнуться реставратор, связана с незначительными повреждениями в результате аварии — вмятинами, царапинами и т.п. Именно полное устранение таких повреждений позволяет отличить очень хорошо отреставрированный автомобиль от автомобиля, который выглядит почти пропавшим.
Наиболее важным аспектом устранения такого рода повреждений является понимание материала, с которым вы работаете, — листового металла, — и иметь некоторые общие и конкретные представления о том, как он был деформирован и какие действия потребуются для его восстановления. до первоначальной формы с минимумом деформации, растяжения и осадки.Помните, неверное использование блока тележки и молотка может быть столь же разрушительным, как и события, вызвавшие повреждение, которое вы пытаетесь восстановить.
Действуйте в этих делах с очень определенным планом атаки. Часть этого плана должна быть основана на известной теории листового металла, описанной в этой книге и в книгах, упомянутых в начале этой главы. Другая часть вашего плана будет основываться на вашем опыте, полученном в результате экспериментов с утильными панелями. Дело в том, что когда вы размахиваете отбойным молотком или решаете, с чего начать удаление вмятины, работать ли «на тележке» или «вне тележки», ваши знания помогут вам, а ваш опыт даст вам интуитивное ощущение каковы будут результаты данного действия.
До публикации книги Fairmont Forge «Ключ к ударам по металлу» в 1939 году такие тексты, которые существовали в области кузовного ремонта, имели тенденцию быть расплывчатыми и подчеркивали черную магию этого ремесла. Навыки работы с листовым металлом, как правило, передавались устной традицией, а это означало, что были некоторые ужасно хорошие практикующие, а некоторые были довольно плохими. Ключ… был важным вкладом в ремесло, потому что он предлагал простой и очень понятный формат для анализа и ремонта дефектов листового металла.
Суть «метода Fairmont» заключалась в логическом различении «прямого» и «косвенного» ущерба. Прямое повреждение включает области, которые вступили в прямой контакт с поражающим объектом или объектами. Косвенное повреждение описывает области, которые деформированы и заблокированы в результате прямого повреждения, но которые фактически не подверглись прямому воздействию.
Наиболее косвенно поврежденные области в значительной степени вернутся в надлежащую форму, если прилегающие области прямого повреждения будут удалены и таким образом высвободятся силы, удерживающие косвенно поврежденные области.Штампованная сталь имеет память, которая способствует возвращению к исходному формату. Как правило, вмятины размером с портфель в основном связаны с косвенным повреждением с точки зрения площади затронутой поверхности. Метод Fairmont предписывает разблокировать большие участки листового металла, которые не деформируются сверх их пределов упругости, работая только с теми участками, которые подвержены деформации. Маленький «ключик» открывает большую загадку. Открытие метода Fairmont заключается в том, что вам не нужно брать большой молоток и бездумно бить по всему, что, кажется, выталкивается или выталкивается в процессе, который неизбежно растягивается, а работа делает металл излишне и контрпродуктивным.
Вместо этого осмотр и анализ покажут, какие области имеют прямой ущерб и, следовательно, должны быть устранены в первую очередь. Помимо проверки, применение логики позволит понять последовательность, в которой возник прямой и косвенный ущерб. Если прямое повреждение ремонтируется в порядке, обратном его возникновению, большая часть косвенного ущерба будет устранена по мере вашего продвижения.
Более современные подходы к анализу повреждений кузова и стратегии ремонта, как правило, уделяют больше внимания тому, что есть, и меньше — тому, как именно это произошло.Я склоняюсь к последнему подходу, но спешу добавить, что, если вы можете определить порядок деформации конкретного поврежденного участка, удаление составляющих повреждения в порядке, обратном их возникновению, всегда является хорошим подходом. Однако не стоит тратить полдня на теоретические рассуждения о порядке возникновения повреждений, поскольку это не является абсолютно необходимой информацией, которую нужно иметь в голове, прежде чем приступить к корректирующим мерам.
В любой теории анализа повреждений и стратегии ремонта само повреждение сводится к одной или комбинации трех возможных составляющих частей.Это V-образные каналы, выступы и пряжки (также называемые «катаные пряжки»). Эти три категории и их почти бесконечное количество комбинаций охватывают сферу деятельности. Гребни, как следует из названия, представляют собой участки выпуклого металла, которые выделяются линейным строением. V-образные каналы представляют собой углубленные области, сформированные в линии, противоположные гребням. Пряжки — это области, которые прижимаются к металлу и фиксируются в нем волнообразной формой волны, созданной в металле в результате первоначального удара.
