Детали механизма автосцепки ~ Вагонник
Автосцепное устройство обеспечивает автоматическое сцепление вагонов между собой.
Автосцепное устройство воспринимает растягивающие и сжимающие усилия, а также ударные нагрузки, возникающие в пути следования поезда и при маневрах.
Автосцепное устройство одного конца вагона состоит из:
1. Автосцепки.
2. Упряжного устройства.
3. Ударно-центрирующего прибора.
Автосцепка служит для сцепления единиц подвижного состава, а также передачи тяговых и ударных нагрузок.
Автосцепка СА-3 является тягово-ударной нежесткого типа. Автоматической сцепке присвоено обозначение СА-3 (советская автосцепка, третий вариант). На каждом грузовом вагоне установлено две автосцепки, которые устанавливаются по концам рамы вагона.
Корпус автосцепки представляет собой пустотелую фасонную отливку, состоящую изголовной части (1) и хвостовика (2). Внутри головной части размещаются детали механизма автосцепки.
Головная часть автосцепки (голова) переходит в удлиненный пустотелый хвостовик, в котором имеется отверстие (1) для размещения клина, соединяющего автосцепку с тяговым хомутом. Часть хвостовика, расположенная между отверстием (1) для клина и торцом, называется перемычкой (2). Голова автосцепки имеет большой (3) и малый (4) зубья.
Вверху замок снабжен шипом (1), служащим для навешивания предохранителя. В средней части замка находится овальное отверстие (2), через которое пропускается валик подъемника. Снизу замка расположены направляющий зуб (3) и сигнальный отросток (4), окрашенный в красный цвет. Прилив (5), имеет прорезь (6) под нижнее плечо предохранителя.
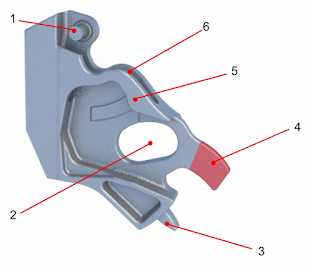
Подъемник замка предназначен для того, чтобы при расцеплении автосцепок нажать на нижнее плечо предохранителя, отвести замок из зева внутрь головы и с помощью замкодержателя поддерживать его в расцепленном положении до разведения автосцепок. Подъемник замка имеет узкий (1) и широкий (2) пальцы.
www.xn--80adeukqag.xn--p1ai
Автосцепка са-3. Конструкция
НАЗНАЧЕНИЕ АВТОСЦЕПНЫХ УСТРОЙСТВ
Автосцепки могут быть разделены на две большие группы: механические автосцепки, т, е. обеспечивающие автоматическое сцепление единиц подвижного состава, и унифицированные автосцепки, которые, помимо сцепления, предусматривают соединение межвагонных коммуникаций, включающих в себя один или два воздухопровода, а при необходимости и контакты электро- и радиоцепей, а также паропроводы отопления.
Механические автосцепки применяются для сцепления грузовых и пассажирских вагонов общего назначения; при этом межвагонные коммуникации соединяются вручную. Унифицированные автрсцепки устанавливают на специиальном подвижном составе: вагонах метрополитенов, некоторых типах зарубежных электро- и дизель-поездов и др.
Автосцепное устройство подвижного состава советских железных дорог общего назначения бывает двух типов: вагонного и паровозного.
Автосцепное устройство вагонного типа устанавливается на грузовых и пассажирских вагонах, тепловозах, электровозах, вагонах дизель- и электропоездов и тендерах паровозов, а паровозного — на паровозах, мотовозах, автодрезинах и некоторых специальных вагонах.
Узлы и детали автосцепного устройства вагонного типа имеют следующее назначение.
Автосцепка 13 (рис. 1) служит для сцепления единиц подвижного состава, а также передачи тяговых и ударных нагрузок. Поглощающий аппарат 5 смягчает удары и рывки, предохраняя подвижной состав, грузы и пассажиров от вредных динамических воздействий. Тяговый хомут 6 через клин 5 передает поглощающему аппарату тяговое усилие от автосцепки.
Рис. 1. Автосцепное устройство вагонного типа и его детали
Передний 9 и задний 1 упоры (объединенные упорные угольники), расположенные между стенками хребтовой балки, передают нагрузку на раму. На современном подвижном составе передний упор отлит вместе с
Задний упор воспринимает ударные нагрузки непосредственно от корпуса поглощающего аппарата.
Ударная розетка упора 9 предназначена для усиления концевой балки рамы вагона или локомотива и восприятия в некоторых случаях части удара непосредственно от автосцепки наряду с поглощающим аппаратом.
Центрирующий прибор, состоящий из двух маятниковых подвесок 7 и центрирующей балочки 12, возвращает автосцепку после бокового отклонения в центральное положение. Расцепной привод
В автосцепном устройстве восьмиосных вагонов (рис. 2, а) соединение автосцепки с тяговым хомутом выполнено посредством цилиндрического валика 3. Между валиком и автосцепкой находится вкладыш 12 (рис. 2, б) . Валик удерживается от выпадания с помощью планки 5, проходящей через отверстия в переднем упоре 6. Автосцепка 10 (см. рис. 2, а) восьмиосного вагона является полужесткой, так как имеет ограничитель 11, препятствующий разъединению автосцепок при их больших относительных перемещениях. В центрирующем приборе находится подвижная плита 8 с направляющими, опирающаяся на пружины 9. Для обеспечения сцепляемости восьмиосных вагонов в кривых участках пути небольшого радиуса эти вагоны оборудуются направляющим механизмом, состоящим из торсиона 2 (П-образного рычага из пружинной стали), укрепленного во втулках 4.
Рис. 2 Автосцепное устройство вагонного типа для восьмиосных вагонов
(а) и узел соединения с тяговым хомутом (б)
Один конец торсиона связан с приливом 7 центрирующей балочки, а другой — с соединительной балкой 1 тележки. При движении по кривой соединительная балка перемещается относительно вагона, нажимая на вертикальную часть торсиона, и отклоняет автосцепку в сторону к центру кривой, обеспечивая необходимый горизонтальный захват автосцепки.
У автосцепного устройства паровозного типа (рис. 3) нет поглощающего аппарата и связанных с ним деталей. Паровозная розетка 2, предназначенная для передачи усилий от автосцепки 1 на раму подвижного состава, закреплена на концевой балке болтами 5 с гайками 6 и шплинтами.
Рис 3 Автосцепное устройство паровозного типа и его детали
Автосцепка соединена с розеткой цилиндрическим валиком 3, который проходит через отверстия в розетке и автосцепке. От выжимания вверх валик удерживается запорным болтом 4. Центрирующий прибор, состоящий из пружин 7 и стаканов 8, возвращает автосцепку в центральное положение после боковых отклонений.
Автосцепка СА-3 (рис. 1) является тягово-ударной нежесткого типа. Она состоит из корпуса 4 и деталей механизма сцепления: замка 5, замкодержателя 2, предохранителя 3, подъемника 6, валика подъемника 7.
Рис 1 — Автосцепка СА-3
Головная часть автосцепки (голова) переходит в удлиненный пустотелый хвостовик, в котором имеется отверстие 1 для размещения клина, соединяющего автосцепку с тяговым хомутом. Голова автосцепки имеет большой 10 и малый 9 зубья. В пространство между малым и большим зубьями, в так называемый зев автосцепки, выступают замок 5 и замкодержатель 2, взаимодействующие в сцепленном состоянии со смежной автосцепкой.
Большой зуб имеет три усиливающих ребра: верхнее, среднее и нижнее, плавно переходящие в хвостовик и соединенные между собой перемычкой. Голова автосцепки заканчивается сзади упором 8. предназначенным для передачи при неблагоприятном сочетании допусков жесткого удара на хребтовую балку через концевую балку рамы вагона и ударную розетку.
Очертание в плане малого 7 (рис. 2) и большого 2 зубьев, а также выступающей в зев части замка 3 называется контуром зацепления автосцепки.
Рис. 2. Стандартный контур зацепления автосцепки
Для обеспечения взаимосцепляемости всех автосцепок СА-3 контур зацепления должен соответствовать ГОСТ 21447—75. Линия I-I является продольной осью автосцепки. Внутренние стенки кармана корпуса, в котором находится механизм автосцепки, смещены относительно этой оси на 10°, а замыкающая поверхность замка расположена под углом 15°. Вследствие такого размещения механизма сцепления равномерно распределяется продольное усилие между замком, малым и большим зубьями. Ось II-II (ось зацепления) перпендикулярна оси I—I и проходит через точку О, называемую центром зацепления. По оси II-II обычно устанавливают расстояние автосцепки от концевой балки.
Корпус (рис.3), являющийся основной частью автосцепки, предназначен для передачи тяговых и ударных нагрузок, а также размещения деталей механизма сцепления. Хвостовик корпуса имеет постоянную высоту по длине. Его торец 1 — цилиндрический, что обеспечивает перемещение автосцепки в горизонтальной плоскости. Часть хвостовика, расположенная между отверстием 2 для клина тягового хомута и торцом, называется перемычкой.