В отличие от выступов и V-образных каналов, которые являются результатом прямого повреждения или довольно небольшого удлинения от него, пряжки образуются в результате схлопывания металла, когда он находится под давлением, и буквально не имеет другой альтернативы, кроме как схлопнуться.Пряжки часто вызывают сильную осадку, чего нельзя сказать о гребнях и V-образных каналах.
Когда вы распознаете и поймете происхождение этих трех компонентов ущерба, вы сможете выполнить эффективную стратегию по их устранению. В значительной степени ваши действия должны разблокировать то, что обычно является значительными областями косвенного ущерба.
В некотором смысле проверка хорошей стратегии состоит в том, насколько мало работы молотка и тележки необходимо для устранения повреждений. Метод анализа работает, потому что разбиение повреждений на компоненты и логическая атака на эти компоненты представляет собой эффективную атаку на причины проблемы.Альтернатива, бездумная атака на симптомы повреждения, заканчивается подходом «большего молотка» и обычно не позволяет распознать даже такие очевидные компоненты повреждения, как изгиб каркаса. Он заменяет интеллект и навыки разрушительной контрсилой. По этой причине обычно это не удается.
НАЖМИТЕ ЗДЕСЬ, ЧТОБЫ СТАТЬ ДЛЯ ВОССТАНОВЛЕНИЯ БОЛЬШЕ
Более толстая сталь всегда лучше для сейфов
Дверь и стены вашего сейфа — первая линия защиты от мошенников.Чем толще сталь, тем лучше будет защита вашего сейфа. Вот что вам следует знать о толщине стали, используемой, чтобы сделать ваш Liberty безопасным, а его запорные планки в стиле милитари — еще более надежными.
Общие сведения о толщине датчика
Концепция стального калибра может немного сбить с толку. Листовой металл использует так называемую регрессивную шкалу. Чем ниже номер калибра, тем толще и прочнее сталь. По мере увеличения калибра толщина стали уменьшается на 10 процентов.
Когда дело доходит до сертификации в качестве жилого охранного контейнера (RSC), внесенного в список UL, толщина стали определенно имеет значение. Сейф не может получить сертификат RSC, если он не имеет стального калибра 12 или ниже.
Liberty использует сталь 5 разной толщины
Для изготовления различных моделей сейфов Liberty используется сталь пяти разных толщин. Используемая толщина помогает определить уровень безопасности сейфа:
- Сейфы уровня 1, такие как Centurion, изготовлены из стали 14-го калибра
- Сейфы 2-го уровня, например, в США, изготовлены из стали 12-го калибра
- Сейфы 3-го уровня, такие как Colonial и Fatboy 47, изготовлены из стали 11-го калибра .
- Сейфы 4-го уровня, такие как Franklin и Fatboy 64, изготовлены из стали 11-го калибра
- Сейфы 5-го уровня, такие как Lincoln, изготовлены из стали 11-го калибра
- Сейфы 6-го уровня, такие как Classic Select, изготовлены из стали 11-го калибра .
- Сейфы 7-го уровня, такие как Classic Plus, изготовлены из стали 10-го калибра
- Сейфы 8-го уровня, такие как Presidential и Magnum, изготовлены из стали 7-го калибра
Чтобы лучше понять прочность стали меньшего калибра, примите во внимание следующее:
- Сталь 12 калибра — 2.В 86 раз прочнее, чем сталь 14-го калибра Сталь
- 11-го калибра в 1,45 раза прочнее стали 12-го калибра Сталь
- 10-го калибра в 1,42 раза прочнее, чем сталь 11-го калибра
4 разные толщины стали для стопорных стержней в стиле милитари
Стальные фиксаторы в стиле милитари намного надежнее , чем традиционные круглые стальные штифты. Liberty использует сталь трех разных толщин для наших запорных планок в стиле милитари, в том числе:
- Сейфы уровня 1, такие как Centurion, оснащены запирающими планками толщиной 3/16 дюйма
- Сейфы 2-го уровня, такие как США, оснащены запирающими планками толщиной 1/4 дюйма
- Сейфы 3-го уровня, такие как Colonial и Fatboy 47, оснащены запирающими планками толщиной 1/4 дюйма
- Сейфы 4-го уровня, такие как Franklin и Fatboy 64, оснащены запирающими планками толщиной 1/4 дюйма
- Сейфы 5-го уровня, такие как Lincoln, оснащены запирающими планками толщиной 3/8 дюйма
- Сейфы 6-го уровня, такие как Classic Select, оснащены запирающими планками толщиной 3/8 дюйма
- Сейфы 7-го уровня, такие как Classic Plus, оснащены запирающими планками толщиной 3/8 дюйма
- Сейфы 8-го уровня, такие как Presidential и Magnum, оснащены запирающими планками толщиной 1/2 дюйма
Да… Более толстая сталь стоит дороже
При покупке сейфа всегда полезно выбрать сейф из самой толстой стали, который будет соответствовать вашему бюджету.Более толстая сталь действительно увеличивает цену сейфа, но она стоит дополнительных денег из-за своей прочности и большего веса.
4 причины, по которым толщина стали жизненно важна для безопасности вашего оружия
Понимание калибровочных рейтингов
Всегда проверяйте номинал калибра на сейфе для оружия, прежде чем принимать решение о покупке. А если вы не можете найти этот рейтинг в сейфе или в списке его технических характеристик, обратитесь к своему дилеру за дополнительной информацией. Если вы не знакомы с тем, как работают рейтинги датчиков, они могут немного запутать.Чем выше номинал калибра, тем тоньше сталь, пригодная для огнестрельного оружия. Следовательно, вы хотите искать сейф с более низким рейтингом калибра .
Сталь более низкого качества, безопасная для огнестрельного оружия, обычно имеет калибр от 14 до 20. Это означает, что стальные стенки сейфа очень тонкие. Вероятность того, что они устоят перед атакой дрели или любопытства, мала. Безопасный для оружия металл калибра 14 имеет толщину 1,626 мм (0,064 дюйма), а металл калибра 20 — всего 0,9 мм (0,037 дюйма).
Вы должны попытаться выбрать сейф из толстой стали толщиной от 12 до 6 для максимальной защиты.Безопасный для оружия металл калибра 12 имеет толщину 2,057 мм (0,081 дюйма), а калибра 6 — 4,166 мм (0,164 дюйма). Вы заплатите больше за более толстую безопасную для оружия сталь, но оно того стоит.
Вот четыре причины, по которым толщина стали жизненно важна для безопасности вашего оружия:
Причина № 1 — Толстая безопасная сталь для пистолета означает более прочный сейф
Когда дело доходит до для защиты вашего огнестрельного оружия и ценностей вашей семьи , каждый более толстый калибр увеличивает прочность вашего сейфа в большей степени. Удвоение толщины, как переход с 12 на 6, делает сталь в восемь раз прочнее.
Причина № 2 — Толстая сталь — лучший металл для сейфов
При покупке сейфа убедитесь, что его толстые стенки сделаны из стали хорошего качества . На самом деле на рынке есть несколько оружейных сейфов, которые сделаны из алюминиевого сплава, который не так прочен, как сталь.
Причина № 3 — Толстая сталь обеспечивает лучшую защиту от огня
Оружейные сейфы , обеспечивающие максимальную противопожарную защиту , обычно имеют более толстые стальные стенки. Однако не стоит думать, что все сейфы с толстыми стенками предназначены для защиты от огня.Такой сейф также должен иметь дополнительные противопожарные средства, в том числе многослойный огнестойкий гипсокартон .
Причина № 4 — Великое спокойствие
Сейф, сделанный из толстой стали, может дать вам и вашей семье больше душевного спокойствия; ваше огнестрельное оружие и ценные вещи защищены от кражи и пожара. В конце концов, разве это не главная причина иметь сейф для оружия?
Алюминий для корпусов общего назначения
Алюминий
Видео с техническими советами по Protocase
Краткое видео о выборе металла
Алюминий устойчив к коррозии и имеет небольшой вес.
Он имеет более низкую структурную жесткость, чем сталь (около 1/3), что необходимо компенсировать более толстым калибром.
Поверхность:
Порошковое покрытие, без отделки или шероховатости
Крепежные детали:
Обычно крепежи из нержавеющей стали используются с алюминием. Однако в некоторых случаях в зависимости от области применения используются оцинкованные крепежные детали.