Рис. 3 — Корпус автосцепки
Поверхности контура зацепления корпуса в сцепленном состоянии взаимодействуют со смежной автосцепкой: при сжатии усилие воспринимается ударной 6 и боковой 7 поверхностями малого зуба, ударной стенкой 5 зева и боковой поверхностью 4 большого зуба, а при растяжении — тяговыми поверхностями 8 малого и 3 большого зубьев. Тяговая, ударная и боковая поверхности малого зуба, а также тяговая поверхность большого зуба в средней части по высоте имеют вертикальную площадку длиной 160 мм (80 мм вверх и 80 мм вниз от продольной оси корпуса). Эти поверхности выше и ниже вертикальной площадки скошены для улучшения условий работы сцепленных автосцепок, когда между их продольными осями в вертикальной плоскости возникает угол (при прохождении горба сортировочной горки).
Корпуса автосцепок ранних выпусков имеют сбоку со стороны малого зуба прилив 10 (ухо), на который в период перехода с винтовой упряжки на автосцепку навешивали скобу винтовой упряжи смежного вагона во время маневровых работ, а также в передаточных поездах. После перевода подвижного состава на автосцепку новые корпуса сначала изготовлялись с приливом вместо уха, а затем без прилива с утолщением стенки малого зуба.
У выпускаемых корпусов автосцепок высота малого зуба увеличена и его нижняя кромка используется для приварки ограничителя вертикальных перемещений, необходимого для некоторых типов вагонов, поэтому кромка выполнена горизонтальной.
Рис. 4 — Корпус автосцепки: вид А
На корпусе со стороны малого зуба сделан прилив 9 с отверстиями для валика подъемника и запорного болта. В ударной стенке 5 зева имеются два окна: большое 11 для выхода в зев замка и малое 12 для выхода лапы замкодержателя.
Приливы и отверстия в кармане корпуса служат для размещения деталей механизма и правильного их взаимодействия.
Рисунок 5 -Внутренняя полость (карман) автосцкпки
Серповидный прилив (рис. 5) вверху на внутренней стенке малого зуба ограничивает перемещение замка внутрь кармана. Нижняя часть прилива переходит в полочку 12, на которую опирается верхнее плечо предохранителя. В стенке корпуса со стороны малого зуба имеется отверстие 15 с приливом снаружи для размещения толстой цилиндрической части стержня валика подъемника, а со стороны большого зуба — отверстие 15 для тонкой цилиндрической части стержня. Рядом с этим отверстием находятся приливы 16, которые служат опорами для подъемника, а выше — шип 13 для навешивания замкодержателя.
На дне кармана корпуса имеются отверстия: 14 — для сигнального отростка замка, 17 — для направляющего зуба замка и 18 — для выпадания мусора, случайно попавшего в карман. Ребро 5 стенки 9 служит ограничителем ухода лапы замкодержателя внутрь корпуса. Внизу полости кармана, ограниченной стенкой 9 и ударной стенкой зева, имеется отверстие, которое пересекает нижнее ребро большого зуба. Через это отверстие извне воздействуют на замкодержатель для восстановления сцепления ошибочно расцепленных автосцепок. По всей высоте малого зуба проходит вертикальное отверстие 7, которое выполнено для уменьшения массы корпуса и улучшения технологии литья. Вдоль хвостовика на его горизонтальных станках с выходом в переходную зону расположены ребра 10 жесткости. Выпускаемые корпуса автосцепки имеют усиление переходной зоны, повышающее их предел выносливости.
Замок (рис. 6) своей замыкающей частью 5 запирает сцепленные автосцепки. Утолщение замыкающей части к наружной кромке препятствует выжиманию замка из зева внутрь кармана корпуса силами трения при перемещении сцепленных автосцепок друг относительно друга во время хода поезда. На цилиндрический шип 7 навешивается предохранитель. Через овальное отверстие 2 проходит валик подъемника. Замок опирается поверхностью 4 на наклонное дно кармана корпуса и перекатывается по нему во время сцепления или расцепления автосцепок, при этом направляющий зуб 3 препятствует перемещению опоры замка по дну кармана.
Рис
6 — Замок
На цветной картинке обозначение частей замка другое: 1 — замыкающая (тяжелая) часть; 2 — шип для навешивания предохранителя; 3 -овальное отверстие; 4- сигнальный отросток; 5 — лпорная цилиндрическая поверхность; 6 -зуб
Для передвижения замка внутрь кармана корпуса при расцеплении автосцепок служит прилив 5, имеющий прорезь 6 под нижнее плечо предохранителя По сигнальному отростку 1 судят о положении замка в автосцепке при ее наружном осмотре сбоку вагона Для лучшей видимости отросток окрашивают красной краской.
Замки прежних выпусков имеют сигнальный отросток, по форме соответствующий показанной штрихпунктирной линией, практика показала, что такие сигнальные отростки в месте перехода к корпусу замка отламывались вследствие вибрационных нагрузок
Замкодержатель (рис 7) вместе с предохранителем удерживает замок в нижнем положении при сцепленных автосцепках, а вместе с подъемником — в верхнем при расцепленных автосцепках до разведения вагонов
Рисунок 7 — Замкодержатель
Обозначения на цветном рисунке: 7 — лапа; 8 — расцепной угол; 9 — проивовес; 10 — овальное отверстие
Лапа 4 замкодержателя взаимодействует со смежной автосцепкой В собранном механизме лапа под действием противовеса 7 выходит в зев автосцепки Хвостовик 6 лапы служит как направляющая. На него воздействуют для восстановления сцепленного состояния у ошибочно расцепленных автосцепок. Овальное отверстие 3 в стенке 2 предназначено для навешивания на шип корпуса. Замкодержатель может не только поворачиваться на шипе, но и перемещаться в вертикальной плоскости Снизу под овальным отверстием расположен расцепной угол 5, взаимодействующий с подъемником замка.
Верхнее плечо 1 (рис 8) предохранителя в сцепленном состоянии перекрывается противовесом замкодержателя, что препятствует уходу замка внутрь кармана корпуса, а нижнее плечо 4, взаимодействуя с подъемником при расцеплении автосцепок, выводит верхнее плечо из зацепления с противовесом замкодержателя. Отверстие 2 служит для навешивания на шип замка. Фаска 5 на нижнем плече предохранителя облегчает проход нижнего плеча в паз замка при расцеплении автосцепок, а фаска у основания верхнего плеча и вокруг втулки 3 предназначена для того, чтобы предохранитель не задевал за шип для замкодержателя в корпусе и не препятствовал перемещению замка при боковых отклонениях предохранителя.
Рисунок 8 -Предохранитель
Обозначения на цветном рисунке:14 — нижнее плечо; 15- верхнее плечо; 16 — отверстие
Чтобы предупредить излом нижнего плеча от действия инерционной нагрузки, в нем предусматривают углубления 6, уменьшающие его массу. Предохранитель делают штампованным и литым. Литой вариант предохранителя изготавливается из стали, имеющей высокий предел выносливости.
Подъемник (рис. 9) удерживает вместе с замкодержателем замок в расцепленном положении до разведения вагонов и служит для подъема предохранителя и перемещения замка из зева внутрь кармана корпуса.
Рисунок 9 — Подъемник
Обозначения на цветном рисунке: 11 — квадратное отверстие; 12 — узкий палец; 13 — широкий палец
Широкий палец 1 поднимает предохранитель и уводит замок, а узкий палец 2 взаимодействует с расцепным углом замкодержателя. Отверстие 5 предназначено для квадратной части стержня валика подъемника. Буртик 4 препятствует западанию подъемника в овальное отверстие замка. Углубление 3 предусмотрено для опоры подъемника на прилив в кармане корпуса.
Валик подъемника (рис.10) предназначен для поворота подъемника замка при расцеплении автосцепок и ограничения выхода замка из кармана корпуса в зев собранной автосцепки.
Рисунок 10 — Валик подъемника
Обозначение на цветном рисунке: 17 — отверстие для цепочки; 18 — цилиндрическая часть; 19 — квадратная часть; 20 — балансир
Балансир 1, соединяемый с цепью расцепного привода, облегчает возвращение валика подъемника в исходное положение после разведения автосцепок и в других случаях. Стержень валика состоит из толстой 2, тонкой 4 цилиндрических и квадратной 3 частей. В собранной автосцепке цилиндрические части располагаются в соответствующих отверстиях корпуса, а квадратная часть находится в отверстии подъемника Толстая цилиндрическая часть удерживает замок от выпадания, имеющаяся на ней выемка 5 предназначена для запорного болта. Конические углубления 7 на балансире и 6 на торце стержня служат для центровки валика подъемника на станке при обработке поверхностей стержня во время ремонта.
studfiles.net
Автосцепка СА-3: назначение, характеристика, конструкция
Назначение
Ударно – тяговые приборы предназначены для сцепления вагонов между собой и с локомотивом, удержания их на определенном расстоянии друг от друга, восприятия, передачи и смягчения действия в поезде и при маневрах.
Современным ударно – тяговым прибором является автосцепное устройство, выполняющее основные функции ударных и тяговых приборов.
Краткая характеристика автосцепки СА-3
Парк подвижного состава железнодорожного транспорта характеризуется многообразием типов и конструкций вагонов, используемых в перевозочном процессе грузов и пассажиров. Условия эксплуатации вагонов связаны со значительными статическими и динамическими нагрузками, а в отдельных случаях — с воздействием высоких и низких температур перевозимого груза, повышенной влажности, агрессивных сред на конструкцию вагонов. При малой дальности перевозок значительно возрастает интенсивность ведения погрузочно-разгрузочных работ, как правило, с использованием различных средств механизации. Таким образом, многофункциональное и интенсивное использование вагонов железнодорожного транспорта требует их качественного технического обслуживания и ремонта квалифицированными специалистами.
Автосцепка СА-3 обеспечивает:
— автоматическое сцепление при соударении вагонов; автоматическое запирание замка у сцепленных автосцепок;
— расцепление подвижного состава без захода человека между вагонами и удержание механизма в расцепленном положении до разведения автосцепок;
— автоматическое возвращение механизма в положение готовности к сцеплению после разведения автосцепок; восстановление сцепления случайно расцепленных автосцепок, не разводя вагоны;
— производство маневровых работ (положение на «буфер»), когда при соударении автосцепки не должны соединяться. До сцепления автосцепки могут занимать различные взаимные положения:
— оси их находятся на одной прямой;
— оси могут быть смещены по вертикали или горизонтали.
Смещение осей по вертикали допускается в грузовом поезде до 100 мм и пассажирском скоростном до 50 мм, а в горизонтальном направлении до 175 мм, при которых обеспечивается надежное автоматическое сцепление вагонов в эксплуатации.
Значение автосцепки СА-3
Автосцепка СА-3 обеспечивает:
— автоматическое сцепление при соударении вагонов; автоматическое запирание замка у сцепленных автосцепок;
— расцепление подвижного состава без захода человека между вагонами и удержание механизма в расцепленном положении до разведения автосцепок;
— автоматическое возвращение механизма в положение готовности к сцеплению после разведения автосцепок; восстановление сцепления случайно расцепленных автосцепок, не разводя вагоны;
— производство маневровых работ (положение на «буфер»), когда при соударении автосцепки не должны соединяться.
Автосцепка са-3. конструкция
Автосцепка СА-3 (рис. 1) является тягово-ударной нежесткого типа. Она состоит из корпуса 4 и деталей механизма сцепления: замка 5, замкодержателя 2, предохранителя 3, подъемника 6, валика подъемника 7.
Рис 1 — Автосцепка СА-3
Головная часть автосцепки (голова) переходит в удлиненный пустотелый хвостовик, в котором имеется отверстие 1 для размещения клина, соединяющего автосцепку с тяговым хомутом. Голова автосцепки имеет большой 10 и малый 9 зубья. В пространство между малым и большим зубьями, в так называемый зев автосцепки, выступают замок 5 и замкодержатель 2, взаимодействующие в сцепленном состоянии со смежной автосцепкой.
Большой зуб имеет три усиливающих ребра: верхнее, среднее и нижнее, плавно переходящие в хвостовик и соединенные между собой перемычкой. Голова автосцепки заканчивается сзади упором 8. предназначенным для передачи при неблагоприятном сочетании допусков жесткого удара на хребтовую балку через концевую балку рамы вагона и ударную розетку.
Очертание в плане малого 7 (рис. 2) и большого 2 зубьев, а также выступающей в зев части замка 3 называетсяконтуром зацепления автосцепки.
Рис. 2. Стандартный контур зацепления автосцепки
Для обеспечения взаимосцепляемости всех автосцепок СА-3 контур зацепления должен соответствовать ГОСТ 21447—75. Линия I-I является продольной осью автосцепки. Внутренние стенки кармана корпуса, в котором находится механизм автосцепки, смещены относительно этой оси на 10°, а замыкающая поверхность замка расположена под углом 15°. Вследствие такого размещения механизма сцепления равномерно распределяется продольное усилие между замком, малым и большим зубьями. Ось II-II (ось зацепления) перпендикулярна оси I—I и проходит через точку О, называемую центром зацепления. По оси II-II обычно устанавливают расстояние автосцепки от концевой балки.
Корпус (рис.3), являющийся основной частью автосцепки, предназначен для передачи тяговых и ударных нагрузок, а также размещения деталей механизма сцепления. Хвостовик корпуса имеет постоянную высоту по длине. Его торец 1 — цилиндрический, что обеспечивает перемещение автосцепки в горизонтальной плоскости. Часть хвостовика, расположенная между отверстием 2 для клина тягового хомута и торцом, называется перемычкой.
Рис. 3 — Корпус автосцепки
Поверхности контура зацепления корпуса в сцепленном состоянии взаимодействуют со смежной автосцепкой: при сжатии усилие воспринимается ударной 6 и боковой 7 поверхностями малого зуба, ударной стенкой 5 зева и боковой поверхностью 4 большого зуба, а при растяжении — тяговыми поверхностями 8 малого и 3 большого зубьев. Тяговая, ударная и боковая поверхности малого зуба, а также тяговая поверхность большого зуба в средней части по высоте имеют вертикальную площадку длиной 160 мм (80 мм вверх и 80 мм вниз от продольной оси корпуса). Эти поверхности выше и ниже вертикальной площадки скошены для улучшения условий работы сцепленных автосцепок, когда между их продольными осями в вертикальной плоскости возникает угол (при прохождении горба сортировочной горки).
Корпуса автосцепок ранних выпусков имеют сбоку со стороны малого зуба прилив 10 (ухо), на который в период перехода с винтовой упряжки на автосцепку навешивали скобу винтовой упряжи смежного вагона во время маневровых работ, а также в передаточных поездах. После перевода подвижного состава на автосцепку новые корпуса сначала изготовлялись с приливом вместо уха, а затем без прилива с утолщением стенки малого зуба.
У выпускаемых корпусов автосцепок высота малого зуба увеличена и его нижняя кромка используется для приварки ограничителя вертикальных перемещений, необходимого для некоторых типов вагонов, поэтому кромка выполнена горизонтальной.
Рис. 4 — Корпус автосцепки: вид А
На корпусе со стороны малого зуба сделан прилив 9 с отверстиями для валика подъемника и запорного болта. В ударной стенке 5 зева имеются два окна: большое 11 для выхода в зев замка и малое 12 для выхода лапы замкодержателя.
Приливы и отверстия в кармане корпуса служат для размещения деталей механизма и правильного их взаимодействия.
Рисунок 5 -Внутренняя полость (карман) автосцкпки
Серповидный прилив (рис. 5) вверху на внутренней стенке малого зуба ограничивает перемещение замка внутрь кармана. Нижняя часть прилива переходит в полочку 12, на которую опирается верхнее плечо предохранителя. В стенке корпуса со стороны малого зуба имеется отверстие 15 с приливом снаружи для размещения толстой цилиндрической части стержня валика подъемника, а со стороны большого зуба — отверстие 15 для тонкой цилиндрической части стержня. Рядом с этим отверстием находятся приливы 16, которые служат опорами для подъемника, а выше — шип 13 для навешивания замкодержателя.
На дне кармана корпуса имеются отверстия: 14 — для сигнального отростка замка, 17 — для направляющего зуба замка и 18 — для выпадания мусора, случайно попавшего в карман. Ребро 5 стенки 9 служит ограничителем ухода лапы замкодержателя внутрь корпуса. Внизу полости кармана, ограниченной стенкой 9 и ударной стенкой зева, имеется отверстие, которое пересекает нижнее ребро большого зуба. Через это отверстие извне воздействуют на замкодержатель для восстановления сцепления ошибочно расцепленных автосцепок. По всей высоте малого зуба проходит вертикальное отверстие 7, которое выполнено для уменьшения массы корпуса и улучшения технологии литья. Вдоль хвостовика на его горизонтальных станках с выходом в переходную зону расположены ребра 10 жесткости. Выпускаемые корпуса автосцепки имеют усиление переходной зоны, повышающее их предел выносливости.
Замок (рис. 6) своей замыкающей частью 5 запирает сцепленные автосцепки. Утолщение замыкающей части к наружной кромке препятствует выжиманию замка из зева внутрь кармана корпуса силами трения при перемещении сцепленных автосцепок друг относительно друга во время хода поезда. На цилиндрический шип 7 навешивается предохранитель. Через овальное отверстие 2 проходит валик подъемника. Замок опирается поверхностью 4 на наклонное дно кармана корпуса и перекатывается по нему во время сцепления или расцепления автосцепок, при этом направляющий зуб 3 препятствует перемещению опоры замка по дну кармана.