Дополнительные примечания для крепежа с алюминием: Алюминиевый крепеж очень мягкий и поэтому имеет низкую физическую прочность.В результате мы НЕ храним их на складе. Однако в некоторых приложениях они могут быть полезны, например, в деталях, которые используются в агрессивных жидкостях, таких как соленая вода. Другие комбинации разнородных металлов могут вызвать гальваническую коррозию.
Алюминиевый сплав на складе (листовой металл)
5052 Алюминий — h42
5052 Алюминий оптимален для обработки листового металла и очень легко формуется при комнатной температуре.Этот материал очень гибок и поэтому может работать с небольшими радиусами. Нетермообрабатываемый сплав, алюминий 5052, легко сваривается обычными методами. Обладает хорошими формовочными характеристиками и хорошей коррозионной стойкостью, в том числе стойкостью к соленой воде. Алюминий 5052 также относительно легко обрабатывать.
Примечание: См. Меры предосторожности на манометрах.
Калибр | Толщина | Допуск толщины |
---|---|---|
(0.250 дюймов | 6,35 мм) | ± 0,014 « | |
(0,188 дюйма | 4,78 мм) | ± 0,009 « | |
8 калибр | (0,1285 дюйма | 3,26 мм) | ± 0,007 | ± 0,18 мм |
10 калибр | (0,102 дюйма | 2,59 мм) | ± 0,006 | ± 0,15 мм |
11 калибр | (0.091 «| 2,31 мм) | ± 0,0045 « |
12 калибр | (0,081 дюйма | 2,06 мм) | ± 0,0045 « |
14 калибр | (0,064 дюйма | 1,63 мм) | ± 0,0040 « |
16 калибр | (0,051 дюйма | 1,30 мм) | ± 0,0035 « |
18 калибр | (0.040 «| 1,02 мм) | ± 0,0035 « |
20 калибр | (0,032 дюйма | 0,81 мм) | ± 0,0030 « |
6061 Алюминий — T6
Алюминий — это сплав общего назначения, обычно используемый при штамповке, а также доступен для изготовления листового металла. Однако он не рекомендуется для работы с листовым металлом, поскольку он имеет тенденцию к растрескиванию по внешнему радиусу, когда выходит за пределы своей текучести (и, следовательно, требует гораздо большего радиуса для правильного изгиба).Алюминий 6061 также очень легко обрабатывать.
Калибр | Толщина | Допуск толщины |
---|---|---|
(0,1285 дюйма | 3,26 мм) | ± 0,007 « | |
(0,188 дюйма | 4,78 мм) | ± 0,009 « | |
(0.250 дюймов | 6,35 мм) | ± 0,014 « | |
(0,375 дюйма | 9,53 мм) | ± 0,017 « | |
(0,500 дюйма | 12,7 мм) | ± 0,023 « |
Обратите внимание: наши поставщики предоставили указанные выше данные о материалах с номинальной толщиной, основанной на отраслевых стандартах.
Примечание. Калибры обычно не используются при указании алюминия, поскольку фактическая толщина алюминия более признана во всем мире. Он начинается с листа по толщине и переходит в пластину на более толстом конце шкалы.
Листовой металл — материалы, стандартные размеры и процессы формования
Листовой металл сегодня является основой всего машиностроения.Мы видим это повсюду — от машин и техники до фасадов домов и мебели.
Чтобы использовать листовой металл в полной мере, инженеры должны сначала кое-что узнать об этом. Сюда входят стандартные размеры, материалы, различия в производстве и возможные методы формования.
Что такое листовой металл?
Листовой металл — это одна из форм и форм, в которых можно купить металл. Листовой металл — это любой металл, имеющий толщину от 0,5 до 6 миллиметров.
Однако существуют и другие единицы измерения, используемые для классификации металлов по толщине.
Миллиметры, мил и калибр
Пленки, листы и пластины практически одинаковы, с той лишь разницей, что разница в толщине. Толщина измеряется тремя способами — миллиметрами, милами и калибрами. В то время как миллиметр — довольно простая единица измерения, милы и калибры используются только в инженерии и производстве.
Один мил равен одной тысячной дюйма. Поскольку британцы часто используют «mils» во множественном числе для обозначения миллиметров, это может немного сбивать с толку, но разница важна.