Рис 6 — Замок
На цветной картинке обозначение частей замка другое: 1 — замыкающая (тяжелая) часть; 2 — шип для навешивания предохранителя; 3 -овальное отверстие; 4- сигнальный отросток; 5 — лпорная цилиндрическая поверхность; 6 -зуб
Для передвижения замка внутрь кармана корпуса при расцеплении автосцепок служит прилив 5, имеющий прорезь 6 под нижнее плечо предохранителя По сигнальному отростку 1 судят о положении замка в автосцепке при ее наружном осмотре сбоку вагона Для лучшей видимости отросток окрашивают красной краской.
Замки прежних выпусков имеют сигнальный отросток, по форме соответствующий показанной штрихпунктирной линией, практика показала, что такие сигнальные отростки в месте перехода к корпусу замка отламывались вследствие вибрационных нагрузок
Замкодержатель (рис 7) вместе с предохранителем удерживает замок в нижнем положении при сцепленных автосцепках, а вместе с подъемником — в верхнем при расцепленных автосцепках до разведения вагонов
Рисунок 7 — Замкодержатель
Обозначения на цветном рисунке: 7 — лапа; 8 — расцепной угол; 9 — проивовес; 10 — овальное отверстие
Лапа 4 замкодержателя взаимодействует со смежной автосцепкой В собранном механизме лапа под действием противовеса 7 выходит в зев автосцепки Хвостовик 6 лапы служит как направляющая. На него воздействуют для восстановления сцепленного состояния у ошибочно расцепленных автосцепок. Овальное отверстие 3 в стенке 2 предназначено для навешивания на шип корпуса. Замкодержатель может не только поворачиваться на шипе, но и перемещаться в вертикальной плоскости Снизу под овальным отверстием расположен расцепной угол 5, взаимодействующий с подъемником замка.
Верхнее плечо 1 (рис 8) предохранителя в сцепленном состоянии перекрывается противовесом замкодержателя, что препятствует уходу замка внутрь кармана корпуса, а нижнее плечо 4, взаимодействуя с подъемником при расцеплении автосцепок, выводит верхнее плечо из зацепления с противовесом замкодержателя. Отверстие 2 служит для навешивания на шип замка. Фаска 5 на нижнем плече предохранителя облегчает проход нижнего плеча в паз замка при расцеплении автосцепок, а фаска у основания верхнего плеча и вокруг втулки 3 предназначена для того, чтобы предохранитель не задевал за шип для замкодержателя в корпусе и не препятствовал перемещению замка при боковых отклонениях предохранителя.
Рисунок 8 -Предохранитель
Обозначения на цветном рисунке:14 — нижнее плечо; 15- верхнее плечо; 16 — отверстие
Чтобы предупредить излом нижнего плеча от действия инерционной нагрузки, в нем предусматривают углубления 6, уменьшающие его массу. Предохранитель делают штампованным и литым. Литой вариант предохранителя изготавливается из стали, имеющей высокий предел выносливости.
Подъемник (рис. 9) удерживает вместе с замкодержателем замок в расцепленном положении до разведения вагонов и служит для подъема предохранителя и перемещения замка из зева внутрь кармана корпуса.
Рисунок 9 — Подъемник
Обозначения на цветном рисунке: 11 — квадратное отверстие; 12 — узкий палец; 13 — широкий палец
Широкий палец 1 поднимает предохранитель и уводит замок, а узкий палец 2 взаимодействует с расцепным углом замкодержателя. Отверстие 5 предназначено для квадратной части стержня валика подъемника. Буртик 4 препятствует западанию подъемника в овальное отверстие замка. Углубление 3 предусмотрено для опоры подъемника на прилив в кармане корпуса.
Валик подъемника (рис.10) предназначен для поворота подъемника замка при расцеплении автосцепок и ограничения выхода замка из кармана корпуса в зев собранной автосцепки.
Рисунок 10 — Валик подъемника
Обозначение на цветном рисунке: 17 — отверстие для цепочки; 18 — цилиндрическая часть; 19 — квадратная часть; 20 — балансир
Балансир 1, соединяемый с цепью расцепного привода, облегчает возвращение валика подъемника в исходное положение после разведения автосцепок и в других случаях. Стержень валика состоит из толстой 2, тонкой 4 цилиндрических и квадратной 3 частей. В собранной автосцепке цилиндрические части располагаются в соответствующих отверстиях корпуса, а квадратная часть находится в отверстии подъемника Толстая цилиндрическая часть удерживает замок от выпадания, имеющаяся на ней выемка 5 предназначена для запорного болта. Конические углубления 7 на балансире и 6 на торце стержня служат для центровки валика подъемника на станке при обработке поверхностей стержня во время ремонта.
www.trportal.ru
Автосцепка — Энциклопедия нашего транспорта
Автосцепка — разновидность ударно-тяговых приборов, устройство для автоматического сцепления железнодорожного подвижного состава, передачи и смягчения действия продольных усилий, развиваемых при движении и остановке поезда, а также при маневровой работе. Обеспечивает автоматическое сцепление подвижного состава при соударении, автоматическое возвращение деталей механизма в положение готовности к сцеплению после разведения подвижного состава и возможность работы «на буфер», когда при соударении автосцепок их сцепления не требуется. Расцепление производится вручную (при этом человек не заходит между вагонами).
Классификация автосцепок
Все существующие автосцепки могут быть разделены по их типу на две группы: нежёсткие и жёсткие и по принципу восприятия усилий также на две группы: тягово-ударные и тяговые.
- Нежёсткой называется автосцепка, которая допускает перемещение в вертикальном направлении её корпуса относительно корпуса смежной автосцепки в сцепленном состоянии.
- Жёсткой называется автосцепка, у которой продольная ось корпуса в сцепленном состоянии находиться на одной прямой с осью корпуса смежной автосцепки, при этом исключается возможность взаимного перемещения корпусов автосцепок.
- Тягово-ударной называется автосцепка, служащая для передачи растягивающих и сжимающих усилий между единицами подвижного состава.
- Тяговой называется автосцепка, которая воспринимает только растягивающие усилия между единицами подвижного состава, а сжимающая воспринимается отдельными приборами (буферами).
На железных дорогах СНГ применяются тягово-ударные сцепки нежёсткого типа. В вагонах метрополитена применяется тягово-ударная сцепка жёсткого типа.
Автосцепка СА-3
Описание
Применяется сейчас на всех магистральных железных дорогах СНГ, в Финляндии и Монголии, а также на нескольких отдельных линиях в других государствах. По краям вагона или локомотива имеется два буфера, а посередине располагается автосцепка. Автосцепка вагона состоит из следующих частей: корпуса автосцепки и расположенного в нём механизма, тягового устройства с поглощающим аппаратом (пружинами), расцепного привода и ударно-центрирующего прибора. Корпус автосцепки представляет собой пустотелую стальную отливку, в головной части которой размещаются детали механизма. Если смотреть на автосцепку спереди, то у неё справа расположен большой зуб, слева — малый. Пустота между зубьями называется зевом автосцепки. Слева из зева выступает замок, в середине выходит лапа замкодержателя.
Автосцепка СА-3На рисунке показана автосцепка и её расположение на вагоне. В корпусе автосцепки 13 размещаются детали механизма сцепления. Тяговый хомут 6 с помощью клина 8, закрепленного болтами, упорной плиты 7, переднего 9 и заднего 1 упоров передаёт через поглощающий аппарат 5 продольные растягивающие и сжимающие усилия от корпуса автосцепки на раму вагона. Маятниковые подвески 11 и центрирующая балка 12 возвращают в центральное положение отклоненный корпус автосцепки. Расцепной рычаг 3, удерживаемый кронштейном 2 и державкой 10, и цепь 14 предназначены для расцепления автосцепки и установки механизма в выключенное положение при необходимости работы «на буфер»; поддерживающая планка 4 служит для удержания тягового хомута с поглощающим аппаратом и упорной плитой. Корпус сцепки имеет два зуба — большой и малый, между которыми образован зев. При сцеплении малый зуб одной сцепки входит в зев другой, а расположенные в корпусе автосцепки замки нажимают один на другой и входят в карманы корпусов 13, обеспечивая сцепление. В сцепленном состоянии замкодержатель препятствует саморасцеплению автосцепки в пути под влиянием ударов и толчков. Для расцепления автосцепки необходимо поворотом валика подъёмника любой из сцепок сначала отпереть соответствующий замкодержатель, а затем отвести замок назад. В положение готовности к новому сцеплению замки приводятся при выводе малого зуба из зева или без разведения автосцепки (при ошибочном расцеплении) — поднятием замкодержателя. Действует автосцепка следующим образом. При нажатии или соударении вагонов головы автосцепок скользят одна по другой в горизонтальной плоскости до тех пор, пока малый зуб одной не войдёт в зев другой. При нажатии друг на друга замки сначала уходят каждый в свой карман, а затем выпадают в образовавшееся пространство и запирают автосцепки. Чтобы расцепить автосцепки, достаточно убрать один из замков внутрь головы автосцепки. Для этого при помощи расцепного привода поворачивается валик подъёмника, а вместе с ним и подъёмник замка, который сначала поднимает верхнее плечо собачки, чем выключает действие предохранителя замка, затем уводит замок внутрь головы автосцепки и одновременно заходит за расцепной угол замкодержателя. Проследним движением подъёмник замка запирает свой обратный ход, так как, упираясь в расцепной угол замкодержателя, он не может вернуться в своё прежнее положение до тех пор, пока не освободиться лапа замкодержателя, что произойдёт только при разъединении автосцепок. При этом она под действием веса своего противовеса и нажатия подъёмника войдёт в зев автосцепки. В пассажирских вагонах устраиваются, помимо поглощающих аппаратов автосцепки, центральные упругие площадки (переходы). Упругая площадка, размещаемая на торцовой стенке вагона, имеет рамку, выступающую вперёд за плоскость зацепления автосцепок. Нижняя часть рамки соединяется штырями с буферами, а верхняя с хомутом листовой рессоры, концы которой при помощи шарниров опираются на торцовую стенку вагона. При соединении вагонов сначала сжимаются упругие площадки, после чего уже сцепляются автосцепки, в результате этого автосцепки находятся в натянутом положении, что смягчает толчки, вызываемые зазорами между сцепляемыми поверхностями автосцепок. Сбоку и сверху переходы закрываются резиновым суфле.
История
У нас впервые вопрос о внедрении автосцепки на отечественных железных дорогах всерьёз обсуждался в 1898 году, на ХХ совещательном съезде представителей железных дорог. Как один из вариантов рассматривалась и американская автосцепка системы Джанея. В начале XX века на нескольких вагонах были испытаны сцепки американского типа. Однако, из-за её недостатков и отсутствия подходящей отечественной конструкции введение автосцепки было решено отложить на неопределённый срок.
Применяемая на отечественных железных дорогах автосцепка СА-3 сконструирована в 1932 году коллективом авторов в составе А. Ф. Пухова, И. Н. Новикова, В. А. Шашкова, В. Г. Голованова под руководством В. Ф. Егорченко. За основу была взята автосцепка Виллисона, изобретенная в 1916 году и предназначенная для подвижного состава шахт и рудников. Авторы полностью переработали автосцепку, а главное, применили новый контур зацепления. Получилась очень удачная конструкция. На западе ее называют «русская автосцепка» или «автосцепка Виллисона с русским контуром». Перевод железных дорог СССР на автосцепку начался в 1935 году, и был полностью завершён в 1957 году. Во время перехода с винтовой стяжки на автосцепку на отечественных железных дорогах применялись специальные переходные приспособления.
Модификации
Патент, выданный Виллисону: http://www.google.com/patents/US1201665
Конструкция большинства элементов сцепки неоднократно подвергалась изменениям для улучшения эксплуатационных характеристик.
Для паровозов и путевой техники выпускаются модификации автосцепки, не имеющие поглощающего аппарата. Сцепки локомотивов и части вагонов имеют возможность установки предохранительного крюка, удерживающего головку автосцепки в случае обрыва на исправной сцепке. Для восьмиосных вагонов разработана усиленная сцепка СА-3М, допускающая бОльшие отклонения головки.
С 1950-х гг. для внедрения на дорогах Европы предлагаются различные модификации СА-3, обеспечивающие соединение электрических цепей и пневматических магистралей.
По тому же принципу зацепления Виллисона, но с другими геометрическими размерами, существуют сцепки для узкоколейных дорог и горной техники.
Например, сейчас производится автосцепка А-7 для шахтных вагонеток, позволяющая:
- Автоматическое сцепление, быстрое и безопасное расцепление вагонеток при формировании составов.
- Разгрузку вагонеток в круговом опрокидывателе без расцепления состава.
- Надежное сцепление и расцепление вагонеток на закруглениях рельсовых путей радиусом не менее 10 мм.
- Прохождение вагонеток на закруглениях рельсовых путей радиусом не менее 6 м.
- Прохождение вагонеток на превышениях рельсовых путей до 50 мм.
- Прохождение сцепленных вагонеток на переломах рельсовых путей в вертикальной плоскости без радиуса сопряжения путей 200 а при радиусе сопряжения путей 20 м более 200
- Автосцепка одновременно выполняет роль буфера.
- Тяговое рабочее усилие автосцепкой 7000 кг.
- Автосцепка не может сцепляться с вагонетками оборудованными не автоматическими сцепками.
- Для сцепления вагонеток оборудованных автосцепками модели А-7 с электровозами, последние должны оборудоваться переходными автосцепками.
[1]
Для узкой колеи выпускалась автосцепка АУК, предложенная Медведевым.
Автосцепки узкой колеиNarrow gauge automatic coupling
Автосцепка Джаннея
Из ныне существующих первая автосцепка была изобретена в США Эли Джаннеем и запатентована 29 апреля 1873 года. В 1892 году Конгресс принял законопроект, которым все ЖД США должны были ввести автосцепку Джаннея в обязательном порядке. Но в таком виде автосцепка просуществовала недолго. В 1887 году Master Car Builders Association существенно изменила контур зацепления. В дальнейшем контур зацепления изменялся, с сохранением совместимости, в 1904, 1916 (принят тип «D»), 1918, 1930 (принят тип «E). Сейчас на ЖД США применяется автосцепка Дженнея стандарта Association of American Railroads типов «F» и «H», принятые в 1946 и 1954 годах. Чтобы она нормально работала, необходимо предварительно разблокировать когти, поэтому эту сцепку и прозвали полуавтоматической. Основные недостатки сцепки Джаннея — это износ валика, недостаточное использование поверхности корпуса для передачи усилий, невозможность работы с вагонами с винтовой упряжью, а в ранних образцах — ненадежность работы.
Разновидностью является сцепка Tightlock, обеспечивающая вертикальную взаимную неподвижность сцепок и соединение пневматических магистралей.
Автосцепка Шарфенберга
Автосцепка Шарфенберга в расцепленном состоянии Карл ШарфенбергНемецкий инженер-железнодорожник Карл Вильгельм Генрих Фридрих Шарфенберг (родился 3 марта 1874 в Висмаре; умер 5 января 1938 в Готе) запатентовал свою автосцепку жесткого типа 18 марта 1903. образцы его автосцепки были изготовлены в 1909 в Кенигсберге. После долгой доводки опытных образцов в 1921 году Шарфенберг открывает в Берлине свою фирму. В 1926 году он получает крупный заказ на оснащение своей автосцепкой вагонов.
У нас в стране автосцепка Шарфенберга используется на вагонах метрополитена, некоторых трамвайных вагонах и части скоростных поездов. Сцепка полностью автоматическая.
За рубежом создано значительное количество разновидностей сцепки Шарфенберга, отличющихся размерами, формой отдельных частей и расположением электрических и пневматических соединителей. Зачастую вагоны с разными модификациями сцепки оказываются не совместимы между собой. Одним из крупнейших производителей модифакаций сцепки Шарфеньерга является компания Dellner, иногда её сцепки выделяют в отдельный подтип.
Автосцепка Томлинсона
Аммериканским инженером Томлинсоном предложено несколько конструкций автоматических сцепок, обеспечивающих соединение магистралей.
Применяются, в частности, на МВПС в Японии, например Токийским метрополитеном.
http://ja.wikipedia.org/wiki/%E3%83%95%E3%82%A1%E3%82%A4%E3%83%AB:Tomlinso.jpg
Автосцепка Шибаты
Применяется в Японии для МВПС.
http://ja.wikipedia.org/wiki/%E3%83%95%E3%82%A1%E3%82%A4%E3%83%AB:%E6%96%B0%E5%B9%B9%E7%B7%9A%E7%94%A8%E9%80%A3%E7%B5%90%E5%99%A8.jpg
Близкий вариант сцепки используется на скоростных поездах Синкансен:
http://ja.wikipedia.org/wiki/%E3%83%95%E3%82%A1%E3%82%A4%E3%83%AB:%E6%96%B0%E5%B9%B9%E7%B7%9A%E7%94%A8%E9%80%A3%E7%B5%90%E5%99%A8.jpg
Автосцепка Wedgelock
Применяется в Лондонском метрополитене.
http://en.wikipedia.org/wiki/File:London_Underground_1996ts.jpg
Другие системы
Существует также ряд имеющих более узкое применение других конструкций автоматических сцепок.