Датчик — это еще одна единица измерения толщины листового металла. Хотя официальные стандарты не рекомендуют использовать манометры, они не так уж и редки. Калибр представляет собой толщину металла по отношению к его весу на квадратный фут. Чем больше номер калибра, тем меньше толщина.
Поскольку это связано с весом металла, фактическая толщина (мм) для одного и того же калибра различается для разных металлов (например, сталь 12 мм и алюминий 12 мм).
Фольга, лист и пластины
Пройдя по основным системам измерения, мы можем теперь взглянуть на категоризацию фольги, листов и пластин.Для наших целей мы будем использовать миллиметры в качестве единицы измерения.
Металлическая фольгаМеталлическая фольга особенно часто используется с алюминием, ее часто называют оловянной фольгой. Толщина фольги обычно до 0,2 мм.
Листовой металл следующий на очереди. Толщина листового металла от 0,5 мм до 6 мм. Все, что выше, — это металлическая пластина.
Тонкий листовой металл легко поддается формовке, но при этом обладает высокой прочностью. При относительно невысокой цене он отлично подходит для большинства инженерных целей.Вот почему мы видим это повсюду вокруг нас.
В конце статьи мы обсудим различные методы формования листового металла.
Общие материалы
Практически все обычные технические металлы также используются в виде листов. Некоторые из них — углеродистая сталь, нержавеющая сталь, медь и алюминий. Выбор подходящего для вас зависит от области применения и требований вашего продукта.
Металлические листы имеют те же механические свойства, что и основной металл.Таким образом, стальные листы обладают высокой прочностью на разрыв и долговечностью, подходящей для использования в конструкциях и машинах.
В то же время медные листы часто находят применение в качестве декоративного слоя на современных зданиях.
Стандартные размеры
Стандартные измерения применимы как к размеру, так и к толщине листа. Хотя для достижения больших размеров листов есть несколько обходных путей с помощью сварки, вы не можете смотреть за пределы таблиц толщины.
Стандартные размеры листового металла
Знание стандартных размеров листов поможет вам оптимизировать компоновку деталей.Много раз мы получали детали для производства, которые были немного больше стандартного размера. Это означает больше брака и более высокие общие затраты для клиента.
Также следует иметь в виду, что доступны листы разных размеров. В то время как листы малого, среднего и большого размера почти всегда есть в наличии на складе каждого производителя листового металла, листы негабаритных размеров могут отсутствовать.
Многие из них могут также не иметь оборудования для резки таких больших листов. Так что знание возможностей ваших производителей здесь пригодится.
Иногда можно просто сварить два листа меньшего размера, но это не оптимальное решение. Особенно, если уделять большое внимание эстетике вашего проекта.
Стандартная толщина листового металла
В таблице выше указаны стандартные толщины листового металла и металлических листов. Как видите, на каждый вид металла существуют свои стандарты.
Также полезно обращать внимание не только на начальную и конечную точки, но и на фактические значения.Довольно часто кто-то просит нестандартную толщину.
Исключения из этой таблицы определенно существуют. Мы просто советуем вам следить за этими значениями толщины из-за трудностей с поиском материалов. Все вышеперечисленные легко доступны у многих производителей листового металла.
Горячекатаный лист и холоднокатаный лист
Существует два способа производства листового металла — горячая прокатка и холодная прокатка. Глядя на приведенную выше таблицу стандартной толщины, вы можете увидеть, как используются эти две толщины.В случае конструкционных сталей холодная прокатка идет только до 3 мм. С этого момента листы и плиты подвергаются горячей прокатке в целях экономии.
Хотя процесс горячей прокатки снова начинается с 3 мм для нержавеющих сталей, холодная прокатка охватывает все листы, то есть до 6 мм.
Для инженерных целей важно различать их. Для прецизионных применений предпочтительнее холоднокатаная сталь, так как мы можем лучше контролировать конечные размеры. Это связано с тем, что в горячекатаных сталях после охлаждения сталь слегка усаживается и форма может немного измениться.
Процессы формовки листового металла
Итак, мы наконец добрались до методов формования листового металла. На столе есть множество вариантов, и решение остается за вами.