- Сцепка ABC (Automatic Buffing Contact)
— Современные конструкции http://laf-lloyd.com/en/prod/attelages/lloyd.htm
— История http://www.historywebsite.co.uk/Museum/Transport/Trains/ABC/ABC01.htm
- Сцепки трамвайных вагонов, например сцепка УКВЗ
Ссылки
См. также:
Источники:
- А. С. Бакулин «Сооружения, устройства, подвижной состав метрополитена» М., Транспорт, 1979.
- Большая Советская энциклопедия
- en.wikipedia.org
wiki.nashtransport.ru
Автосцепное устройство четырехосных вагонов
Оглавление |
---|
Автосцепное устройство четырехосных вагонов |
Отливка автосцепки |
Страница 1 из 2
Автосцепное устройство типа СА-3 грузовых вагонов размещается в консольной части хребтовой балки рамы кузова.
Основные части автосцепного устройства:
— корпус автосцепки с деталями механизма,
— ударно-центрирующий прибор,
— упряжное устройство,
— упоры и расцепной привод.
Корпус автосцепки 13 с механизмом предназначен для сцепления и расцепления вагонов, восприятия и передачи ударно-тяговых усилий упряжному устройству.
Корпус установлен в окно ударной розетки 9 и своим хвостовиком соединен при помощи клина 8 с тяговым хомутом 6.
Корпус автосцепки представляет собой пустотелую фасонную отливку, состоящую из головной части и хвостовика.
Внутри головной части размещены детали механизма автосцепки.
Она имеет большой 1 и малый 4 зубья, которые, соединяясь, образуют зев.
Торцовые поверхности малого зуба и зева воспринимают сжимающие усилия, а тяговые усилия передаются задними поверхностями большого и малого зубьев, та вертикальной стенке зева возле малого зуба имеется окно для замка 3, а рядом — окно для замкодер-жателя 2.
В верхней части головы отлит выступ 5, который воспринимает жесткий удар при полном сжатии поглощающего аппарата и передает его через розетку на раму вагона.
Со стороны малого зуба внутри головы отлита полочка для верхнего плеча предохранителя замка от саморасцепа, а со стороны большого зуба имеется шип для навешивания замкодержателя.
В нижней части головы выполнены отверстия для выступов замка автосцепки и горизонтальное отверстие для постановки валика подъемника. В пустотелом хвостовике сделано продолговатое отверстие 6 для клина, соединяющего корпус с тяговым хомутом.
Торец хвостовика 7 служит для передачи ударных нагрузок и имеет цилиндрическую поверхность, обеспечивающую горизонтальные повороты автосцепки.
Горизонтальная проекция зубьев, зева и выступающей части замка называется контуром зацепления.
Центрирующий прибор воспринимает от корпуса автосцепки избыточную энергию удара после полного сжатия поглощающего аппарата и центрирует корпус автосцепки.
Прибор имеет ударную розетку 9, две маятниковые подвески 11 и центрирующую балочку 12.
Ударная розетка 9 отлита заодно целое с передним упором и приклепана или приварена к концевой балке рамы. У розетки есть окно для постановки корпуса автосцепки и отверстия для маятниковых подвесок, а также ребра жесткости в верхней ударной части.
Центрирующая балочка 12 омегообразной формы с двумя плоскостями и двумя ограничителями (продольными и боковыми). При установке балочки на место продольный ограничитель захватывает нижнюю вертикальную стенку ударной розетки. Боковые ограничители удерживают корпус автосцепки при максимальных отклонениях в поперечном направлении.
Маятниковые подвески 11 имеют вид стержня диаметром 25 мм с двумя головками (верхней более широкой и нижней). Верхними головками подвески опираются на ударную розетку, а на нижние уложена центрирующая балочка.
Упоры автосцепки задние 1 и передние 9 служат для передачи растягивающих и сжимающих усилий на раму и кузов вагона. Передний упор совместно с розеткой представляет собой П-образную коробку с ребрами жесткости.
На расстоянии 625 мм от упорных плоскостей переднего упора к хребтовой балке приклепан или приварен задний упор 1, который также представляет собой П-образную отливку с ребрами жесткости.
У четырехосных вагонов с укороченными консольными частями (крытые вагоны и цистерны) задние упоры отливают заодно целое с надпятниковыми коробками. Для предупреждения истирания вертикальных стенок хребтовой балки поглощающим аппаратом на них между упорами приклепывают по две предохранительные планки.
Упряжное устройство передает упорам продольные силы от корпуса автосцепки и смягчает их действие. Оно размещено между передними и задними упорами автосцепного устройства и состоит из тягового хомута 6, поглощающего аппарата 5, клина 8, упорной плиты 7 и крепежных деталей клина и поддерживающей планки.
Нижней опорой тягового хомута и поглощающего аппарата является поддерживающая планка 4, прикрепляемая восемью болтами снизу к хребтовой балке. Тяговый хомут 6 представляет собой раму, внутри которой размещен поглощающий аппарат и упорная плита.
В головной части хомута имеется отверстие для клина. Внизу головной нижней части расположены приливы с отверстиями для болтов, предохраняющих клин от выпадания.
Опорная площадка хомута снабжена усиливающими ребрами. Клин тягового хомута прямоугольного сечения с округленными кромками в нижней части имеет заплечики, которыми он опирается на болты, удерживающие его от выжимания. Выемки в верхней части боковых поверхностей клина сделаны для уменьшения его массы.
Расцепной привод служит для расцепления автосцепок.
Привод представляет собой двуплечий рычаг 3, удерживаемый кронштейном 2 с полочкой и державкой 10. Цепь 14 соединяет короткое плечо рычага с валиком подъемника 15.
www.aswn.ru
Автосцепка СА-3
«Автосцепка СА-3» является автоматическим сцепным устройством. Её основное предназначение заключается в проведении автоматического сцепления вагонов, в момент, когда срабатывает «автосцепка СА-3», личного участия какого-либо специалиста не требуется. Весь процесс сцепления происходит моментально при соединении составляющих подвижного состава. Первое упоминание о подобной операции появилось в конце девятнадцатого века, в 1898 году. За решение подобной проблемы взялись специалисты высокого ранга. С российской стороны отправились на двадцатый совещательный съезд представители от национальных железных дорог.
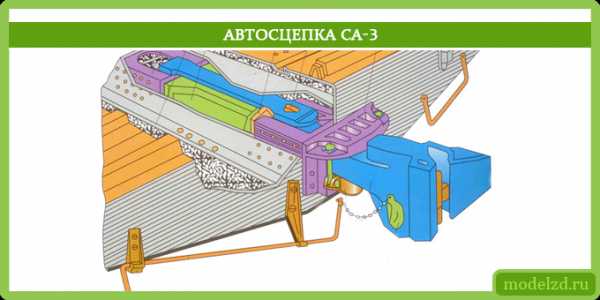
Один из предложенных вариантов предусматривал применение автосцепки американского производства. Автором рекомендуемого оборудования был американец Эли Джанней, родился 12.11.1831 года в небольшом городке Александрия, находящегося на территории штата Виргиния. Свою учёбу начинал в семинарии. Принимал участие в боевых действиях в период Гражданской войны, дослужился до чина майора. В возрасте сорока трёх лет, апрельским утром 1873 года Джаннею вручили американский патент за номером «138,405», за ту самую, вроде, как улучшенную вагонную сцепку. Необходимо отметить, ради исторической справедливости, что принцип данного изобретённого оборудования Эли Джаннеем, служит по сей день на всех железных дорогах большинства стран мира.
Однако, тогда на совещательном форуме изобретение было подвергнуто критике, так как была отмечена ненадёжность работы данной сцепки. В Российской империи на тот момент вообще отсутствовала какая-либо подходящая отечественного производства автосцепка. Участники двадцатого съезда тогда отказались принимать конкретное решение по изобретению. Его внедрение на поездные составы отложили не несколько лет, не оговаривая никакой даты.
Зато изобретатель Willison, Виллисон создает автосцепку, и в 1916 году ее ставят на вагоны железных дорог многих мировых держав, Россия в этом случае не была исключением. Данное оборудование представляло собой двузубый контурный корпус автосцепки, в котором и происходило само зацепление. Европейцы изначально обкатывали эту автоматическую сцепку на рудниках и шахтах. Кстати, именно, советская «автосцепка СА-3», появившееся на железных дорогах Советского Союза, создавалась на основе конструкции Виллисона.
В последующие годы её стали применять на территории Советского союза. Начинал внедрять данное оборудование коллектив ЛЗР в далёком 1932 году. Руководителем работ стал конструктор В.Ф Егорченко, инженерная группа была представлена В.Г. Головановой, В.А Шашковой, И Н. Новиковой и А.Ф Пуховой. Вот уж поистине самым прочным сцеплением оказалось изделие женского производства. Создатели кропотливо, как может это делать только женщина, в полном объёме переработали старую конструкцию корпуса автоматического сцепления. В итоге проводимой работы, авторами был создан совершенно новый вид контурной основы самого сцепления. Международные специалисты железной дороги повсеместно в то время отмечали новизну и оригинальность работы созданного автоматического сцепления «СА-3». В мировой инженерной среде этому оборудованию дали имя, назвав «Автосцепкой Виллисона с наличием русского контура» или коротко «Русской автосцепкой».
После признания данного изобретения международным сообществом «автосцепка СА-3» стала закупаться такими странами, как Норвегия, Швеция, применяя её на железнодорожных рудниковых путях «Мальмбанан» для электровозов «IORE». Не отставали в приобретении столь необходимого оборудования такие страны, как Ирак, Иран, Финляндия. В этих государствах изделие «СА-3», приняли с совмещением буферов и винтовой стяжки. Для своего подвижного состава Монголия тоже приобрела сцепку «СА 3». Многие любопытствующие долго ломали голову над такой короткой аббревиатурой описываемой продукции, чтобы это могло означать? Но оказалось, что и здесь тоже всё просто, но со вкусом и гордостью за свою страну, авторы назвали изделие «Советской автосцепкой», а цифра «три» означала, тем самым информируя покупателя и эксплуатационников, что это третий вариант разработки, относящийся к ударно-тяговому, нежесткому типу.
Описываемое изделие «СА 3» имеет следующие составные части: в первую очередь – это сам корпус автосцепки, в котором расположен механизм, представляющий собой тяговое устройство с установлением поглощающего аппарата, то есть пружин. В данной описываемой конструкции есть также ударно-центрующий прибор и расцепной привод автосцепки. Сама корпусная часть изготовлена в виде пустотелой стальной отливки, её головная часть предназначена для размещения названных механических деталей. Смотрим на сцепное устройство, как на фасад здания, тогда с левой стороны будет виден зуб малого размера, а с правой стороны окажется зуб большего размера. Между двух зубов находится пустотелость – это и есть зев автосцепа. С левой стороны от зева находится замок, имеющий несколько выступающую форму. Со срединной части самого устройства выдвинута лапа замкового держателя.
На всех железных дорогах Советского Союза с севера на юг и с запада на восток в 1935 году началась замена старого сцепного устройства на новое «СА-3». Начавшаяся война в 1941 году внесла свои коррективы в данное техническое переоснащение. В итоге, данный процесс смогли осуществить только в 1957 году, то есть минуло немного и немало, а целых двадцать два года. Именно таким временным отрезком вынужден был расплатится весь советский народ. В этот переходной период времени для правильного осуществления такого большого переоборудования всего подвижного состава началось применение специального переходного приспособления, оно носило название «двухзвенной цепи».
Изготовление предложенного варианта изделия состояло из двух цепных звеньев и е уголка, который устанавливался непосредственно в зев автоматического сцепа, находящегося между малым и большим зубьями. На вагонный крюк старого винтового сцепа набрасывалось крайнее цепное звено.
Такое отечественное вынужденное «ноу-хау», то бишь уникальное по своей простоте изделие из двух цепных звеньев позволяло производить сцепление всех вагонов в единый поездной состав, как со старым винтовым сцепом, так и с новой сцепкой «СА-3». В процессе применения таких деталей, специалисты пришли к выводу, что винтовую сцепку можно напрямую соединить с новым изделием. Для этого требовалось наличие на корпусной части «автоматической сцепки» установить, так называемое в народе, «ухо» или крюк. Изначально описываемый вариант применяли только на станционных пунктах при производстве манёвровых работ.
Упрощённый второй вариант сцепления вагонов со старым и новым оборудованием, позволял станционному сцепщику соединять электрический кабель и тормозной рукав, на каждом вагоне. Таким образом потомки русского Кулибина добились того, что такая сцепка стала выдерживать большую нагрузку, показатель разрывного статического усилия стал равен двумстам тоннам.
В последующие годы «автоматическая сцепка СА-3» неоднократно усовершенствовалась, приобретая новые лучшие характеристики. К примеру, на приваренных кронштейнах, которые были установлены на железнодорожные цистерны, стали производить трафаретную маркировку в виде красных стрелок, что сразу бросалось в глаза при проведении проверок оборудования.
С наступлением двухтысячного года Российские железные дороги вновь усовершенствуют «автосцепку СА-3». В случаях, когда, происходит обрыв автосцепа, её корпусная часть может выскользнуть из полости зева, тем самым прекратив работу сцепного изделия.
Мало того, сам корпус падает на рельсошпальную решётку. Как правило, в этом случае может произойти повреждение другого оборудования железной дороги. Достаточно констатировать факт выхода из строя стрелочного перевода. Попадание корпуса сцепки на рельсовую головку, даст возможность произойти самому страшному крушению состава, с человеческими жертвами или с последствиями экологической катастрофы. Поэтому переоборудование начали с нефтяных цистерн.
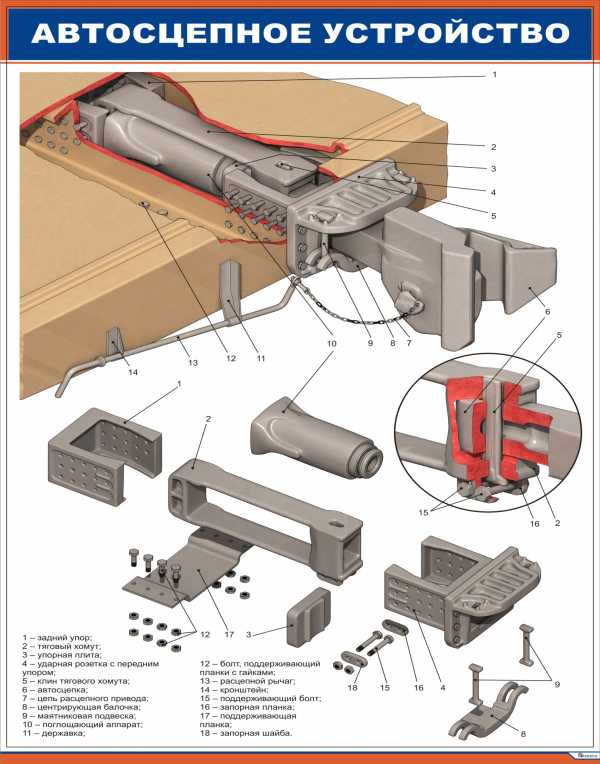
При данном процессе необходимо было к корпусной части, к её нижней и верхней поверхностям приварить два кронштейна, которые препятствовали бы процессу выскальзывания, соответственно, исключали само падение оборванного автосцепа на шпалы.
Подготовительные ремонтные работы сцепных устройств, непосредственная их проверка начинается на территории депо. Такими видами работ занимаются специализированные ремонтные отделения. На ведение подобных работ у предприятия должно быть специальное разрешительное удостоверение, которое выдаётся только в российском департаменте МПС. Вся размещённая технологическая оснастка предприятия должна была обеспечить проведение означенного ремонта. При этом обязательно соблюдать правила промышленной санитарии и технику безопасности.
Для проведения процедуры полного осмотра каждой детали сцепного оборудования и съёмных узлов, производится их снятие с вагонов подвижного состава. После чего, они отправляются на одно из вышеперечисленных ремонтных отделений. Все несъёмные детали, к которым можно отнести расцепной привод, задние и передние упоры ударную розетку, подлежат проверке на своём штатном месте. Исключение может иметь место, если специалисты потребуют произвести демонтаж означенных узлов.
Все детали, подлежащие очередному освидетельствованию, зачищаются, имеющаяся на них грязь должна быть тоже снята. Только после такой подготовительной процедуры, детали проходят неразрушающий контроль. Оборудование, узлы, которым требуется сварка, подвергаются проверке только после проведения сварочных работ.
Любая «автосцепка СА-3» разбирается в определённой последовательности. Первоначально происходит разъединение цепи, установленной на расцепном приводе. После чего вытаскивается болт, являющийся запорным. Через корпусное отверстие, находящееся на стенке, достаётся валик, стоящий на подъёмнике. После этого из корпусной части изымается предохранитель вместе с замком. Последняя процедура проводится по съёмке самого подъёмника, закреплённого на опоре корпусной стенки. Отступление от этой последовательности недопустимо.
Процедура деповского ремонта подвижного состава требует разборку только неисправных поглощающих аппаратов. Процедура проведения капитального ремонта требует разборку всех аппаратов.
Только с помощью правки ремонтируется уширение зева и изгибы сцепки.
Для этого необходимо первоначально произвести на корпусе разметку, тем самым определи изгибную величину корпуса.
Процедура начинается с обозначения хвостовой середины, чтобы расстояние от упора было равно двадцати миллиметрам. Такие же манипуляции делаются на торцевой и средней частях. Таким образом, изгиб является отклонением в срединной части хвостовика от размеченной линии. Наличие изгиба с размером больше трёх миллиметров в горизонтальной и вертикальной плоскостях, подлежат обязательной процедуре правки.