Выбор во многом зависит от желаемого результата. Но многие из этих методов дают, казалось бы, аналогичный или совпадающий результат. Затем все сводится к стоимости (часто зависит от размера партии), доступности и желаемой точности.
Гибка листового металла
Гибка — это процесс формования, при котором листовой металл сгибается в желаемую форму за счет приложения напряжения изгиба.Листовой металл изгибается, поэтому достигается пластическая деформация. Это не дает металлу вернуть прежнюю форму.
Гибка на воздухе с помощью V-образной матрицыТакие детали, как фланцы и гофры, создаются путем гибки. Самая распространенная форма гибки — это V-образная гибка. Там V-образная матрица и пуансон сжимают вместе, чтобы придать листу желаемую форму.
Гибка кромок — это еще один распространенный метод гибки фланцев с использованием протирочной матрицы и пуансона.
Скручивание листового металла
Скручивание — это процесс формирования круглого кольца на краю металлического листа, чтобы сделать его более безопасным в обращении.
Есть разница между загнутым краем и каплевидным краем. При скручивании начальный край свертывается в сформированный круг, тогда как при каплевидном рубчике начальный край остается открытым.
Керлинг также можно разделить на керлинг со смещением от центра и керлинг. У валков со смещением от центра центр находится над уровнем листа, а у валков со смещением от центра центр находится на том же уровне, что и у металлического листа.
Обрезка листового металла
Обрезка — это процесс удаления изгиба с листа металла.В листе металла, особенно в деталях в форме полосы, возникает горизонтальный изгиб, когда он расплющивается в листы.
При расчесывании мы устраняем этот горизонтальный изгиб, выравнивая края, чтобы убрать изгиб. Усилие прикладывают к деформированному краю, а не к лицу, чтобы придать ему прямую форму. Обычно это выполняется на участках ограниченной длины.
Глубокая вытяжка
Процесс изготовления банок с ДИ методом глубокой вытяжки
Глубокая вытяжка — это процесс формования листового металла, при котором форма листа изменяется на желаемую в несколько этапов с использованием ряда штампов.Только если глубина сформированной формы превышает исходный диаметр листа, это считается глубокой вытяжкой.
Пуансоны и матрицы используются для внесения изменений на каждом этапе. Используя этот процесс, лист преобразуется во множество различных форм, таких как топливный бак, раковина и автомобильные детали. Глубокая вытяжка в основном используется для крупносерийного производства.
Листовой металл Расширяющийся
Линия по производству металлопродукции Bender SP-1250
В этом процессе обработки металла лист металла пропускается через перфорирующие ножницы, где он разрезается и растягивается в виде узора.Обычно предпочтительна ромбовидная сетка, поскольку она имеет структурное преимущество перед другими формами.
Этот процесс формования обычно используется для изготовления ограждений, мостков, платформ, решеток и т. Д. В результате получается самодренирующийся прочный продукт, способный выдержать вес, на который он рассчитан.
Эти продукты могут использоваться там, где требуется прохождение воздуха или жидкости, но необходимо предотвратить прохождение более крупных частиц, например просеивание. Сохраняется прочность исходного металла.
Гидроформинг
Как это сделано — гидроформованные детали шасси 1232
Гидроформование — это инновационный способ придания металлическим листам желаемой формы. В этом процессе металл помещается на матрицу, но вместо пуансона для придания формы листу используется жидкость под высоким давлением.
С помощью этого процесса можно создавать более сложные детали в более короткие сроки. Это также сравнительно дешевле и требует меньше работы. Гидроформовка также совместима практически со всеми материалами, такими как нержавеющая сталь, алюминий, углеродистая сталь, латунь и драгоценные металлы.
Поскольку подходящие штампы обычно не требуются, гидроформование можно использовать для формования нестандартных форм.
Инкрементальное формование листа
Одноточечное инкрементальное формование в Университете Авейру — проект SPIF-A
Постепенное формование листа — это процесс обработки металла, при котором листовой металл приобретает определенную форму. Это возможно только при малых объемах.
В продукт можно внести изменения быстро и без особых хлопот. В этом процессе продукт формируется поэтапно.
Листовой материал имеет форму одноточечной сферы.
Хотя этот процесс дает результаты, аналогичные результатам глубокой вытяжки, он не требует отдельного набора штампов и штампов. Так что самое большое преимущество этого метода — его гибкость.