Для того, чтобы прогреть равномерно корпусную часть температура доводится до восьмисот градусов по Цельсию, только после этого приступают к правке. Выдержка в печи должна быть менее одного часа. Когда процедура правки будет подходить к окончанию, то выправляемые зоны должны быть уже со сниженной температурой. В идеале – это шестьсот градусов по Цельсию. Выполнение данных требований, позволит избежать возможного появления трещин термического происхождения. Подобная описанная правка осуществляется только на специализированном гидравлическом прессе. При проведении процедуры по устранению уширения зева в корпусной части изделия, необходимо установить ограничитель, который исключить процесс возможного сужения зева больше указанной нормативной величины.
Когда придёт пора охлаждать корпус, то прежде всего, необходимо избежать возможного появления каких-либо сквозняков. Никогда не применять водное охлаждение или иную среду, позволяющую производить охлаждение. Ремонт площадей износа и появившихся трещин производят с помощью наплавки или сварки.
С различными вариантами допусков и каталогом деталей при проведении сварочных операций можно ознакомится в разрешительной документации, где всё детально расписано.
Процедура сборочного этапа тоже подробно расписана, в которой последовательность проводимых операций начинается с монтажа подъёмника. Он укладывается с помощью широкого пальца на опорную площадь, находящуюся на корпусной стенке, на стороне, где находится большой зуб. После чего навешивается замковый держатель непосредственно на шиповую часть уже упомянутой корпусной стенки.
Затем происходит установка предохранителя и замка во внутреннюю корпусную часть изделия. Нельзя пропустить такую деталь процесса, как подъём нижнего предохранительного плеча, задействовав, при этом, металлический крючок. Только в таком варианте осуществляется проход верней части плеча над полкой с той стороны, где находится малый зуб. В стенное отверстие корпусной части пропускается валик, относящийся к деталям подъёмника. Таким образом, с помощью квадратного отверстия на подъёмнике и овального замкового выреза происходит фиксация упомянутых деталей, не допуская их выпадения.
Закрепление механизма и соединение цепи, относящейся к расцепному приводу, с имеющимся отверстием в балансире валика, установленного на подъёмнике, происходит по окончанию процедуры вставки запорного болта.
Когда автоматическая сцепка правильно собрана, а в зев вошли и замковая часть, и ударная поверхность лап замкового держателя. Такое расположение деталей оборудования свидетельствует о готовности самого механизма к производству автоматического сцепления.
Когда прилагается усилие со стороны рукоятки рычага расцепки или со стороны зева, то замковая часть от такого воздействия перемещается во внутреннюю часть механизма. Когда усилие снимается, то происходит возвратное перемещение в изначальную позицию.
Полное утопление замка в корпусную часть, когда там уже находится лапа замкового держателя никогда не произойдёт.
После того весь процесс проведения ремонтных работ окончен, то с помощью шаблонов проверяются все детали, относящиеся к «автосцепке СА-3». Процесс начинается с визуального осмотра, затем происходит обмер деталей, при этом применяются шаблоны. Каждый из шаблонов имеет свой номер, результат резюмируется, как проходной или непроходной.
Начиная с 1970 года, в европейских странах тоже работали над усовершенствованием конструкции автоматической сцепки. Итогом поиска и создания новых разработок стало изделие, созданное, по версии «С-АКу». Полное название на немецком языке пишется, как «Compact — Automatische Kupplung vereinfacht», что на русском языке приобретёт значение в виде «Компактного Автоматического облегчённого сцепления». За основу была взята наша советская разработка конструкция «автосцепки СА-3», поэтому европейское сцепное оборудование совместимо с нашим отечественным изделием.
Различие двух уже упомянутых версий заключается в наличии на европейской модели «C-AKv» дополнительного выступа, появившегося на зубе большого размера. Он-то и входит в пазовое специальное углубление. За счёт этого нововведения сцепление получилось весьма жёстким, а тормозные магистрали и электрические разъёмы стали соединяться в автоматическом режиме. Применяют «автосцепку C-AKv» в первую очередь при формировании крупного грузового поездного состава, поскольку винтовое оборудование такой большой нагрузки точно не выдержит.
Читайте также:
www.modelzd.ru
Автосцепка — это… Что такое Автосцепка?
Автосцепка — автоматическое сцепное устройство, которое осуществляет сцепление единиц подвижного состава без участия (либо при минимальном участии) человека. Чаще всего применяется для железнодорожного подвижного состава (вагоны, локомотивы) друг с другом. Автосцепка состоит из следующих частей: корпуса автосцепки и расположенного в нём механизма, тягового устройства с поглощающим аппаратом (пружинами), расцепного привода и ударно-центрирующего прибора. Корпус автосцепки представляет собой пустотелую стальную отливку, в головной части которой размещаются детали механизма. Если смотреть на автосцепку спереди, то у неё справа расположен большой зуб, слева-малый. Пустота между зубьями называется зевом автосцепки. Слева из зева выступает замок, в середине выходит лапа замкодержателя.
В пассажирских вагонах устраиваются, помимо поглощающих аппаратов автосцепки, центральные упругие площадки (переходы). При соединении вагонов сначала сжимаются упругие площадки, после чего уже сцепляются автосцепки, в результате этого автосцепки находятся в натянутом положении, что смягчает толчки, вызываемые зазорами между сцепляемыми поверхностями автосцепок.
Преимуществ автосцепки перед неавтоматическими сцепными устройствами (например винтовой стяжкой) достаточно много, основными из них можно считать следующие:
- Значительно снижается опасность профессии сцепщика — человеку не нужно пролезать под буферами, при ошибке сцепщика могло зажать вагонами[1].
- Повышается масса поезда за счёт более высокой допускаемой силы тяги. Это связано с тем, что максимальную прочность на разрыв винтовой упряжи ограничивает масса сцепки, которая, в свою очередь, ограничена физическими возможностями человека. В автосцепке руками берут тормозные рукава и кабели управления — но не сцепное звено.
- Сокращается время сцепки и расцепки.
- За счёт исключения буферов, функции которых выполняет поглощающий аппарат автосцепки, снижается масса тары грузового вагона.
Разновидности
Все существующие автосцепки могут быть разделены по их типу на две группы: нежёсткие и жёсткие и по принципу восприятия усилий также на две группы: тягово-ударные и тяговые.
- Нежёсткой называется автосцепка, которая допускает перемещение в вертикальном направлении её корпуса относительно корпуса смежной автосцепки в сцепленном состоянии.
- Жёсткой называется автосцепка, у которой продольная ось корпуса в сцепленном состоянии находится на одной прямой с осью корпуса смежной автосцепки, при этом исключается возможность взаимного перемещения корпусов автосцепок.
- Тягово-ударной называется автосцепка, служащая для передачи растягивающих и сжимающих усилий между единицами подвижного состава.
- Тяговой называется автосцепка, которая воспринимает только растягивающие усилия между единицами подвижного состава, а сжимающая воспринимается отдельными приборами (буферами).
Нежёсткие автосцепки:
- Автосцепка Джаннея — автосцепка с однозубым контуром зацепления. Была изобретена в США бывшим майором армии Конфедерации Эли Джаннеем (англ. Eli H. Janney), который запатентовал её 29 апреля 1873 года. Используется и по сей день на железных дорогах разных стран, в том числе и в самих США.
- Автосцепка Виллисона — автосцепка с двузубым контуром зацепления, изобретена в США в 1916 году.
- Автосцепка СА-3 — автосцепка с двузубым контуром зацепления, конструктивно является улучшенной автосцепкой Виллисона. Применяется в России, странах СНГ и Монголии. Выполняется в тягово-ударном варианте на грузовых вагонах, на пассажирских и почтово-багажных вагонах фактически работает в режиме тяговой, сжимающие нагрузки воспринимаются буферами и переходами.
Жёсткие автосцепки:
Преимущества жёсткой: допускает автоматизированное соединение рукавов и кабелей, позволяет высокие скорости, ниже износ. Преимущества нежёсткой: проще в изготовлении, возможны большие допуски, выше прочность на разрыв.
География применения
- США, Латинская Америка, Япония, Китай, Корея, Вьетнам — автосцепка Джаннея.
- Индия — винтовая упряжь и собственный вариант автосцепки Джаннея, совместимый с ней.
- Африка, Австралия — единого стандарта нет. И в Африке, и в Австралии можно найти даже такие необычные варианты сцепок, как «норвежскую» (щелевую) сцепку.
- Бывший СССР, Монголия, Финляндия — СА-3.
- Европа — винтовая стяжка. Скоростные поезда сцепляются автосцепкой Шарфенберга. На отдельных большегрузных линиях используется СА-3.
Автосцепки на других видах транспорта
Автомобильная автосцепка
Монорельсовая авто сцепка
Примечания
В этой статье не хватает ссылок на источники информации. Информация должна быть проверяема, иначе она может быть поставлена под сомнение и удалена. Вы можете отредактировать эту статью, добавив ссылки на авторитетные источники. Эта отметка установлена 13 августа 2012. |
dic.academic.ru