Гладильная
Процесс глажки используется, когда необходимо уменьшить толщину в определенной области листового металла. Это позволяет производителю получать однородную толщину стенок при глубокой вытяжке изделий.
Хорошим примером глажки является процесс производства банок из-под газировки.Стенки банки необходимо утончить до заданной толщины. Обычно требуется 2 или 3 процесса глажки с разными матрицами, чтобы получить желаемую толщину в алюминиевых банках из-под соды. Этот процесс глажки осуществляется в сочетании с глубокой вытяжкой.
Лазерная резка
Лазерная резка все чаще используется для резки листового металла. Он точен, а поверхность очень гладкая. Станки с ЧПУ обычно используются для резки определенных форм.
После подачи программы конкретная резка выполняется лазером.Лазерная резка имеет преимущество гибкости. При необходимости можно легко изменить требуемую форму. Также возможно разрезать металлические листы на очень сложные части с помощью услуг лазерной резки.
Фотохимическая обработка
Химическое травление: обзор процесса (3D-анимация)
Фотохимическая обработка — это процесс, в котором проводится контролируемая коррозия для изготовления деталей из листового металла в соответствии с требованиями.
В этом процессе фоторезист и травитель используются для придания металлическому листу его формы. Метод был разработан в 60-х годах и даже сегодня является сравнительно недорогим методом.
С помощью фотохимической обработки можно резать любой металл. Процесс идеален для массового производства. Если требуются изменения, их можно легко осуществить.
Как и при лазерной резке, этот процесс чрезвычайно точен и обеспечивает гладкую поверхность. Этот процесс используется для изготовления очень мелких сеток, отверстий, гибких нагревательных элементов, металлических прокладок, электрических контактов и украшений.
Пробивка
Пробивка отверстий — очень распространенный метод вырезания отверстий в листовом металле. Установка состоит из пуансона и штампа. Между ними очень маленький зазор.
Когда пуансон и матрица встречаются, материал сжимается между ними, и с последующим толчком усилие сдвига вырезает отверстие в листе. Этот процесс относительно недорог в больших количествах и позволяет пробивать отверстия как в полосе, так и в листе.
Можно пробивать отверстия различных размеров, но обычно рекомендуется, чтобы диаметр отверстия был больше толщины пробиваемого материала.Для особо прочных сплавов разница между диаметром отверстия и толщиной должна быть больше.
Роллинг
Прокатка может выполняться на листовых металлах для уменьшения общей толщины металлического листа или для того, чтобы сделать его более однородным. В этом процессе листовой металл пропускается через набор валков.
В зависимости от температуры процесс классифицируется как горячая или холодная прокатка. При горячей прокатке температура стали составляет около 1400 градусов по Фаренгейту.Это может помочь достичь толщины от 1/16 дюйма до 5/16 дюйма.
При холодной прокатке процесс осуществляется при комнатной температуре. Материал промывают кислотой и подвергают термообработке для достижения хорошего результата.
Листовой валок / Листовой валок / Гибка листового металла / Rundbiegemaschine Motor / Hengerítőgép
Прокатка — еще один способ получения изгибов с большим радиусом. Вместо использования листогибочных прессов для ступенчатой гибки, это дает большой равномерный радиус без необходимости непрерывной ручной работы в процессе.
Листогибочный пресс
В этом процессе длинный лист металла изгибается вокруг прямой оси, проходящей через материал. В зависимости от пуансона и матрицы может быть образован материал «V», «U» или канал в форме.
Хотя это выглядит просто, прецизионная гибка является сложной задачей при формовании листогибочным прессом. Свойства материала необходимо учитывать вместе с прессом и инструментами, чтобы улучшить степень упругости.
Листогибочный пресс может также использоваться для более мелких деталей, что делает его пригодным для изготовления более мелких деталей наряду с крупными.Толщина до 25 мм легко изгибается, а длина детали может достигать 6 м.
Уилинг
Английское колесоВ этом процессе формования используется английское колесо для растягивания и изгиба плоских металлических листов в требуемые формы. Этот метод требует высококвалифицированной рабочей силы и поэтому стоит дорого. Этот метод нельзя использовать для массового производства. Wheeling в основном используется для производства небольших объемов индивидуальных деталей для старых автомобилей.
Он также используется для изготовления деталей из листового металла для прототипов автомобилей и самолетов.